|
How to Define a Rib
To define a rib, you need a center curve, a planar profile and possibly
a reference element or a pulling direction.
You can combine the different elements as follows:
|
Closed Profile |
Open Profile |
Open Center Curve |

|

(Existing material) |
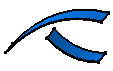 (Thick Profile
option, no existing material) |
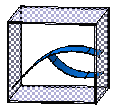
(Thick Profile option, existing material)
|
Closed Planar Center Curve |
 |
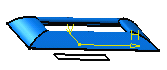 (Thick Profile
option, no existing material) |
Closed 3D Center Curve |
|
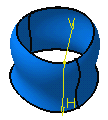 (Thick Profile
option) |
About Profiles
- In some cases, you can define whether you need the whole sketch, or
sub-elements only. For more information, refer to
Using the Sub-elements of a Sketch.
- Clicking the icon
opens the Sketcher . You can then edit the profile. Once you have done
your modifications, you just need to quit the Sketcher. The Rib
Definition dialog box then reappears to let you finish your
design.
- If you launch the Rib command with no profile previously
defined, just click the icon
to access the Sketcher and then sketch the profile you need.
-
You can also create your profile by using any of these
creation contextual commands available from the Profile field:
-
Create Sketch: launches the Sketcher after
selecting any plane, and lets you sketch the profile you need as
explained in the Sketcher User's Guide.
-
Create Join: joins surfaces or curves. See
Joining Surfaces or Curves.
-
Create Extract: generates separate
elements from non-connex sub-elements. See
Extracting Geometry.
If you create any of these elements, the application then
displays the corresponding icon in front of the field. Clicking this icon
enables you to edit the element.
If you have chosen to work in a
hybrid design environment, the elements created on the fly via the
contextual commands mentioned above are aggregated into sketch-based
features.
- You can use an open profile provided existing material can trim the
rib. For more information, refer to Trimming
Ribs or Slots.
- Ribs can also be created from sketches including several profiles.
These profiles must be closed and must not intersect. For example,
you can easily obtain a pipe by using a sketch composed of two concentric
circles:
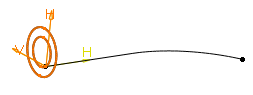
|
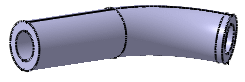
|
Profiles |
Result |
Center Curves
Before using center curves, the following rules
should be kept in mind:
- 3D center curves must be continuous in tangency
- If the center curve is planar, it can be discontinuous in tangency.
- center curves must not be composed of several geometric elements
Profile Control
You can control its position by choosing one of the following options:
- Keep angle: keeps the angle value
between the sketch plane used for the profile and the tangent of the
center curve.
- Pulling direction: sweeps the
profile with respect to a specified direction. To define this direction,
you can select a plane or an edge. For example, you need to use this
option if your center curve is a helix. In this case, you will select the
helix axis as the pulling direction.
- Reference surface: the angle value
between axis h and the reference surface is constant.
- Contextual commands creating the directions
you need are available from the Selection field:
- Create Line: For more information, see
Creating Lines.
- Create Plane: see
Creating Planes.
- X Axis: the X axis of the current coordinate system
origin (0,0,0) becomes the direction.
- Y Axis: the Y axis of the current coordinate system
origin (0,0,0) becomes the direction.
- Z Axis: the Z axis of the current coordinate system
origin (0,0,0) becomes the direction.
- Create Join: joins surfaces or curves. See
Joining
Surfaces or Curves.
- Create Extrapol: extrapolates surface boundaries or
curves. See
Extrapolating Surfaces and
Extrapolating Curves.
If you create any of these elements, the application then displays the
corresponding icon in front of the Selection field. Clicking
this icon enables you to edit the element.
If you have chosen to work in a hybrid design
environment, the elements created on the fly via the contextual
commands mentioned above are aggregated into sketch-based features.
-
Move
profile to path: easily associates profiles with center curves but
also allows a single sketch to be swept along multiple center curves.
This option can be accessed if Pulling direction of
Reference surface is already on, and builds the
profile with the following understanding:
- The origin of the sketch plane (i.e. 0,0) will be swept
along the path.
- The vertical axis of the sketch plane (i.e. 0,1) will be
kept parallel to either the pulling direction (if the profile control
is set to Pulling direction) or the normal to the
Reference surface (if profile control is set to Reference surface).
In this example, the profile to be swept is a
square (shown by the arrow). The circles which belong to the same
sketch are used as center curves and plane yz is set as the pulling
direction. |
 |
Once the geometry is selected and Move
profile to path on:
- the moved profile turns blue,
- a blue arrow is displayed at the origin of the
transformed profile. Clicking on this arrow reverses the profile
direction and rotates it 180 degrees about the pulling direction.
-
an orange arrow is parallel to the pulling direction. Clicking on
this arrow reverses the profile direction and rotates it 180
degrees about the blue arrow.
|
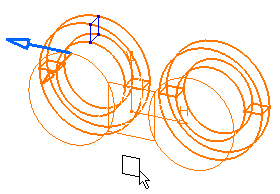 |
The resulting rib looks like this: |
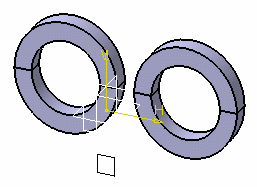 |
Merge Rib's Ends
The Merge rib's ends option is to be used in specific cases. It
trims each extremity of the rib to existing material, starting from the
profile position until the first limit encountered on existing material
in each direction. For more information, see
Trimming Ribs or Slots.
Recommendation
It is recommended that the profile be on the center curve in a plane
normal to the center curve. Otherwise, it very often leads to an
unpredictable rib shape.
The position of the profile in relation to the center curve determines
the shape of the resulting rib. When sweeping the profile, the application
keeps the initial position of the profile in relation to the nearest point
of the center curve. The application computes the rib from the position of
the profile.
In both examples below, the application computes the intersection point
between the plane of the profile and the center curve, then sweeps the
profile from this position. |
|
In this particular
example, the profile is not located on the center curve. Is this context,
the shape obtained is unpredictable.
Keep in mind that when the profile is not on the center curve, even if
you use any of the Profile control options (Keep
angle, Pulling direction,
Reference surface) , you cannot predict the
final rib shape. The use of the Profile Control options never
helps in anticipating the final rib shape. Consequently, it is preferable
not to use such profile types. |