 |
The Draft Both Sides
capability allows you to generate drafted faces on each side of a parting
element you determine.
This task includes two scenarios.
|
 |
Open the
Draft4.CATPart document. |

|
Using Two Different Computation Modes
-
Click Draft Both Sides
in the Advanced Dress-up Features toolbar
.
The Draft Both Sides dialog box is displayed.
By default, it is expanded to let you see helping
images. In the default helping image, the text in red indicates the
geometry you need to select. Conversely, the text in green indicates the
geometry already selected by default. Helping images vary according to
the parameters you set during your design.
A default pulling direction (xy plane) is displayed in
the geometry.
Selecting Less hides the dialog
box 2D viewer. Note that the last state of this 2D viewer is memorized
when the dialog box is closed by clicking OK. As a result,
once you are familiar with the Draft Both Sides capability and
you no longer need helping images, just minimize the dialog box before
clicking OK.
-
To draft two faces with reflect lines, keep
Reflect/Reflect, which is the default option,
on. Using this option, the neutral faces are the
filleted edges and the faces to draft are automatically defined by the
neutral elements as being the tangent faces.
-
To be able to specify two different angle values select
Independent in the Computation method
combo list.
The helping image reflects the parameters you have selected and the
dialog box now displays two angle value fields:
-
Select Parting Element and select the green
surface as the parting element.
As indicated in the helping image, the "Parting Element"
text is now in green, indicating that the required geometry has been
selected.
-
Click the Neutral Element 1st Side field and
as the neutral element you need, select the fillet as shown:
-
In the 1st Side Angle field, enter 6 as the
draft angle value you want to assign to this face.
-
To define the second face you want to draft, click the
Neutral Element 2nd Side field and select the second fillet.
-
In the 2nd Side Angle field, enter 10 as the
draft angle value you want to assign to this face.
Both faces to be drafted are now selected. The application displays the
reflect line in pink.
-
Click OK to confirm.
Two faces on each side of the parting element are drafted. Each of
them is assigned a distinct angle value.
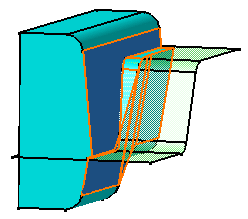 |
|
Due to the use of the different angle values you have
set, this operation results in a "step" where both drafted faces
meet. |
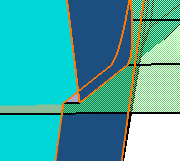 |
-
Double-click the draft feature in the
specification tree to remove this step.
-
Set the Fitted option. This option adjusts the resulting faces on the parting element you
chose.
|
 |
Using the Parting Line Adjustment Option
You will use Parting Line Adjustment to ensure
that later on you will be able to apply machining techniques onto the part.
To illustrate that option, let's consider the part we used in the previous scenario.
-
Double-click Draft.1 in the specification tree
to edit it.
-
Enter 17 degrees to change the draft angle value you
previously set to the draft.
-
This excessive value does not reflect angle values
designers usually use, but this lets us quickly see what happens next.
You obtain a draft which is not satisfactory. As indicated by the arrow,
the curvature radius would invalid any machining process because it is
too small:
-
Click the More tab.
-
Keep 0.1mm as the parting line adjustment value.
-
If you click Top View
in the View toolbar, the curvature radius causing trouble for
being too small, becomes more visible, as pointed to by the arrow:
-
Now, changing the parting line adjustment value to 0.7 mm
would add material up to the curve pointed to by the arrow. Consequently,
the curvature radius would be more acceptable.
-
Changing the parting line adjustment value to 0.9mm would
let you obtain an even larger curvature radius:
Concretely speaking, when setting the parting line
adjustment parameter, you define a length value that sets a maximum
thickness to be added to the draft to enlarge the wrong curvature radius.
As illustrated in the case just above, that length is represented by
L. The chosen value is 0.9mm, which means that L might be 0.9mm or
even a little bit less.
Considering the rest of the curvatures of the draft feature, depending on
the part shape, that thickness will most often be thinner, but will never
exceed the value you entered.
Methodology
The Parting Line Adjustment option thus adds
material to the part. If then you decide to use it, you should keep in
mind that you need to enter reasonable values not to add too much
material prior to machining processes. Usually, 0.1mm set as the default
value provided by the application, proves to be efficient most of the
time.
Concerning draft angle values, again make sure the value
you enter does not add too much material. In the worst cases, this would
prevent you from removing parts from molds.
In other words, a successful draft operation requires a
fine tuning between the draft angle value you set and the parting line
adjustment you may perform. The challenge being to add the minimum
material to the part.
Useful Tools
Remember that you can always check curvatures by
performing
Surface
Curvature Analyses and draft validity by using the
Draft Analysis capability.
Mode
The application offers two modes:
-
Reflect/Reflect: the neutral faces are the
filleted edges and the faces to draft are automatically defined by the
neutral elements as being the tangent faces.
-
Neutral/Neutral: the neutral selected faces can
be propagated by tangency, and the faces to draft can be defined either
by the user or automatically by the neutral elements.
When this mode is chosen, radius values are displayed in the geometry
Computation Method
Three computation methods are available:
-
Independent: you need to specify two angle
values, as shown in the scenario above.
-
Driving/Driven: the angle value you specify
for one face affects the angle value of the second face.
By default, 1st Side Driving is the
selected side, meaning that the angle value you specified for the face
selected first is the driving value. You can change and select 2nd Side
Driving instead.
Sometimes, some resulting faces of the "Driven draft" are not apt for
being removed from molds. In this case, we recommend you to check this
using the
Draft Analysis capability.
-
Fitted: performs a draft operation on two opposite sides of
the part while adjusting the resulting faces on the parting element you
chose.
|
 |
-
-
-
|
|
Pulling Direction
Contextual commands creating the reference elements you need are
available from the Selection field:
-
Create Line: For more information, see
Creating Lines.
-
Create Plane: see
Creating Planes.
-
X Axis: the X axis of the current coordinate system origin
(0,0,0) becomes the direction.
-
Y Axis: the Y axis of the current coordinate system origin
(0,0,0) becomes the direction.
-
Z Axis: the Z axis of the current coordinate system origin
(0,0,0) becomes the direction.
If you create any of these elements, the application then displays the
corresponding icon next to the Selection field. Clicking this
icon enables you to edit the element. |
|
Editing Drafts Created Via Advanced Draft
Double-clicking on both side draft features created using
Advanced Draft
displays the Draft Both Sides dialog box in which changing
parameters will be done more easily. |
 |
Automatic Relimitation
|
|
-
-
|
|
|