|
The information in this section will help you create and edit Roughing
operations in your Manufacturing Program.
Click Roughing
then the geometric
components to be machined.
A number of strategy parameters are available:
- the Stepover with the Max.
distance between pass and the Tool diameter ratio.
in the HSM tab:
Specify the
tool to be used (only end mill tools
are available for this
operation)
and speeds and rates
.
You can also define transition paths in your machining operations by
means
of NC macros
as needed.
These transition paths are useful to:
Only the geometry is obligatory, all of the other requirements have a
default value.
Roughing: Machining Strategy tab
The roughing strategy parameters are distributed into 6
tabs.
By default, all 6 tabs are displayed with all their parameters.
However, current operations only require a reduced list of those parameters.
Click <<Less to display only those current
parameters.
The Zone and the Bottom tab are hidden, as well as the
Variable cut depths button in the Axial tab.
Click More>> to re-display all parameters.
You can also use the modal option
User
Interface Simplified mode
in the Tools > Options > Machining > Operation tab.
By default, all tabs and all parameters are displayed:
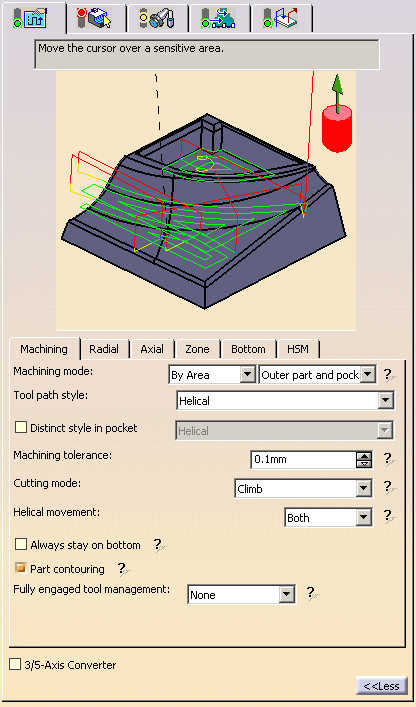
Click <<Less to display a reduced list of tabs
and parameters:
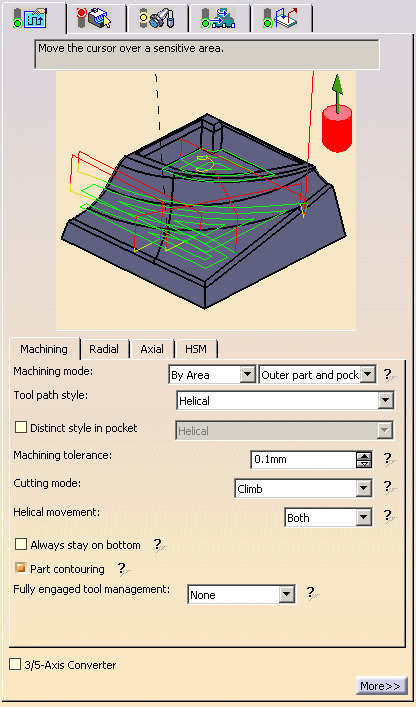
Roughing: Machining tab
All parameters remain displayed in the <<Less mode.
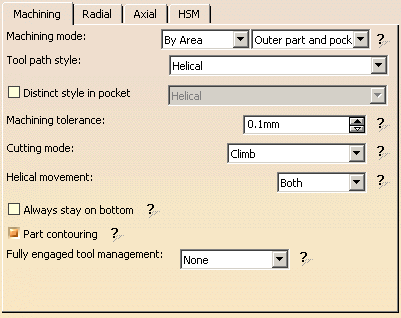
Machining mode
Defines the type of area to be machined:
- By plane: the whole part is machined plane by plane,
- By area: the whole part is machined area by area,
then
- Pockets only: only pockets on the part are machined,
- Outer part: only the outside of the part is machined,
- Outer part and pockets: the whole part is machined outer
area by outer area
and then pocket by pocket.
Please note that horizontal areas are always defined as pockets (no
distinction outer part/pocket).
To mill them as Pockets only or
Outer part areas, please use a limiting contour.
See also
Definition of Pockets and Outer part.
Tool path style
Indicates the cutting mode of the operation:
- One-way next:
the tool path always has the same direction during successive passes and
goes diagonally from the end of one tool path to the beginning of the
next.
- One-way same: the tool path always has the same direction
during successive passes
and returns to the first point in each pass before moving on to the first
point in the next pass.
- Zig-zag: the tool path alternates directions during
successive passes.
- Spiral: the tool moves in successive concentric passes from
the boundary
of the area to machine towards the interior.
The tool moves from one pass to the next by stepping over.
- Contour only: only machines around the external contour of
the part.
- Concentric: the tool removes the most constant amount of
material possible at each concentric pass.
The tool is never directly in the heart of material. It also respects the
given cutting mode in all cases.
The approach mode with this style is always Helix.
- Helical: the tool moves in successive concentric passes
from the boundary of the area to machine
towards the interior. The tool moves from one pass to the next by stepping
over.
- By Offset on part with One-Way
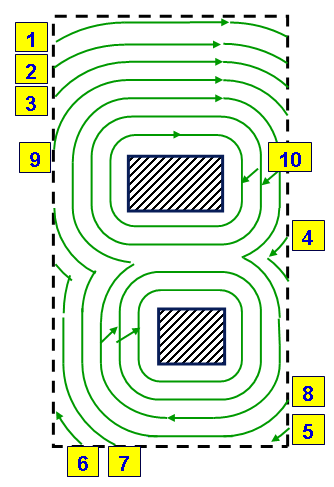
- By Offset on part with Zig-zag
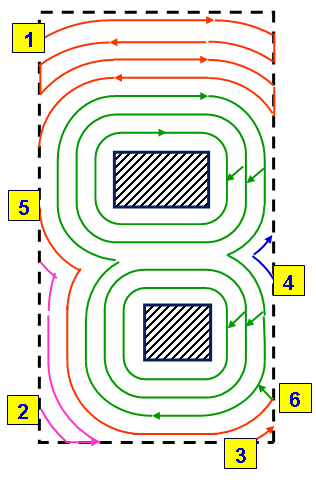
 |
- With these two tool path styles, the part is machined by
contouring passes,
offset from the part,
with high speed milling capability.
This is useful for:
- progressive milling from stock to part,
- island machining in high speed milling,
- optimized contouring tool path.
|
- These styles are available for outer part areas only.
Therefore, when the Machining mode is set to Outer
part and pockets,
the Distinct style in pocket option is automatically
selected.
- The user Start point is not used as an imposed start
point but is taken
into account to define the path start point.
- Finish passes are done after rough passes, and finish passes on
islands are
done before those on sides.
- The Cutting mode is respected for:
- each pass in By Offset on part with One-Way
mode,
- the last pass (side finish pass if it exists) in By
Offset on part with Zig-zag mode.
|
- The option Always stay on bottom is not available for
these styles.
|
Available only for the Machining
mode Outer part and pockets.
When this option is selected, you can apply a different tool path style
to pockets.
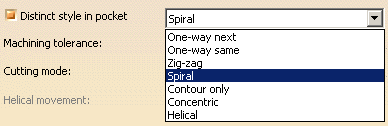
The icon icon is updated accordingly, for example:
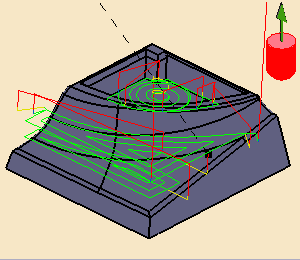
Machining tolerance
Maximum allowed distance between the theoretical and
computed tool path.
Consider the value to be the acceptable chord error.
Specifies the position of the tool regarding the surface to be machined.
It can be:
Helical movement
Specifies the way the tool moves in a pocket or an external zone. It can
be:
- Inward: the tool starts from a point inside the zone and
follows inward paths parallel to the boundary.
- Outward: the tool starts from a point inside the zone and
follows outward paths parallel to the boundary.
For pockets, the tool starts from a point inside the pocket and follows
outward paths parallel to the boundary.
For external zones, the tool starts from a point on the rough stock
boundary and follows inward
paths parallel to the boundary.
 |
In Helical mode, the control of the Non Cutting
Diameter (Dnc) has been enhanced,
in particular in the computation of the ramping approaches.
This improvement may cause a computation failure, resulting in this
specific message:
The tool core diameter is not compatible with some ramping motions. |
Always stay on bottom
This option becomes available when at least one tool path style is set to
Helical.
When machining a multi-domain pocket using a helical tool path style,
this parameter forces the tool to remain in contact with the pocket bottom
when moving from one
domain to another.
This avoids unnecessary linking transitions.
- Always stay on bottom is not selected:
- Always stay on bottom is selected:
Part contouring
Only used with the zig-zag and helical tool path styles.
With Part contouring selected, the tool goes round the outside
contour of the part before continuing
to zig-zag.
Clearing this check box allows you to gain machining time.
The tool that you are using and the part you are working on must be such
that contouring the
rough stock is superfluous.
- With Part contouring selected.
Note how the tool went round the area to machine first:
- With Part contouring cleared and exactly the same
parameters.
Note that the tool goes straight into zig-zag mode:
|
|
 |
In a roughing operation:
- each area is machined,
- then there is a contouring pass around each areas,
- followed by a contouring pass around the whole part when the remaining
material is less than the tool radius,
- approach and retract motions are computed for all those tool paths.
Starting with R17, when Part Contouring is selected, all the
tool paths around the part are chained, thus reducing the number of air
cuts as there are fewer approach and retract motions. |
|
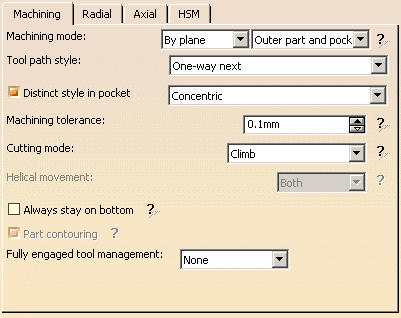
This parameter is available when:
- the
Machining mode is set to:
- Pockets only
- Outer part and pockets
- the
Tool path style is set to:
- Helical
- Concentric
- By Offset on part with Zig-Zag
- By Offset on part with One-Way
It is used to manage full material cut in hard material roughing,
where the stepover is not always respected and where the tool can be
damaged. This can be avoided by switching to a trochoid motion that reduces
the stepover, or by adding machining planes to reduce the load on the tool.
Full engagement is detected when:
- more that 75% of the tool diameter is engaged in the material,
- or more than 120 degrees of the tool is in contact with the
material
- or if the actual radial stepover is more than 75% of the
theoretical volume of material.
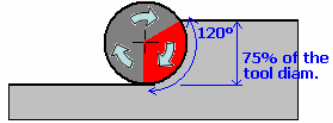
It can be set to:
- MultiPass: adds machining planes in areas where the
stepover is not respected. The distance between those additional planes is
managed by the parameter Maximum full material cut depth.
 |
- In previews and replays, a warning is displayed if Maximum full material cut depth is greater than the
Maximum cut depth.
- The MultiPass mode may be de-activated on a
given portion of the tool path when the curvilinear length of this
portion is smaller than the radial stepover value. This
de-activation avoids unnecessary approaches and retracts, when the
radial plunge of the tool into the full material is not significant.
|
|
|
Click
here for information about the 3/5-Axis Converter option.
All parameters remain displayed in the <<Less mode.
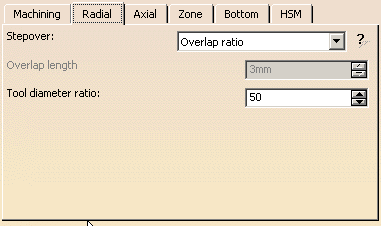
It can be
defined by:
- the Overlap ratio, i.e. the overlap between two passes,
given as a percentage of the tool diameter
(Tool diameter ratio),
- the Overlap length
between two passes given by the Max. distance between pass,
- the Stepover ratio, i.e. the stepover between two passes,
given as a percentage of the tool diameter
(Tool diameter ratio),
- the Stepover length between two passes given by the
Max. distance between pass,
|
 |
In a rework context, if the area is small enough i.e.
covered by the tool diameter,
it is deleted and replaced by an single ZLevel pass (Reduce the air cut)
and the radial stepover is not respected.
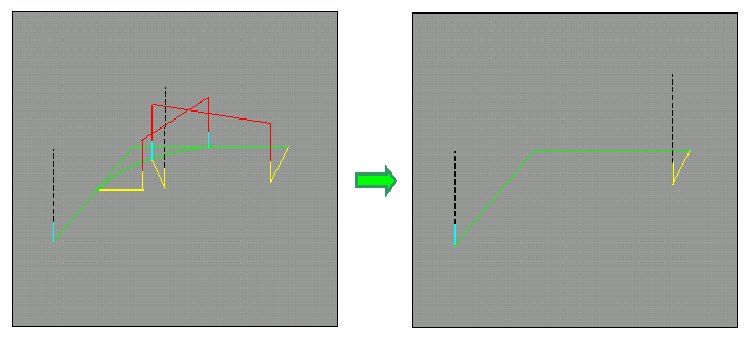
See also
Minimum thickness
to machine |
|
Roughing: Axial tab
By default, or when the More>> button is pressed:
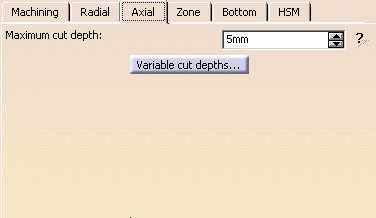
When the <<Less button is pressed:
Depth of the cut effected by the tool at each pass
Variable cut depths
Hidden when the <<Less button is pressed.
When the dialog box opens the distance between passes from
the top to
the bottom of the part is constant and is the same as Maximum cut depth.
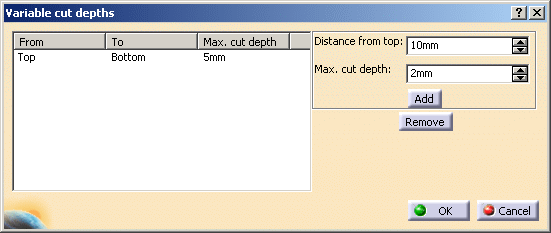
Change the Distance from top value and the
Max. cut depth value and
then press Add to give a different depth value over a given
distance.
In the example below the cut depth:
-
from the top of the part to 15mm from the top is of 2 mm,
-
from 15mm from the top to 25mm from the top is 5mm,
-
and from 25 mm from the top to the bottom of the part is
10 mm.
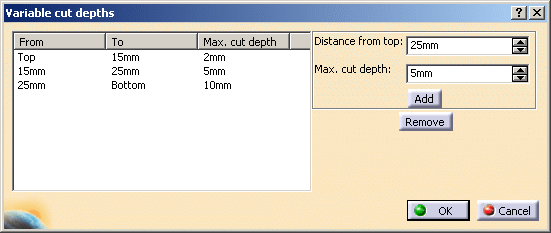
Roughing: Zone parameters
This tab is hidden when the <<Less button is pressed.
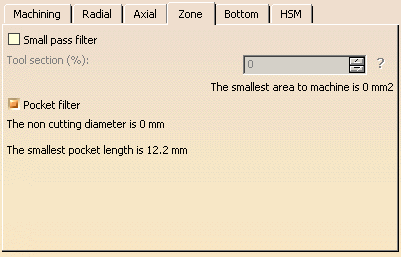
Select this check box to activate the filter
for small passes.
Then type the Tool section (%) value, which will be used to
define the smallest area
to machine according to the tool used.
This information is given below the data field.
Select this check box to activate the filter for small passes.
The non-cutting diameter of the tool can be entered in the Tool
tab,
(click More). It is given as an information only in the Zone tab.

 |
Not all pockets will be machined if there is not enough
depth for the tool to plunge.
A null value means that tool is allowed to plunge in pockets.
The size of the smallest pocket is given below the data field.
However, the smallest area to machine is taken into account only if the
area detected
has no impact on larger areas beneath.
The Tool core diameter is taken into account:
- in pockets (default operating mode),
- also for outer parts when limiting contours are used.
When areas are filtered (i.e. not machined) with the Tool core
diameter,
the areas beneath those areas are not machined. |
This tab is hidden when the <<Less button is pressed.
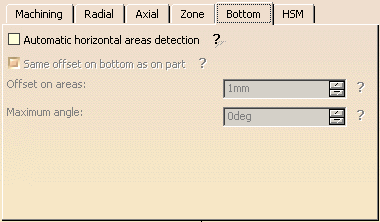
Automatic horizontal areas detection
Then type the value of the offset to apply on the areas (Offset
on areas).
The Maximum angle that
can be considered as horizontal is displayed for information only.
- If the machining mode is By area, the tool path will look
like this:
- If the machining mode is By plane, the tool path will look
like this:
The cutting planes in green are the Standard roughing tool paths,
the red ones are those computed for the horizontal areas detected. |
 |
- The computation of horizontal areas is not possible if the part is
made of a cloud of points (STL).
- This option is not compatible with the use of offset groups.
- Horizontal areas are always defined as pockets (no distinction outer
part/pocket).
To mill Pockets only or Outer part areas, please use
a limiting contour.
- When only Outer part areas are to be machined, no specific
tool path style is given for the pockets. As a consequence, if the tool
path style used for the Outer part areas is not compatible with
pockets (e.g. By Offset on part with One-Way), horizontal areas are machined with a
default tool path style (Concentric).
|
|
Same offset on bottom
as on partRoughing:High Speed Milling tab
All parameters remain displayed in the <<Less mode.
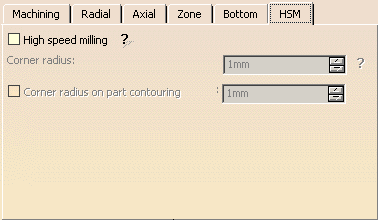
Select the check box High speed milling
to activate and define the parameters for High speed milling.
Corner
radius
Applies to Concentric, Helical, By Offset on
part with One-Way and By Offset on part with Zig-Zag tool
path styles.
Defines the radius of the rounded ends of passes when cutting with a
Concentric tool path style
and the radius of the rounded end of retracts with Helical and
Concentric tool path styles.
The ends are rounded to give a smoother path that is machined much faster.
When available and active, defines the corner radius
of all the tool paths in contact with the part. Roughing: Geometry
You can also specify the following geometry:
- Part with possible offset.
- Rough stock. If you do not have a rough stock you can
create one
automatically.
You must define a rough stock if you have not already defined one in the
Part Operation.
See the Machining Infrastructure user's guide for further information.
- Check element with possible offset.
The check element is often a clamp that holds the part and therefore is
not an area to be machined.
- Area to avoid if you do not wish to machine it (the small
light brown corner near the part selection area).
-
Safety plane. The safety plane is the plane
that the tool will rise to at the end of the tool path in
order to avoid collisions with the part.
You can also define a new safety plane with the Offset option in the
safety plane contextual menu.
The new plane will be offset from the original by the distance that you
enter in the dialog box
along the normal to the safety plane.
If the safety plane normal and the tool axis have opposed directions, the
direction of the safety plane normal
is inverted to ensure that the safety plane is not inside the part to
machine.
- Top plane which defines the highest plane that will be
machined on the part,
- Bottom plane which defines the lowest plane that will be
machined on the part,
- Imposed plane that the tool must obligatorily pass through.
Use this option if the part that you are going to machine has a particular
shape
(a groove or a step) that you want to be sure will be cut.
If you wish to use all of the planar surfaces in a part as imposed
surfaces,
select Search/View ... in the contextual menu to select
them. When searching for planar surfaces, you can choose to find
either:
- all of the planar surfaces in the part,
- or only the planes that can be reached by the tool you are
using.
Here is an example with the
gets2.CATPart.
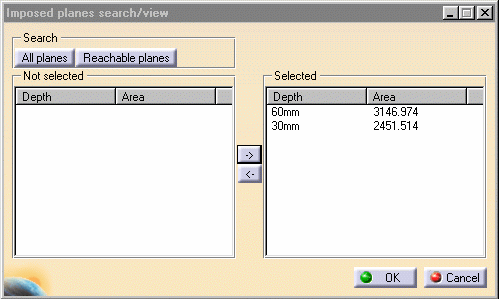 |
 |
To use planar surfaces of a part as imposed planes:
- Select the planar surfaces,
- Select Offset in the contextual menu and enter a
value equal to the
machining tolerance + the offset value on part (if any):
- If the machining tolerance is 0.1 mm, and there is no
offset on part,
you will enter 0.1 mm as offset for the imposed plane.
- If the machining tolerance is 0.1 mm, and the offset on
part is 1 mm,
you will enter 1.1 mm as offset for the imposed plane.
This ensures that the imposed planar surface is respected
to within the offset and tolerance values. |
|
|
|
|
|
|
|
|
|
|
|
|
|
- Start point where the tool will start cutting. There are
specific conditions for start points:
- Start points only concern external contours but not contouring
passes.
- They must be outside the machining limit. Examples of machining
limits are the rough stock contour;
a limit line, an offset on the rough stock, an offset on the limit
line, etc.
- They must not be positioned so as to cause collisions with
either the part or the check element.
If a start point for a given zone causes a collision, the tool will
automatically adopt ramping approach mode.
- The distance between the start point and the machining limit
must be greater than the tool radius plus
the machining tolerance. If the distance between the start point and
the machining limit is greater
than the tool radius plus the safety distance, the start point will
only serve to define the engagement direction.
- If there are several start points for a given area, the one that
is used is the first valid one
(in the order in which they were selected) for that area.
If there are several possible valid points, the nearest one is taken
into account.
- One start point may be valid and for more than one area.
- If a limit line is used, the tool will approach outer areas of
the part and pockets in ramping mode,
towards the outside of the contour.
The tool moves from the outside towards the inside of this type of
area.
In this case, you must define the start point.
|
 |
If you use a limit line or if you use an inner offset on the rough
stock,
the start point may be defined inside the initial rough stock.
The rules concerning the domain of the contour line or the offset on
the rough stock contour
line above must be applied. |
 |
- Concentric tool path style:
Start points are automatically defined. In this case, the start
point is the center of the largest
circle that can be described in the area to machine. Lateral
approach modes cannot be used.
- Spiral and Helical Tool path styles:
Whenever possible, the end of the engagement associated to the start
point corresponds to
the beginning of the sweeping path.
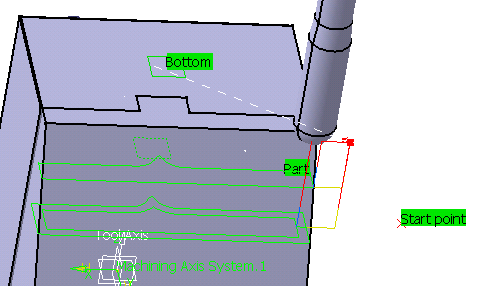 |
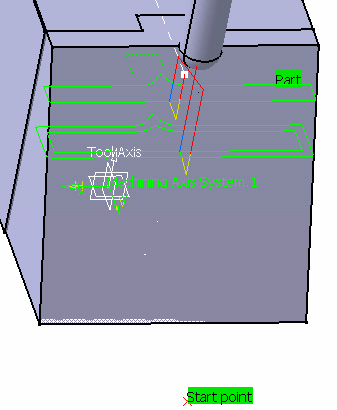 |
If this is no possible, the path will be cut to respect the
constraint imposed by the start point.
|
|
|
|
- Inner points (only active if the Drilling mode has been
selected in the Macro data tab).
There are specific conditions for inner points:
- They are usable for pockets only,
- They must not be positioned so as to cause collisions with
either the part or the check element.
If an inner point for a given pocket causes a collision, the tool
will adopt a new inner point generated
automatically.
- The inner point must lay inside the pocket and inside the portion
of the pocket that is machined.
- When you look at the part from the tool axis direction, the
inner point must lay inside each pocket
tool end contour for every
cutting plane.
- If there are several inner points for a given pocket, the one
that is used is the first valid one
(in the order in which they were selected) for that pocket.
- A point can not be valid for several pockets.
|
- Limiting contour which defines the
machining limit on the part,
with the Side to machine parameter.
|
|
|
|
There is also the
possibility of
setting the order in which the zones on the part are machined. Please refer to the
Selecting Geometric Components to learn how to select the geometry.
 Appears when
invalid faces have been detected.
This message disappears when you close the dialog box or when the next
computation is successful.

Appears when invalid faces have been detected and when you have decided
to ignore them.
This message remains displayed as a warning.
Pick the text to switch from one status to the other. Roughing: Tool/Rough Stock parameters
Position
Defines where the tool center stops:
- Outside stops the tool outside the rough stock.
The toolpath is computed as if the rough stock is increased by a value
equal to 50% of the tool diameter in each cutting plane,
- Inside stops the tool inside the rough stock.
The toolpath is computed as if the rough stock is reduced by a value equal
to 50% of the tool diameter in each cutting plane,
- On stops the tool on the rough stock.
This is the default (recommended) option.
Offset
Defines the distance that the tool can overshoot the Position.
It is expressed as a percentage of the tool diameter.
This parameter is useful in cases where there is an island near the edge of
the part and the tool diameter
is too wide to allow the area behind the island to be machined.
This parameter can only be used if the Position is inside or outside.
Minimum thickness to machine
Specifies the minimum
material thickness that will be removed when using overshoot or in a
rework operation.
- The red arrow points to the Minimum thickness to machine,
the green arrows point to the material that is not removed, the black arrow points to the material removed, the grey arrow points to the part to machine.
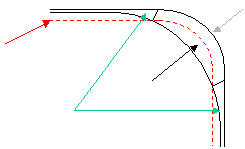
- In red, the Minimum thickness to machine,
in green, the material that is not removed,
in black, the material removed,
in grey, the part to machine.
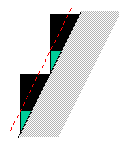
 |
- In a given level, the thickness of material left can amount up to
the value of the
Minimum thickness to machine + twice the value of the tolerance.
Therefore, on a level below you may have to mill a thickness amounting
to the value of the Minimum thickness to machine + twice the value of the tolerance of one
or several levels above.
- Minimum thickness to machine leads to select areas to
be machined depending on a specific thickness value. However, in a
roughing operation collisions with stock must be controlled and passes
are added to avoid any over height situation. Over height situations
are detected with a straight tool, as shown in the picture below:
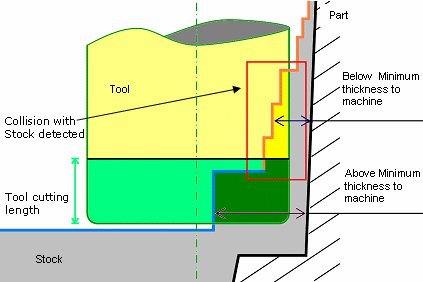
|
Limit
Definition
Defines what area of the part will be machined with respect to the
limiting contour(s).
It can either be inside or outside. In the pictures below, there are three
limiting contours on the rough stock.
The yellow areas will be machined.
Side to machine: Inside
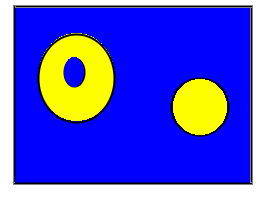 |
Side to machine: Outside
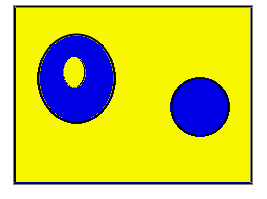 |
|
 |
- If you are using a limiting contour, you should define the start point
so as to avoid tool-material collision.
- The use of limiting contours is totally safe is the limiting contour
is fully contained by the roughing rough stock.
Example of use: restricting the machining to a group of pockets.
- But we strongly advise against using a limiting contour that is partly
outside the roughing or
residual rough stock.
Example: roughing rework or a first roughing with a complex rough stock).
In that case, we recommend that you define a surface with holes or a mask
to define the
machining zone to work on.
|
|
Offset
Specifies the distance that the tool will be either inside or outside the
limit line depending on the stop mode
that you chose.
Force replay button is
only used for reworking operations.
Its purpose is to compute the residual rough stock remaining from
operations preceding the current one,
providing a rough stock has not been defined for this operation. Use it
before clicking Tool Path Replay
.
In the Feeds and Speeds tab page, you can specify
feedrates for approach,
retract, machining and finishing as well as a machining spindle speed.
Feedrates and spindle speed can be defined in linear or angular units.
A Spindle output checkbox is available for managing output of the SPINDL
instruction in the generated NC data file.
If the checkbox is selected, the instruction is generated. Otherwise, it is
not generated.
Feeds and speeds of the operation can be updated automatically according
to tooling data and the Rough or
Finish quality of the operation. This is described in
Update of Feeds and Speeds on Machining Operation. |
 |
Feedrate reduction is not available for all tool path styles.
Feedrate management is possible for Helical, By Offset on
part with One-Way and By Offset on part with Zig-Zag
tool path styles only. |
|
Feedrate Reduction in Corners
You can reduce feedrates in corners encountered along the tool path
depending on values given in
the Feeds and Speeds tab page:
reduction rate,
maximum radius, minimum angle,
and distances before and after the corner.
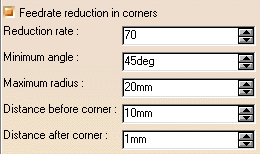
Feed reduction is applied to corners along the tool path whose radius is
less than the
Maximum radius value and whose arc angle is greater than the Minimum angle
value.
When machining pockets, feedrate reduction applies to inside and outside
corners for
machining or finishing passes. It does not apply for macros or default
linking and return motions.
Corners can be angled or rounded, and may include extra segments for HSM
operations.
1=Machining feedrate or Finishing feedrate
2=Reduced feedrate
A=Distance after corner
B=Distance before corner
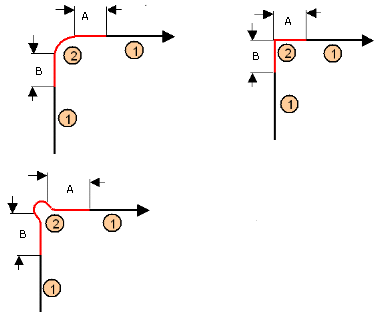
Slowdown Rate
You can use Slowdown rate in the Feeds and Speeds tab page to
reduce the current feedrate
by a given percentage.
In Helical tool paths, the reduction is applied to the first
channel cut.
Combining Slowdown Rate and Feedrate Reduction in
Corners
If a corner is included in a Slowdown path, the general rule is that the
lowest percentage value
is taken into account.
For example, if the Slowdown rate is set to 70 % and Feedrate reduction
rate in corners is set to 50%,
the feedrate sequence is:
100%,
70% (entry in slowdown),
50% (entry in corner),
70% (end of corner, still in slowdown),
100% (end of slowdown).
If Feedrate reduction rate in corners is then set to 75%, the feedrate
sequence is:
100%,
70% (entry in slowdown),
70% (entry in corner: 75% ignored),
70% (end of corner, still in slowdown),
100% (end of slowdown). Roughing: Macro data
For more information on how to save or load an existing macro,
please refer to
Build and use a macros catalog.
In addition to the automatic macros listed below,
you can insert pre-and post-macros using the
Build by user graphic mode.
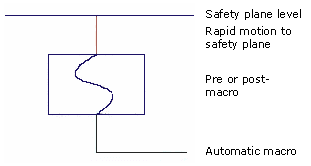
|
 |
If the last motion of the pre- or post-macro is above the safety plane
level,
there will be no rapid motion to the safety plane. |
|
Optimize retract
This button optimizes tool retract movements.
This means that when the tool moves over a surface where there are no
obstructions,
it will not rise as high as the safety plane because there is no danger of
tool-part collisions.
The result is a gain in time. |
 |
- The parameter Optimize retract takes the rough stock left
by the previous operation into account.
- If you have defined a safety plane, you should deactivate the
Optimize retract option.
If you do not, the safety plane will be ignored.
|
|
Axial safety distance
Maximum distance that the tool will
rise to when moving from the end of one pass to the beginning of the next.
Mode
Specifies the engagement of the tool in the material:
- Plunge; the tool plunges vertically,
- Drilling; the tool plunges into previously drilled holes.
You can change the Drilling tool diameter,
Drilling tool angle and Drilling tool length,
 |
Helix retracts are inserted into the toolpath when using Helical
mode (only when retracts begin on the part).
But when a Drilling macro is selected, not all Helix retracts are
inserted. |
- Ramping; the tool moves progressively down at the
Ramping angle,
- Helix; the tool moves progressively down at the ramping
angle with its center along a (vertical)
circular helix of Helix diameter.
Those four approach modes apply to pockets.
- If the tool Path is Concentric, the approach is always
Helix, either on outer areas or pockets.
- Ramping approach mode applies to pockets but also outer areas in given
conditions:
- If a limit line is used, the tool will approach outer areas of
the part and pockets in ramping mode.
- If a lateral approach is not possible (due to the check
element), the approach is made in ramping mode.
|
Approach distance
Engagement distance for plunge mode.
Radial safety
distance
Distance that the tool moves horizontally before it begins its approach.
|