
|
The 3D Multi-Splice feature is
created and includes:
-
the selected plies,
-
the splicing curves,
-
the staggering value,
-
a staggering direction per
curve,
-
the overlapping value,
-
an overlapping direction per
curve.
Sub-plies (also
called cut-pieces) are created under each ply and have the following
characteristics:
-
they inherit the
material and direction of the ply,
-
their contour is
associative with the father ply geometry in the following cases:
-
the ply surface is
modified,
-
the ply geometry
is modified e.g. the boundaries of the plies are modified or a limit
contour is applied to the ply,
Note however that
the number of cut-pieces is not modified during the update of the part,
e.g.:
Original situation
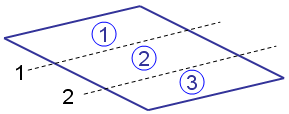 |
Situation after update
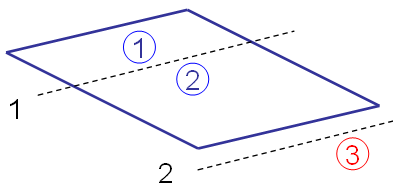 |
Curve 2 no longer intersects the father ply geometry
The limit contour feature of cut-piece 3 will have an update error
You must delete the cut-piece manually. |
-
they have their
own rosette and producibility feature,
-
they have their
own geometry and can be modified individually,
-
They are taken in account in the following commands:
Ply exploder
Limit contour
Core sampling
Numerical analysis
Material excess
Skin swapping
Creates manufacturing Document
Synchronizes this document
-
they can be used
for any manufacturing export,
-
they can be
transferred in the manufacturing model if generated in the engineering
model.
|