 |
This task shows you how to create
a connector. Connectors can only be created on objects that have existing
geometry that satisfies the rules of connector creation. If existing
geometry is not present, you will have to create the geometry. |
 |
1. |
If the resource is not active, make it active
by double-clicking in the specifications tree. |
|
2. |
Click the Build Connector
button. This will bring up the Manage Connectors dialog box. |

|
|
You will not be able to add a connector on
the instance of a standard part (a 'non-unique' part) using the Build
Connector command. You need to use the Define Connectors
sub-command in the Create Part dialog box. If you try to add a
connector to a standard part using the Build Connector command
then you will get an error message. The Build Connector
command can be used to add connectors to a part that is unique -
meaning it has one reference and one instance only.
The Manage Connectors dialog box will list all connectors on
the selected part. To see a connector and its associated geometry on the
part, select a connector from the list.
Adding a connector is explained below; Delete, Modify and Duplicate are
explained elsewhere in this section. To
Publish a connector means you are allowing people who do not
have write access to your document to establish a connection. This is
explained further in Using Work Packages. You
can Publish or Unpublish connectors using the two buttons.
|
|
3. |
Click the Add button. The Add
Connectors box displays. NOTE: The Define Connector Geometry options will
not be available if you are placing a connector on a light object. For more
information see Creating Connectors on Light
Parts. 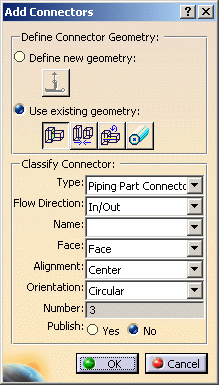
Select the type of connector - piping, HVAC, etc.
In some applications the flow direction field will be available.
The piping (or tubing) part connector has flow direction built in and you
must select a flow direction also from the drop down menu. The mechanical
part connector has no flow direction.
Another type of connector - the nozzle
connector - will be available if you are placing a connector on a nozzle. A
nozzle connector must be placed on the end of the nozzle that
connects to equipment. A part connector is placed on the end that
connects to the pipe or duct.
An electrical part connector
should only be placed on a socket. The electrical part connector should be
placed on the end of the socket that connects to equipment. A cableway part
connector should be placed on the free end of the socket that does not
connect to equipment.
When you are placing a connector on a Bendable, such as a
bendable pipe, you must use the Define New Geometry option. You must
not use existing geometry to place the connector.
You can name each connector by selecting in the Name field. This is
useful for some functions, such as designing using a schematic. See
Customizing 2D and 3D Connector Names for
more information.
The concept of Publishing or Unpublishing a connector is explained
above. Check the checkbox as necessary.
Face, orientation and alignment are explained below. |
 |
The orientation,
alignment and face must be defined correctly before a connector can be
created. To explain what these are, the face is the surface to which you
attach a connector. As an example, if you want to attach a clock to your
office wall, the wall is the face. You want the numeral "12" to be up, so
you orient the clock accordingly. This is the orientation. The alignment is
the direction in which the clock face is pointed - normally it would be
perpendicular to the wall. When creating a connector, the alignment always
has to be perpendicular to the face.
The connector must always be created pointing out of the part. Do not
create a connector where the alignment vector points into the part. The face is generally defined using a face of the part, such as the end
of a pipe. Alignment is usually defined using a line, such as the not-shown
line along the centerline of a pipe. Orientation is defined using the xy
plane, or another plane or face to define an "up" direction.
In the illustration below the Z axis indicates the alignment of the
connector. It also indicates the direction in which routing will occur.
The X and Y axis together define the orientation. They are useful when
attaching two resources.
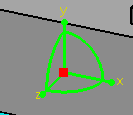
It is necessary to select geometry in the part to which you want to
attach a connector so that these three characteristics are correctly
defined. If the part does not have the necessary geometry then you must
create it. |
|
4. |
If you want to create a connector using the
part's existing geometry click the Use existing geometry option.
Click the Select
Face button to select a face. Selectable faces will highlight as you
move your pointer over the part.

Click this button to
select the alignment. You will only be able to indicate the alignment by
selecting a line - from the construction geometry, or elsewhere in
the part if there is one. You can only select a line that is perpendicular
to the face plane.
Click this button to
select the orientation. You will only be able to select a plane that is
perpendicular to the face you selected. If you cannot find a plane to
select, click the Swap Visible Space button (see below) to make
the construction geometry visible, and select a plane.
Some
connector types require you to place a datum
point. The datum point is placed by clicking this button and then clicking
a 3-D point on the part. The datum point is used as follows:
- Lofted reservation section: Datum is used to define where the spline
will start and end when creating lofted reservations.
- Hangers: See Hanger Design documentation.
- All applications with flexibles: The datum point is placed in two
situations: (1) Datum is used to define where the spline
will start and end when creating flexible tubes. (2) It is recommended
that you place a datum point on each part connector to which a flexible
may be routed. This is needed to allow a flexible to update when you
move a part in a design.
You can display the part construction geometry, if there is any, to make
it easier to select existing geometry. Do this by:
- Right click on the part entry in the specifications tree.
- Click Hide/Show. The part will disappear from the screen.
- Click the Swap Visible Space button
. The part will
reappear on your screen with the construction geometry visible. Clicking
the button again will toggle you back.
|
|
5. |
The fields under Classify
Connector will become available after you have successfully selected the
geometry explained in Step 4. Click on the down arrows to make your
selection.
Select a type.
For Flow direction, select In, Out, InOut or None.
Select the Face type. A Hole connection allows a routable to pass
through it - it is useful for placing parts like clamps along a run without
cutting a tube. A Face connection will stop a routable and not allow it to
pass through.
Select an alignment.
Choose an orientation: Circular will allow the connector to attach to
another connector at any orientation; round ducts and pipes, for instance,
do not need a well-defined "up" direction because they can rotate. A
Rectangular orientation is used for parts like rectangular ducts; they do
not have a strict ''up" direction. Up allows the connector to attach to
another connector or part in the up position: horizontal trays, for
instance, require a well-defined "up" position. You can also use the "up"
orientation for a hole connector. In the image below, the connector on the
right has the up orientation, the connector on the left does not.
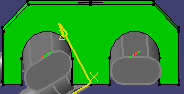
The number in the Number field is assigned by the application. This can
be significant because when you are creating a new connector, you have the
option of using the alignment and orientation used in the previous
connector after you select the face. You can choose to do this, or select a
new alignment and/or orientation. |
|
6. |
Click OK. The new
connector will be listed in the Manage Connectors box. |
|
7. |
To
define new geometry for placing a connector, select the option
Define new geometry, then click on the Select plane button
. The
Define Plane box will display.
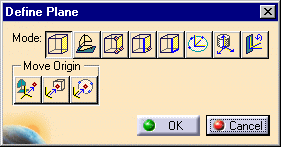
|
|
8. |
Use the functions provided by the
Define Plane box to reposition the connector, if necessary, as explained
below. (The colors of the buttons may be slightly different in some
applications.)
Click the Define Plane button to redefine the plane as well as
the origin by clicking once on the face.
Click the Define Plane using Compass button to redefine the
plane using the compass.
Click the Define 3-point Plane button to define the plane by
clicking on any three points with your pointer. The connector will be
placed on the first point you click.
Click the Define Line-Point Plane button to select the plane by
clicking on a point and a line, like an edge. The connector will be placed
on the first point you click.
Click the Define Line-Line button to select the plane by
clicking on two lines. The plane will be defined by the first line
selected. But if the two lines are parallel the plane will be defined as
the plane in which both lines exist.
Click the Define plane at center of circle button to select the
plane by clicking three points on the edge of a circle. This method is used
for
multi-CAD documents, usually for CGR circles. You can click at points
where two lines meet or in the center of a face. The Z axis of the
plane manipulator will be placed according to the right hand rule. If you
click clockwise the Z axis will point into the object. If you click
counter clockwise the Z axis will point out from the object.
Click the Define plane at product origin button and then the
object to place the plane manipulator on the origin of the object. The
plane manipulator axis will match that of the product.
Click the Define Orientation button to change the orientation.
Click the button and then click a point or a line. If you click a point the
X axis will point to it. If you click a line the X axis will become
parallel to the line.
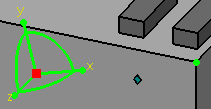
Use the Move Origin buttons to define the plane.
Define Origin at
Plane or Compass allows you to define the origin using the compass or plane
command. You use the compass or plane as the base plane along which the
origin can be selected.
Define Origin at
Point or Center of Face lets you select the origin by clicking on a point
or face. Define
Origin at Center of Circle allows to select the origin by clicking at three
points - the origin will be placed in the center of an imaginary circle
drawn using those three points. The plane and orientation will not change
when using this command. |
|
9. |
Click OK. The connector
will be placed and the Add Connector dialog box will display again.< |
|
10. |
Make your selections in the fields
under Classify Connector as described in Step 5. Click OK. |
 |