|
The information in this section will help you create and
edit Spiral milling operations in your Manufacturing Program.
Click Spiral milling
, then select the
geometry to be
machined .
A number of strategy parameters are available:
Specify the
tool to use
(the tools that can be used with this type of operation are end mill tools
, conical tools
,
face mill tools ,and
T-slotters ),
the feedrates and spindle speeds ,
You can also define transition paths in your machining operations by
means of NC macros
as needed.
Spiral Milling: Strategy parameters
-
The Spiral Milling strategy parameters are distributed
into 5 tabs.
By default, all 5 tabs are displayed with all their parameters.
However, current operations only require a reduced list of those
parameters.
-
Click <<Less button to display only those
current parameters.
-
The Axial tab is hidden, as well as
-
Reverse tool path button in the
Machining tab,
-
View direction is the Radial tab,
-
Click More>> button to re-display all
parameters.
- You can also use the modal option
User
Interface Simplified mode in the
Tools -> Options -> Machining -> Operation tab.
-
By default, all tabs and all parameters are displayed:
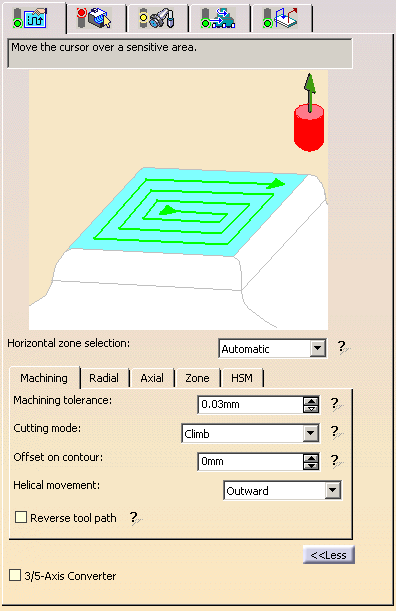
-
Click <<Less to display a reduced list of tabs
and parameters:
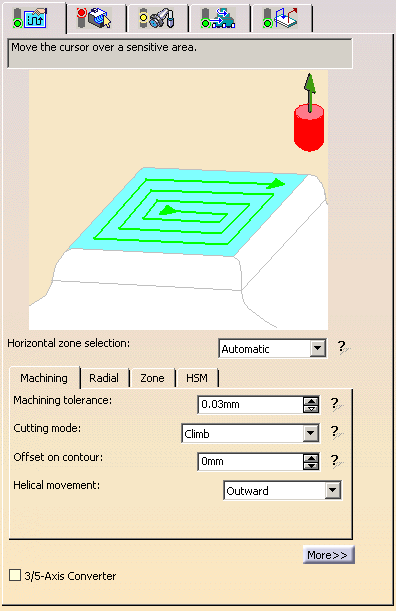
Horizontal zone selection
Specifies whether the horizontal zones are detected automatically or
by means of the guide contours given by the user.
- Automatic: the surfaces that are considered to be
horizontal with respect
to the maximum angle are automatically selected for machining.
- Manual: A red contour lights up in the sensitive icon.
Click it and then
select the contours that will form the limit to the area you want to
machine.
The selection takes account of all the surfaces inside the limit,
horizontal or not.
- You can also define more than one contour.
Defining another contour inside the original contour will have the effect
that only the area between
the two contours (i.e. inside one and outside the other) will be machined.
- The blue contour represents the first contour,
-
the black contour represents the second contour,
-
and the yellow
area represents what will be machined
.
|
Spiral milling: Machining
parameters
Machining tolerance
Maximum allowed distance between the theoretical and
computed tool path.
Consider it to be the acceptable chord error.
Specifies the position of the tool regarding the surface to be machined.
It can be:
Offset on contour
Tool offset with respect to the contour,
Helical movement
- Outward: the tool path will begin at the middle of the area
to machine and work outwards.
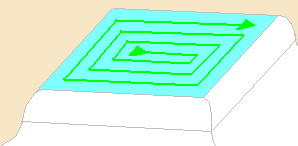
- Inward: the tool path will begin at the outer limit of the
area to machine and work inwards.
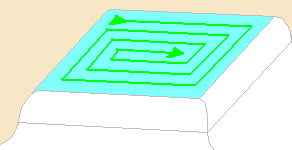
Reverse tool path
Hidden when the <<Less button is pressed.
Reversing the tool path means that a tool path that goes from right to
left will now go from left to right
and vice versa.
Click
here for information about the 3/5-Axis Converter option.
Spiral milling: Radial
parameters
Max. distance between pass
Distance between successive passes in the tool path.
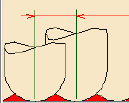
Hidden when the <<Less button is pressed.
- Along tool axis
is used to compute the stepover distance, as if you were looking along the
tool axis.
- Other axis is
used to compute the stepover distance, as if you ware looking along an
axis other than the tool axis.
The icon at the top of the tab for axis selection has changed and you can
now select an axis
(the oblique axis in the icon) other than the tool axis for the view
direction.
 |
 |
Other axis can only be used with a ball-nose tool. |
Collision check
When Other axis is active, select this check box to
search for
toolholder-part collisions. Spiral milling: Axial Parameters
This tab is hidden when the <<Less button is pressed.
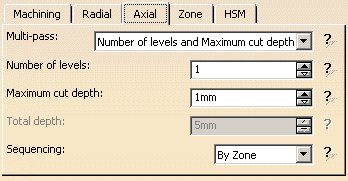
Multi-pass
Use the list to select the mode of input:
- Maximum cut depth and total depth:
Enter the Total depth
and the Maximum cut
depth
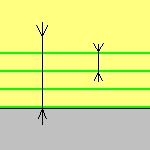
- Number of levels and total depth: 1
Enter the Number of
levels and the Total depth.
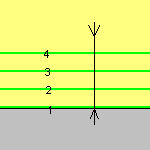
- Number of levels and Maximum cut depth:
Enter the Number of levels and the Maximum cut depth.
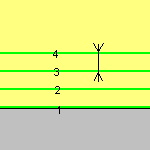
Only two can be selected at time, you select which two via the input mode
choice.
The example below was obtained with 3 levels at a cut depth of 5mm,
but could just as easily have been obtained by:
- A cut depth of 5mm and a total depth of 15 mm,
- or a total depth of 15 mm and 3 levels.
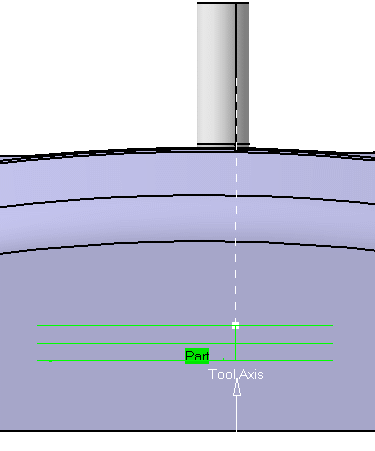
Sequencing
Use the list to select the type of sequencing:
- By Zone:
The multi-pass machining is done zone by zone, all the levels are created
on the first zone,
then on the following zone, etc...
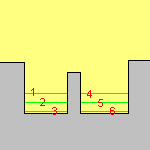
- By Level:
the upper level is created on the first zone, then on the second zone,
etc.
Then the second level is created on the first zone, then on the second,
etc...
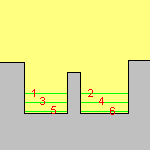
Spiral milling: Zone parameters
All parameters remain displayed in the <<Less mode.
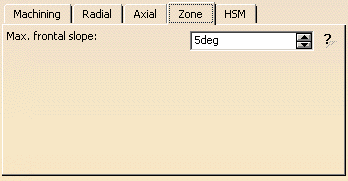
Max. frontal slope
Maximum angle that can be considered as horizontal.
The angle is measured perpendicular to the tool path.
Spiral milling: HSM parameters
tab
All parameters remain displayed in the <<Less mode.
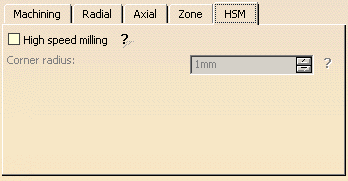
High speed milling
Activates the High speed milling option
Corner radius
Rounds the ends of passes.
The ends are rounded to give a smoother path that is machined much faster.
 |
With HSM and helical mode, the corner radius must be less than half
the stepover distance.
It will be forced to this value. |
Spiral milling: Geometry
|
|
You can specify the following geometry:
- Part with possible offset on the part (double-click
the label)
- Check element with possible offset on the check element
(double-click the label).
The check is often a clamp that holds the part and therefore is not an
area to be machined.
- Area to avoid if you do not wish to machine it
(light brown area in the left hand corner near the part selection area).
- Safety plane. The safety plane is the plane that the tool
will rise to at the end of the tool path in
order to avoid collisions with the part. The safety plane contextual menu
allows you to:
- define an offset safety plane at a distance that you give in a
dialog box that is displayed.
The new plane will be offset from the original by the distance that you
enter in the dialog box along the normal
to the safety plane. If the safety plane normal and the tool axis have
opposed directions, the direction of the
safety plane normal is inverted to ensure that the safety plane is not
inside the part to machine.
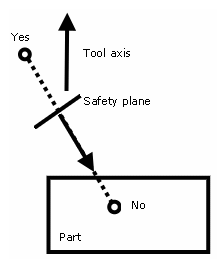
Note that when an Approach/Retract macro is set to None, the safety
plane is not reached.
See the Macros Parameters
chapter for more information.
- Top plane which defines the highest plane that will be
machined on the part,
- Bottom plane which defines the lowest plane that will be
machined on the part,
- Limiting contour which defines the outer machining limit on
the part.
You can also use the
Part Autolimit option, with the Side to machine, Stop position, Stop
mode and Offset parameters.
Subset
If you are editing a slope area,
an additional information is displayed, indicating which type of subset you
are working on.
This field is not editable (you can not go from one subset to another). Please refer to the
Basic
Task - Selecting Geometric Components to learn how to select the
geometry.
 Appears when
invalid faces have been detected.
This message disappears when you close the dialog box or when the next
computation is successful.

Appears when invalid faces have been detected and when you have decided
to ignore them.
This message remains displayed as a warning.
Click the text to switch from one status to the other. |