 |
Insert SCENARIO01.model from the samples folder. |
 |
Use the Fit All In icon
to
position the model geometry on the screen. |
 |
(Optional)
You can manage automatically your Thickness
result as alternate shape of the initial component.In
this case, the thickness result will be automatically reinserted and will
replace the initial component (provided the Activate check box
is selected, it is by default)
Note: If your are not working in alternate shape
mode, it is strongly recommended to use the Reference Product
option to avoid positioning problems when reinserting products. Please read
About Reference Product
In our example, the Manage Alternate Shape option is
activated for Thickness. |
|
-
Click the Thickness icon
from the DMU Optimizer toolbar.
The Thickness dialog box is displayed.
-
Select the surface(s) you want to work on (i.e.
SCENARIO01.model) in the specification tree or in the geometry area.
 |
Note: only 2D surface(s) can be selected. |
About selection:
You can select any node within the specification tree
(terminal/non terminal) and even multi-select them provided that you
are not working in alternate shape mode. |
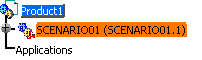 |
-
Enter the Offset values:
For instance: Offset 1=2mm
Offset 2=0mm
|
 |
Setting the Offset values:
Depending on the surface design, you can define any value meeting your needs (negative, positive, or null).
Please refer to More About Thickness |
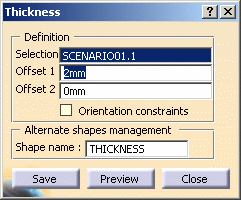 |
-
Click Preview to generate the thickness
representation. The preview window is displayed.
-
Zoom to visualize better the thickness result:
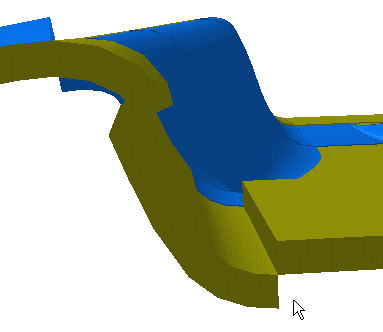 |
If you are not satisfied with the result (because of gaps
between surface patches or bad offset orientation)
You can turn on the Orientation constraints option |
Orientation Constraints
- The Orientation constraints option is disabled by default. (The
default normal vectors are used)
- Through this functionality, you can define the orientation of
the offset (on every surface patch).
- If you select the
Orientation constraints check box (without defining
additional vectors): the normal vector orientation is done
automatically. The first normal vector found defines the
reference orientation which is propagated to the neighboring
surfaces.
- If the automatic propagation is still incomplete (for
example, certain surfaces are not correctly connected), you need
to define manually normal
vectors.
|
You are still in the Thickness command. |
-
Select the
Orientation constraints check box in the dialog box still displayed:
 |
 |
If you change any of the dialog box parameters, the initial
representation is displayed |
-
Click Preview.
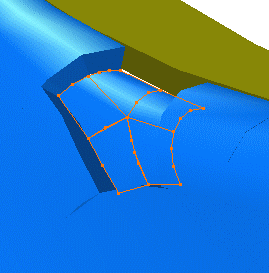 |
The Propagation is not complete.The surfaces concerned are
highlighted. |
-
Select the Orientation constraints check box again to
define constraints on the original representation.
-
Define constraint
vectors for the corresponding surfaces in the document window:
- Drag the cursor onto the surface.
- When you are satisfied, use the left mouse button.
The constraint vector is created.
|
 |
At anytime, you can delete a constraint vector, what you need to
do is to click on the white square
Note that if you click the arrow, you reverse the constraint vector
orientation. |
-
Click Preview when done. The calculation is
based on the orientation of the constraint vectors.
This time, the result is correct (there are not any highlighted surfaces
displayed):
-
Click Save.
The Save As dialog box is displayed:
- Identify the folder in which you want to save the file
- Enter a file name
|
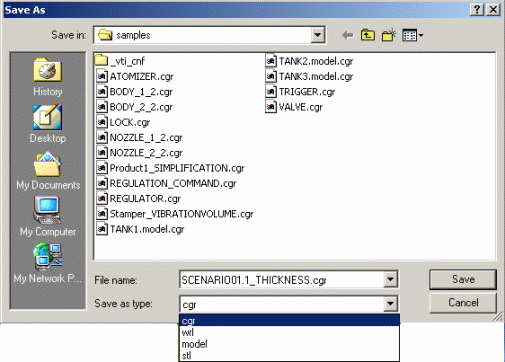 |
-
Click Save.
-
Click Close to exit the thickness command
|
 |
Alternate Shape:
(Optional)
You can manage your Thickness result as an alternate shape
For this:
- Select Tools->Options from the menu bar.
The Options dialog box appears:
- Expand the Digital Mockup category from the upper-left tree.
- Select DMU Optimizer item to display the corresponding tab.
The Alternate Shapes Management is available
- Select the Thickness check box: the thickness is
automatically activated as an alternate shape
The Thickness result will be added as a new representation of the
initial component.
For more details, please refer to Customizing DMU Optimizer Settings and
Managing
as an Alternate Shape.
|
 |
Remember you can customize thickness settings
at any time. |
|