|
The information in this section will help you create and
edit ZLevel operations in your Manufacturing Program.
Click ZLevel
,
then select the geometry
to be machined .
A number of strategy parameters are available:
|
 |
Specify the
tool to use (you have the
choice of end mill ,
conical
or
|
|
You can also define the feedrates and spindle speeds
and transition paths in your machining operations by
means of NC macros
as needed.
See also macro parameters specific to ZLevel.
ZLevel: Strategy parameters
-
The ZLevel strategy parameters are distributed into 3
tabs.
By default, all 3 tabs are displayed with all their parameters.
However, current operations only require a reduced list of those
parameters.
-
Click <<Less to display only those current
parameters.
The Zone tab is hidden, as well as the Pass overlap
parameter in the Machining tab.
-
Click More>> to re-display all parameters.
- You can also use the modal option
User
Interface Simplified mode in the
Tools -> Options -> Machining -> Operation tab.
-
By default, all tabs and all parameters are displayed:
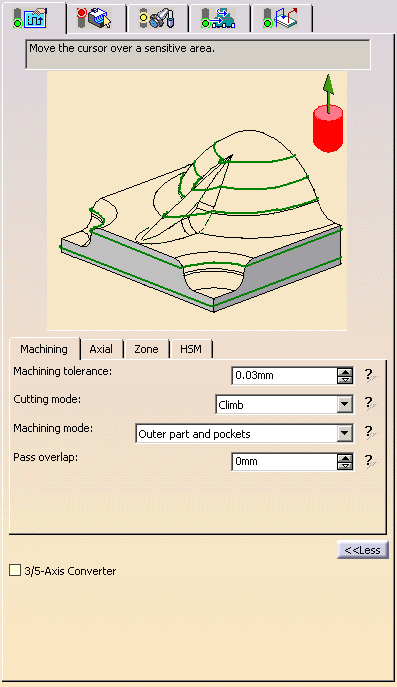
-
Click <<Less to display a reduced list of tabs
and parameters:
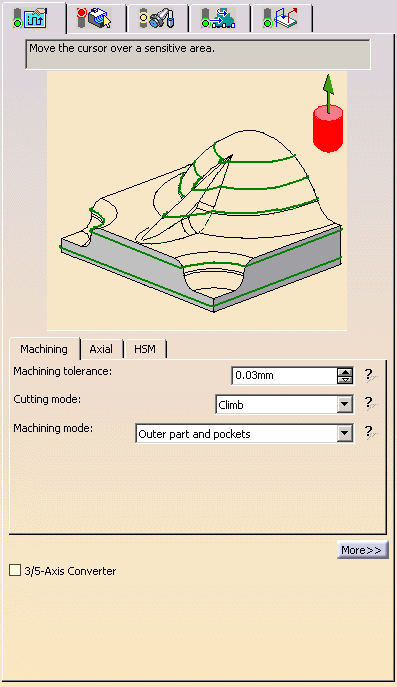
ZLevel: Machining tab
Machining tolerance
Maximum allowed distance between the theoretical and
computed tool path.
Consider it to be the acceptable chord error.
Cutting mode
Specifies the position of the tool regarding the surface to be machined.
It can be:
Machining mode
Defines the type of area to be machined:
- By plane; the whole part is machined plane by plane,
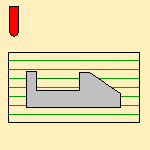
- Pockets only; only pockets on the part are machined,
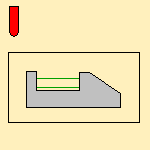
- Outer part; only the outside of the part is machined,
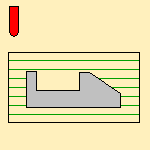
- Outer part & pockets; the whole part is machined external
area by external area and pocket by pocket.
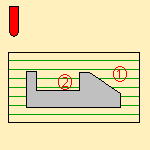
Pass overlap
Hidden when the <<Less button is pressed.
It is the width of the overlap of
the end of a pass over its beginning.
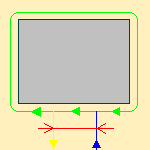
|
 |
Click
here for information about the 3/5-Axis Converter option. |
|
ZLevel: Axial parameters
All parameters remain displayed in the <<Less mode.
Stepover
|
 |
ZLevel: Zone parameters
This tab is hidden when the <<Less button is pressed.
It looks like this with a Conical tool:
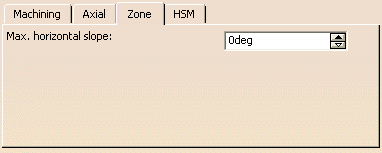

Max. horizontal slope
Maximum slope that can be considered to be horizontal (any area that is
considered to be horizontal will not be machined).
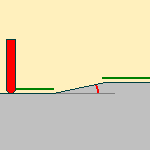
-
Use this parameter to define slope areas if you need a
quick tool path computation.
However, this computation may not be accurate since some parts of the tool
movements may be considered
as vertical although they are in horizontal areas.
-
If you require an accurate tool path computation, we
recommend that you define the slope areas with
the Machining/Slope Area action
before entering the ZLevel action.
|
 |
If you are working with a previously defined
Slope Area or Rework
Area, the Max. horizontal slope value is not editable,
since it is managed in the feature itself. |
 |
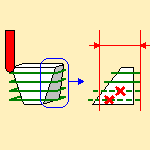
|
|
ZLevel:High Speed Milling tab
All parameters remain displayed in the <<Less mode.
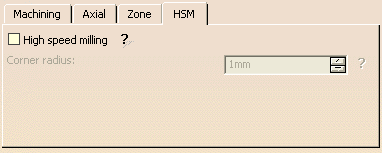
Select the check box High speed milling
to activate and define the parameters for High speed milling. Corner
radius
Defines the radius of the rounded ends of passes.
The ends are rounded to give a smoother path that is machined much faster. ZLevel: Geometry
You can specify the following geometry:
- Part with possible Offset on Part (double-click the
label)
- Check element with possible Offset on check (double-click
the label).
he check is often a clamp that holds the part and therefore is not an area
to be machined.
 |
The tool path quality is improved if check surfaces are selected. |
- Area to avoid if you do not wish to machine it (small
light brown corner near the red part selection area).
- Safety plane.
The safety plane is the plane that the tool will rise to at the end of the
tool path in order to avoid collisions with the part.
You can also define a new safety plane with the Offset option in the
safety plane contextual menu.
The new plane will be offset from the original by the distance that you
enter in the dialog box along
the normal to the safety plane. If the safety plane normal and the tool
axis have opposed directions,
the direction of the safety plane normal is inverted to ensure that the
safety plane is not inside the part to machine.
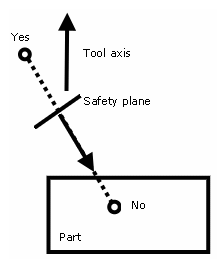
- Top plane which defines the highest plane that will be
machined on the part,
- Bottom plane which defines the lowest plane that will be
machined on the part,
 |
In standard cases, the part will be machined from the upper plane
to the lower plane, i.e. from top to bottom.
If you want to machine the part from the lower plane to the upper
plane,
simply enter the lower plane as the top plane and the upper plane as
the bottom plane. |
- Imposed plane that the tool must obligatorily pass through.
Use this option if the part that you are going to machine has a particular
shape (a groove or a step)
that you want to be sure will be cut.
 |
To use planar surfaces of a part as imposed planes:
- Select the planar surfaces,
- Select Offset in the contextual menu and enter a
value equal to the
machining tolerance + the offset value on part (if any):
- If the machining tolerance is 0.1 mm, and there is no offset
on part,
you will enter 0.1 mm as offset for the imposed plane.
- If the machining tolerance is 0.1 mm, and the offset on part
is 1 mm,
you will enter 1.1 mm as offset for the imposed plane.
This ensures that the imposed planar surface is respected to
within the offset and tolerance values. |
- Start point(s) where the tool will start cutting. There are
specific conditions for start points:
- You can select several Start points.
- The function tries to select a start point convenient for each
set of contours (islands or pockets).
if this point exists, it is used for each contour of the set.
- The group of areas (pockets or islands) affected by a start
point are determined as follows:
- The nearest group of areas is affected by the Start point. In
the image below, GZ1 is the nearest group.
- This defines a minimum distance Dmin in the image below and a
first circle with a radius equal to Dmin.
- Let's draw a second circle with a radius equal to Dmin+Tool
Diameter.
- All the groups at least partially located within the zone
defined by those two circles are affected by the Start point.
In the image below, the group GZ2 is located in that zone, thus it
is affected by the Start points.
GZ3 and GZ4 are not located within that zone, thus they are not
affected by the Start point.
- There is no restriction regarding the position of the Start
points selected.
They can be taken anywhere, even on the part, since only the
distance between the group of areas and
the Start point determines whether the pocket or the island is
affected by the Start point.
|
- Limiting contour which is the contour that defines the
outer machining limit on the part.
You can also use the
Part Autolimit option, with the Side to machine, Stop position, Stop
mode and Offset parameters.
 |
If you have selected a single face to be machined and you are not
using Part autolimit,
the tool will machine both sides of the face.
If you use Part autolimit, the tool will stop when it reaches the edge
of the face (as shown below).
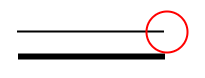
|
Subset
If you are editing a rework or a slope area, an additional information is
displayed,
ndicating which type of subset you are working on.
This field is not editable (you can not go from one subset to another).
Info
When pressed, gives the details on the parameters that were defined with
the rework area.

Appears when invalid faces have been detected.
This message disappears when you close the dialog box or when the next
computation is successful.

Appears when invalid faces have been detected and when you have decided
to ignore them.
This message remains displayed as a warning.
Click the text to switch from one status to the other.
Please refer to the
Basic
Task - Selecting Geometric Components to learn how to select the
geometry. |
 |
|
 |
|