|
Several commands in the Mold Tooling Design (all commands adding a
component to a mold, the component edition commands, the Add New Instance,
Replace Reference) share the same dialog box, with a display adapted to the
specificities of the command. You will find below a description of this
dialog box.
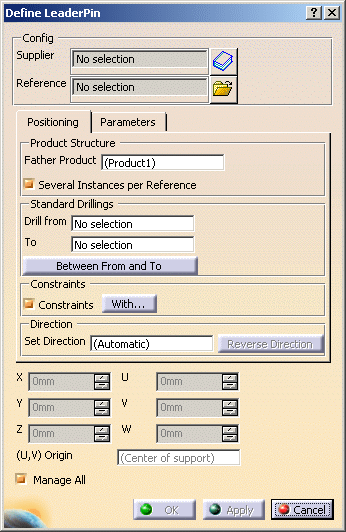 |
 |
The title of the dialog box varies with the command |
|
Config
The catalog icon
starts the catalog browser to select a
Tooling
Component Template.
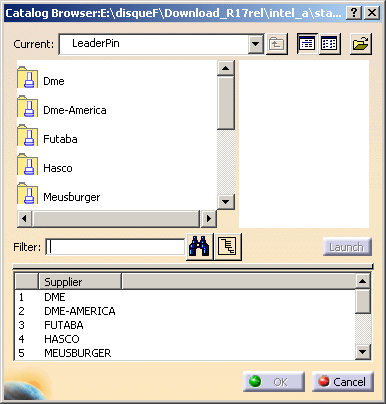
The File Open icon
starts the File Selection box to let you select your own
component.
Your selection is displayed in the Supplier and the
Reference text fields.
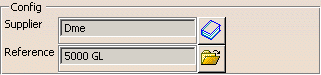
Product Structure

Father Product defines the position of the element in the
specification tree, either automatically, or as you define it.
- If the Drill From field is defined with an element, the
Father Product is either the Father Product of that element or
the active product if there is one.
- If the Drill From field is not defined and if the
corresponding product exists, the Father Product is defined by
the following rules:
- if the component is an Angle Pin, an Eye Bolt, an Inter lock or a
Sprue Bushing, the Father Product is InjectionSide
- if the component is a Baffle, a Ring or a Plug, the Father
Product is EjectionSide
- if the component is a Core Pin, an Ejector, an Ejector Sleeve, an
Ejector Pin, a Flat Ejector, a Knock Out, a Puller, a Stop Disk or a
Support Pillar, the Father Product is EjectorSystem
- if the component is a slider, the Father Product is
Mold.
- For the edition and Add New Instance commands, the
Father Product is the selected instance.
- Otherwise, the Father Product is the active product.
You can also select an element in the specification tree as the Father
Product.
|
 |
- You cannot select the Father Product in the 3D viewer.
- To ensure compatibility with DMU Kinematics, you are not allowed
to change the Father Product of a slider.
- The value of Father Product is not modal, it is defined
each time you enter a dialog box.
- All previewed instances are created under the same Father
Product.
- All components created at the same time are created under the same
Father Product.
- All instances of a single reference are created under the same
Father Product.
- The Father Product of a component cannot be modified
after the component has been instantiated.
|
|
Several Instances per Reference
Allows you to create
several instances of one reference component.
If you deactivate this option,
only one instance will be created per reference component.
This option overrides the same setting in Tools/Option and
is only applied to the current creation.
- if this check box is selected all the instances of the component that you create will have the
same reference:
The logical computations will be the same for each
instance. - If this check box is not selected, each instance of the component
that you create will have its own reference:
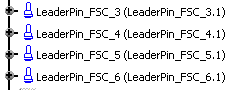
|
 |
We recommend not to activate Several Instances per
Reference for components to be split, each instance needs its own
surface splitting result. |
|
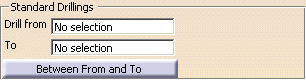
|
 |
Standard Drillings is not accessible:
|
|
The component instances can be classified by their type of
associated drillings:
- no drilling: the component instance has no association,
- drillings are set by the command Distributed Drill Component:
The component instance has a detailed association.
- drillings are set by the Drill from, To Between From
and To fields and the Drill Component command: the component instance has a standard
association.
|
|
Here are the specifities of the Standard Drillings fields: Drill from and To:
- used to define drillings,
- may be used to define the alignment direction.
To:
- used to compute the min, max of the filter for screw length.
Drill from:
- May be used to define constraining elements,
- Deduced from:
- Used to define position of the component instance in the specification
tree, after OK.
This applies to the case of creation of an instance based on a new
reference only,
not to the case of an instance based on an already instantiated reference.
- In planar mode, it is initialized by the positioning part.
It is not initialized in point mode.
Between From and To starts the Define All Component to
cross dialog box:
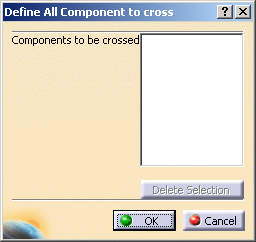 We
recommend to define the drillings for all previewed instances.
If this does not meet your needs, create the instances in several stages, or
edit them afterwards.
In the Add component and Add New Instances commands, the drillings are
defined for all previewed instances.
In the edition command, one instance is edited at a time, provided it does
not have a detailed association.
If it has sister instances, they are not
modified. |
 |
If you have created taps with the command Drill Component,
editing those taps with Between From and To will transform
those taps into simple drills.
|
|
Constraints

|
 |
Constraints is not accessible in the
Replace Reference command. |
|
Please see the chapter Constraints for more
information. The Constraints check box is selected by default.
The button With... starts the Constraining Components
dialog box
that lets you define the constraining components.
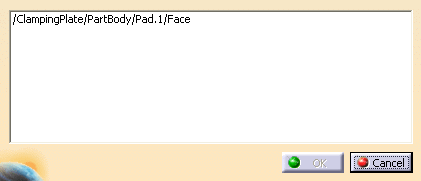
- The check box Constraints applies to all previewed
instances.
- Modifying the constraint of one instance has no effect on the
constraints of sister instances of the selected instance.
- Information displayed in this box is related to the current preview.
- Except for the Edition commands, constraints do not exist in the
tooling assembly in most cases.
They will be created when you click OK to exit the dialog box.
- The nature of the constraint is not displayed.
- The element in the Tooling Component which is constrained (e.g. base
point … ) is not displayed:
- it does not exist yet in the Tooling Assembly in many cases, because
you are often working with previews,
- you already know it: it is often the Tooling Component base point.
- Entering the planar mode or the point mode redefines the current
constraints.
- In local mode, current constraints are defined by analogy with the
ones of the selected instance, if any.
- Constraining elements can be replaced at any time with the With
button, provided that only one constraint is displayed and that the rules are respected.
|
 |
- In some cases, the requested constraints cannot be created, e.g.
when the constraining product is different from the Father
Product.
- If you have created constraints in the tooling assembly by a
method other than Constraints and With... in this dialog box, those
constraints are displayed in the Define Constraint Components
dialog box, but will be deleted when you click OK in planar
or point mode.
|
|
Direction

Direction defines the alignment direction.
|
 |
- Direction is not accessible in the
Replace Reference command.
- Direction is not accessible when it is not compatible
with the component constraints.
- The alignment direction applies to all previewed instances.
|
|
Note that the first selections in the 3D viewer are dedicated to this
definition:
- when you pick an axis, it becomes the alignment direction, and its
name is displayed in the Set Direction field.
- if you pick another axis, it becomes the new alignment direction, and
its name is displayed in the Set Direction field.
- if you do not pick an axis, the alignment direction is defined by
default, and Set Direction displays (Automatic). See
Adding Components.
- the definition of the alignment direction is finished when you pick
a point or a face (see Working Modes)
Another possibility is to define the Drill from and the
To fields in Standard drillings
before any selection in the 3D viewer.
Reverse Direction lets you invert the direction. Anchor
Point Position
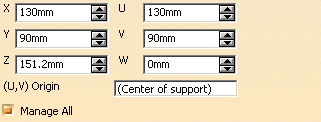
It is expressed in the compass coordinate system (X, Y, Z) and in the local
axis system related to the dialog box (U, V, W). The local axis system
remains the same until you close the dialog box. By default:
- the (U,V) Origin is the center of the positioning plane,
- U and V directions are the main directions in the positioning plane,
- W is the alignment direction and its origin is equal to its
intersection with the positioning plane.
You can modify the (U,V) Origin:
- by picking a line, an axis or an edge: its intersection with the
positioning plane will define the (U,V) Origin.
- by picking any point, even outside the positioning plane: its normal
projection on the positioning plane will define the (U,V) Origin.
The position of the anchor point can be changed using the
manipulators in the 3D viewer (the dialog box is updated), or by direct
input in the dialog box.
|
 |
The active instances are red, the inactive ones are green. |
|
When this option is active:
- selecting a 2D point will effectively select all of the other 2D
points in the mold and create an instance of the component on each of
them,
- selecting a dedicated 3D point will select all of the dedicated 3D points on the same
face.
|
 |
Note that this behavior is specific to dedicated 3D points, i.e.
3D points renamed after the component created.
If the 3D points on the face have no specific names, they will not be
selected in one shot. |