 |
Once you have machined
a part and visually checked it, you may decide to rework certain areas
where residual material remains.
Defining a rework area allows you to focus only on the areas where
there is residual material and this gain time.
This task explains how to define and
edit an area to rework. |
 |
For CATIA V5R16 and later, the order of the subsets
Horinzontal and Vertical has been inversed. |
|
Rework areas defined on a given part can be re-used on
another part, with the following limitations:
- This re-usability is possible with a design change (i.e. evolution of
the part)
but not with a completely different part (from punch to die, for example).
- Re-usability is more uncertain if many manual divisions and/or
transfers
to other subsets have been carried out for the computation of rework area
takes those
cutting points and subsets into account, although they are no longer
relevant
if the part has changed dramatically, leading to incoherent results
(horizontal areas seen as vertical, for example).
- Those manual divisions and subsets can be removed from the original
rework area
using the Remove Cutting Points and Delete Non-updated
Subsets buttons.
The original rework area can then be re-used on another part,
provided the part is only an evolution from the original one.
|
 |
Before creating a rework area you must have executed a
Manufacturing Program. |
 |
-
Open gets2.CATPart
then select Machining > Surface Machining in the Start
menu.
-
Click Rework Area
.
Click the Part area in the sensitive icon and select the part.
-
In the dialog box that is
displayed, change the Entry diameter to 10 mm,
the Corner radius to 5 mm and the name to Rework.
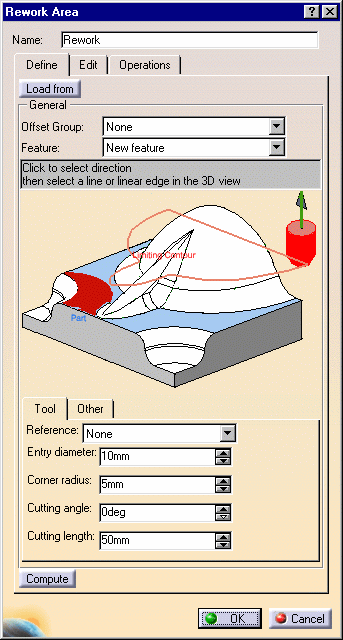
-
Click Compute to compute the rework area.
The rework area is created and can be seen in the Machining feature
view .
A progress indicator is displayed.
You can cancel the tool path computation at any moment before 100%
completion.
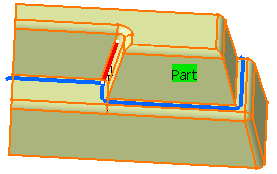
-
To edit a rework area, double-click
its name in the Machining feature view.
|
 |
The following steps are not obligatory. |
|
-
Click Load from
at the top of the dialog box to simplify
the creation of a rework area by loading all of the appropriate data from
an existing operation, tool or area.
Click the button and then select an operation and/or a tool in the
specifications tree
and/or select a machining area in the Manufacturing view.
 |
No link is kept between the rework area and the selected data
(operation, tool..).
The Load From button is only an accelerator to define the
parameters of the rework area.
It may be necessary to tune up some of those parameters to obtain a
correct result. |
-
In the Define tab,
-
Define the limit line
in order to restrict the area to be reworked.
 |
- To avoid to leave material in the rework operation, for each point
of the rework area,
we consider both the tool end point and the 2 contact points according
to it. The rework area is restricted when these 3 points are both outside the
limit line. So, the result of the restriction may create tool end points outside
the limit line.
|
-
Select the tool axis
that you used to machine the rest of the part.
-
Enter the tool data that you
used to machine the rest of the part.
-
If you wish to use a conical tool, type a positive cutting
angle. For an end mill, leave the default value of 0 degrees.
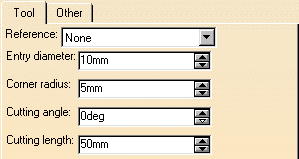
Tolerance is the
machining tolerance that you want to use for the rework area. For the sake of speed you should use the same value as for the
machining tolerance in the operation that the rework area is going to be used in.
You may decide to use a smaller tolerance in the machining area and a
larger one in the operation, reducing the operation one until you obtain satisfactory results as
regards the finish that you require.
Overlap is the
distance that you allow the tool to go beyond the boundaries of the
rework area and is defined as a percentage of the tool radius.
Part offset is
the offset that is computed for the rework area with respect to
the part.
Minimum depth filters out areas that you wish to ignore
because they are not deep enough.
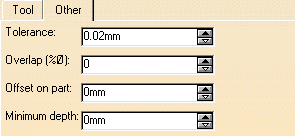
Click Compute.
-
If you find that there are too many areas to be reworked
or if you decide to concentrate on only a part of the rework area, go to the
Edit tab and
define other parameters to restrict the area to rework by creating subsets.
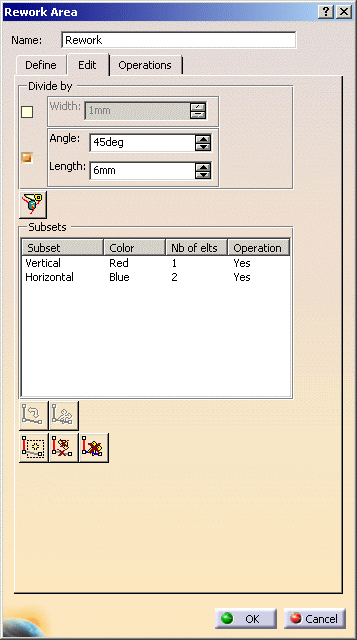
-
You can use a filter
to define a smaller area. By default, an Angle and a Length filter are proposed.
You can activate a Width filter too.
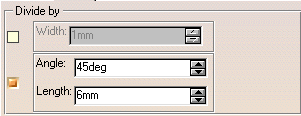
-
Click
to compute or update the subsets. The list of subsets is displayed in the dialog box, with the criterion
used for its computation, its display dolor and the number of elements in the subset.
The column Operation indicates whether an operation is assigned
to the subset.
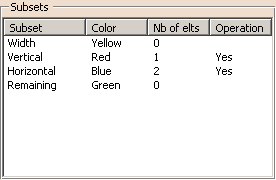
 |
An operation is effectively assigned to a subset when
an Insertion Level has been defined in
Operations tab! |
-
However, creating subsets with the above criteria may not
be sufficient. In that case, you can
split the
subsets manually, by points. Select one subset in the list, and start its contextual menu. Select
Divide by Points.
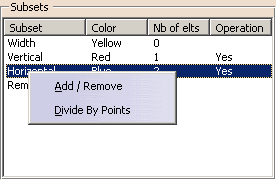
 |
The Divide By Points menu can also be reached by
. |
-
A red dot appears on the selected subset.
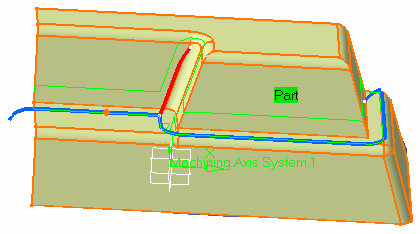
You can move the cursor along this line, to the required
place. Click the line to create the splitting point. The red dot is replaced by a white cross, the subset is split,
and the number of elements is updated in the list.
-
If you want to assign an operation to a rework area, go to
the Operations tab. First, place the cursor in the
Insertion Level field and click
in the specification tree to define where the operation is to be inserted.
The field is updated and the red arrow disappears while the Assign
Operation parameters are displayed.
-
Now, all the tools used in existing operations are
available from the Tool Reference list.
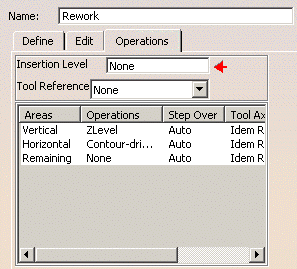
The Reference Tool
applies to all the operations to create.
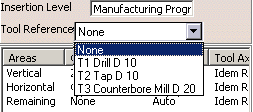
-
Select one subset to which you want to assign an operation
and define the operation parameter in the Assign Operation box that
is now available.
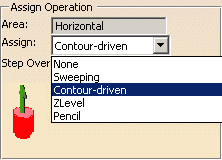
-
Select one type of operation from the Assign list, set the
Stepover value in the field below
and click the tool icon to define its axis. The list of subsets/operations is
updated accordingly.
-
To revert to an automatic step over, click
Auto. The value is replaced with the label Auto.
 |
- Use the same size of tool in a pencil
operation as that defined in the rework area in order
to reduce computation time.
You can also use a larger tool with pencil operations.
- If you choose to use a tool that is smaller than the one defined
in the rework area,
consider the rework area to be simply a set of limiting contours and
use a contour-driven operation.
- If you use a smaller tool with a pencil operation, no tool path
will be generated for the rework area.
|
-
A rework area feature can be removed in the Manufacturing view, using the
Remove
Result contextual menu.
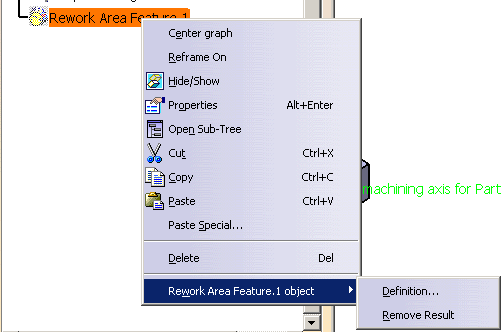
A message confirms the removal of the feature:
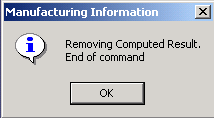
|
 |
Invalid Face
If a rework area cannot be computed
because of invalid faces,
an explicit warning message like this one will appear:
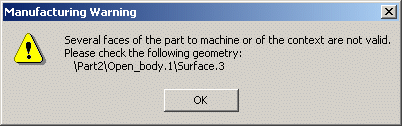
Each invalid face is highlighted in red, with an arrow pointing on it.
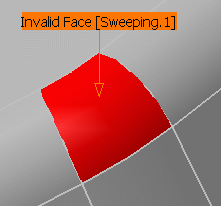
This visualization is removed when you close the main
dialog box or
when you select Remove in the contextual menu.
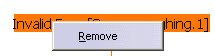
|
 |