 |
This task shows how to perform a numerical analysis in order to compute
the area, mass, center of gravity and mass on a ply, a sequence, a plies
group, or a stacking. |
 |
Available in Composites Design (CPD), Composites Engineering Design (CPE) and Composites Design for Manufacturing (CPM),
in a CATPart context.
Available in DMU Composites Review (CPR), in a CATProduct
context.In Composites Design (CPD), Composites Engineering Design (CPE) and Composites Design for Manufacturing (CPM),
the numerical analysis is done on the CATPart.
The result can be stored in the CAPTPart (select the Persistent
check box).
In DMU Composites Review (CPR), the numerical analysis can
be performed on the whole CATProduct or on a selection of CATParts under the
CATProduct. However the numerical analysis result will not be stored in the
CATProduct: the Persistent check box and OK are
disabled. |
 |
Open:
-
Part_01.CATPart
from the samples\Composites directory if you are
working in CPD, CPE or CPM.
-
CPD_01.CATProduct from the samples\Composites directory if you are
working in CPR.
|
 |
-
Click the Numerical Analysis icon
.
The Numerical Analysis dialog box is displayed.
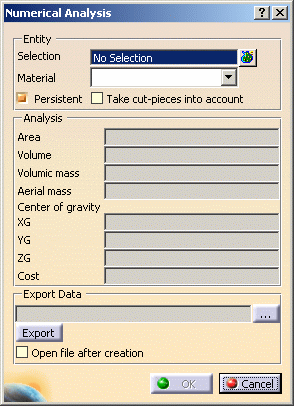
Note that the Persistent check box is not active when you are
in DMU Composites Review (CPR).
-
Click
and select the entities to be
analyzed.
In CPD, CPE or CPM,
you can select the staking or a portion of it.
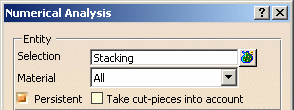
In CPR you can select either the
whole CATProduct
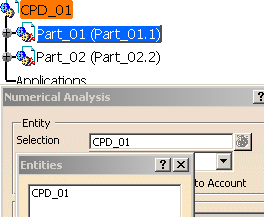
or one or several CATParts under this CATProduct.
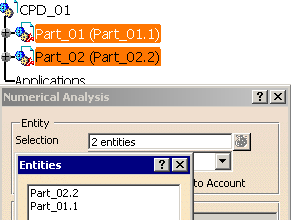
If you select an entity under a CATPart, the CATPart itself is
automatically selected.
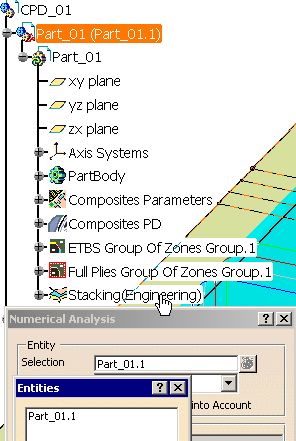 In our example, we selected the Stacking node. The analysis is automatically started, displaying the
results in the Analysis frame.
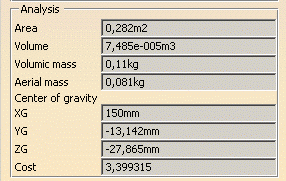
-
Click to select Take cut-pieces
into account.
The analysis is updated with the information concerning the
cut-pieces.
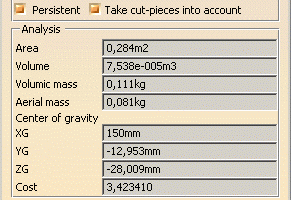
You will note that the area increases due to the
plies superposition.
The numerical analysis of all the plies can now be exported in an external
file (.xls or .txt). The default path is the path where the sample is
stored.
-
Click Export to export the analysis result.
An information message is displayed when data is successfully exported.
Here is the information contained in the external file:
- in DMU Composites Review (CPR):
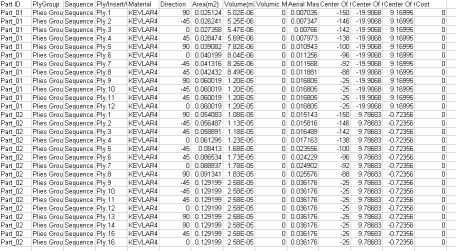
- In Composites Design (CPD), Composites Engineering Design (CPE) and Composites Design for Manufacturing (CPM):
|
-
Select a Material (as defined in the Material
catalog) from the drop-down list if you want to filter the results.
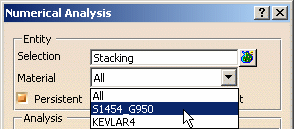
The data retrieved for each material enables you to create
bills of material.
|
|
|
 |
Filtering through Material is only possible if you selected at
least a stacking
as input.
|
|
-
Check the Persistent option if you want the
analysis to be featurized and to be displayed in the specification tree.
This check box is not available in DMU Composites Review
(CPR) as the numerical analysis result cannot be stored in the
CATProduct.
-
In Composites Engineering Design (CPE) and Composites Design for Manufacturing (CPM),
click OK to exit the command and store the numerical analysis
under the CATPart.
The Numerical Analysis element is displayed in the Stacking node under
each sequence containing the selected above Material.
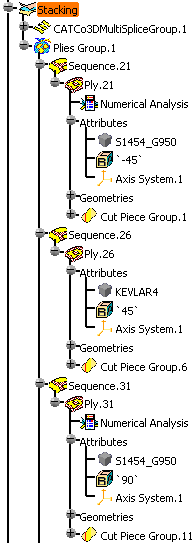
In DMU Composites Review (CPR), click Cancel to
exit the command. The numerical analysis result are not stored under the
CATProduct.
|
 |
- You can perform a numerical analysis on a cut-piece.
- If you select Take cut-pieces into account for a ply
containing cut-pieces, the computation is made from the cut-pieces
geometries. Otherwise, it is made from the ply geometry.
- Even if Persistent is selected, no numerical
analysis feature is created under each cut-piece.
|
 |