|
The information in this section will help you create and edit a sweeping
operation into your Manufacturing Program.
Click Sweeping
, then
the geometry of the part
to machine ,
A number of strategy parameters
are available in:
Specify the
tool to be used
( you have
the choice of end mill
or conical tools
for this operation),
the feedrates and spindle speeds .
You can also define transition paths in your machining operations by
means of NC macros
as needed.
Sweeping: Strategy tab
-
The Sweeping strategy parameters are distributed into 5
tabs.
By default, all 5 tabs are displayed with all their parameters.
However, current operations only require a reduced list of those
parameters.
-
Click <<Less to display only those current
parameters:
-
Click More>> to re-display all parameters.
-
You can also use the modal option
User
Interface Simplified mode in the
Tools -> Options -> Machining -> Operation tab.
- Click <<Less to display a reduced list of tabs and
parameters:
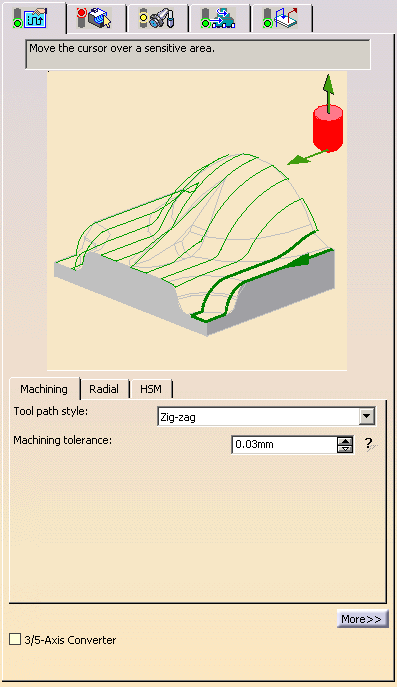
Sweeping: Machining parameters
Tool path style
- One-way next: the tool path always has the same direction
during successive passes and
goes diagonally from the end of one tool path to the beginning of the
next.
- One-way same: the tool path always has the same direction
during successive passes and
returns to the first point in each pass before moving on to the first
point in the next pass.
- Zig-zag: the tool path alternates directions during
successive passes.
Hidden when the <<Less button is pressed.
If you have selected a one-way Tool path style, select the Plunge mode:
- No check: the tool can plunge and rise with the surface,
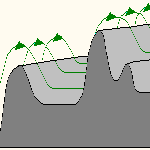
- No plunge: the tool cannot plunge,
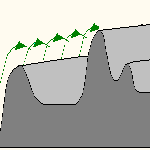
- Same height: the tool does not plunge but will not stop
when it encounters a peak.
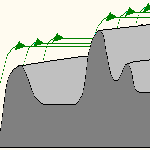
Machining tolerance
Maximum allowed distance between the theoretical and computed tool path.
Consider it to be the acceptable chord error.
Reverse tool path
Hidden when the <<Less button is pressed.
Max Discretization
Hidden when the <<Less button is pressed.
For some surfaces, such as flat surfaces, the tool path can suffer from a
lack of points.
By setting the maximum discretization distance (Step),
the gaps will be filled by the exact surface points
resulting in a better distribution of points, a smoother tool path and
then a better machining quality.
In addition, two Distribution Modes
are available to improve the quality of the machined surface:
- With Aligned, the points of the tool path are aligned
(as best as possible)
with those of the tool paths below and above.
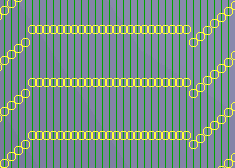 |
Resulting surface
(Zoom on details) |
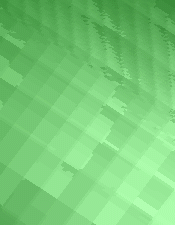 |
|
- With Shifted, the points of the tool path do not form a
line
with those of the tool paths below and above.
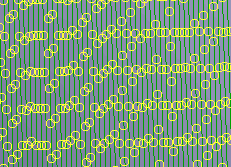 |
Resulting surface
(Zoom on details) |
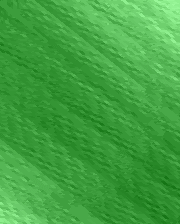 |
|
|
|
Click
here for information about the 3/5-Axis Converter option.Sweeping: Radial parameters
Use the list
to select either:
- Via scallop height:
The stepover is computed from the scallop height you have set,
within the range defined by Max. distance between pass and
Min. distance between pass.
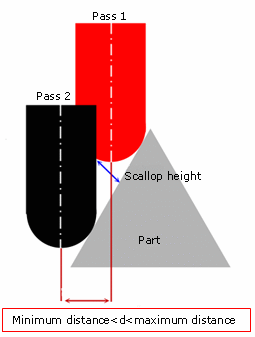
All selected geometries are taken into account in the
stepover computation even if these geometries are not milled.
For example, filled holes or vertical walls outside the limiting contour
influence the stepover computation and
may generate useless paths.
The by-pass consists in not selecting these useless geometries to compute
the toolpath.Maximum distance between pass
Minimum distance between pass
Minimum stepover distance if you chose Via Scallop height.
Scallop height
Value that you define for the
maximum allowable height of the crests of material left uncut after
machining.
Stepover side
Can be left or right and is defined with respect to the machining
direction.
View Direction
- Hidden when the <<Less button is pressed.
- Use Along tool axis
when you want to machine along the axis you have selected
(or along the default axis).
- Other axis can only be
used with a ball-nose tool.
When it is selected, the axis/direction icon lets you define a second axis
(the other axis - the one pointing up to the left).

Collision check
Activating Other axis displays a button for
collision checking.
When this is turned on, all of the points where the toolholder would have
collided
with the part are displayed on the tool path (after Replay). Sweeping: Axial Parameters
This tab is hidden when the <<Less button is pressed.
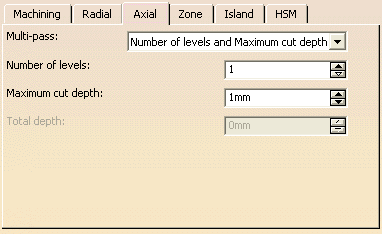
Multi-pass
Use the list to select the mode of input:
- Maximum cut depth and total depth: Enter the
Total depth and the
Maximum cut depth
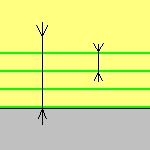
- Number of levels and total depth: Enter the
Number of levels and the
Total depth.
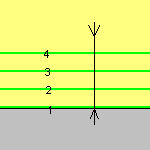
- Number of levels and Maximum cut depth: Enter the
Number of levels and the Maximum cut depth.
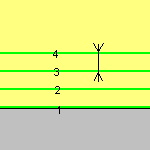
Only two can be selected at time, you select which two via the input mode
choice.
The example below was obtained with 3 levels at a cut depth of 5mm,
but could just as easily have been obtained by:
- A cut depth of 5mm and a total depth of 15 mm,
- or a total depth of 15 mm and 3 levels.
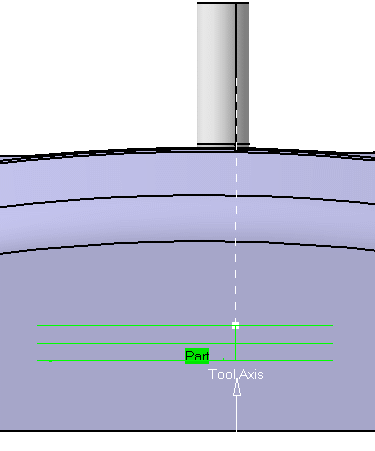
Sweeping: Zone parameters
This tab is hidden when the <<Less button is pressed.
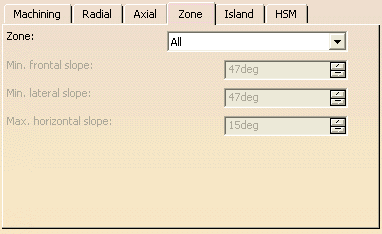
Defines which parts of the part or machining area you wish to machine:
- All: all of the surfaces are
machined,
- Frontal walls:
frontal surfaces of the part are machined,
- Min. frontal slope
Minimum angle between the tool axis and the part surface normal
for the surface to be considered to be a frontal wall.
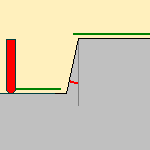
- Lateral walls:
lateral surfaces of the part are machined,
- Min. lateral slope
Minimum angle between the tool axis and the part surface normal
or the surface to be considered to be a lateral wall.
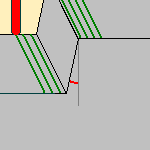
- Horizontal zones: horizontal surfaces of the part are
machined.
- Max. horizontal slope
Maximum angle between the tool axis and the part surface
or the surface to be considered to be a horizontal area.
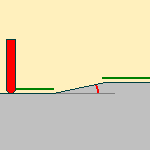
Sweeping: Island parameters
This tab is hidden when the <<Less button is
pressed.
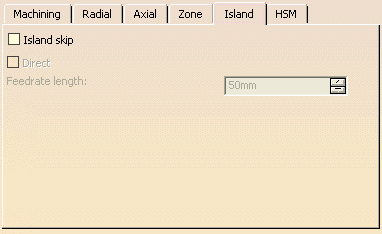
Island skip
Select this check box if you want to use intermediate approaches and
retracts
(i.e. those that link two different areas to machine and that are not at the
beginning nor the end of the tool path).
Direct
- With the Direct check box selected, the tool is not allowed
to rise on intermediate approaches and retracts.
- Whit the Direct check box cleared, the tool will rise to 10
mm on intermediate approaches and retracts.
Feedrate length
Distance beyond which tool path straight lines will be replaced by
intermediate approaches and retracts.
In the picture below, the Feedrate length was set to 45 mm.
Note that the gaps that were less than 45 mm are crossed by a straight line
tool path and
those that are greater than 45 mm are crossed with a standard intermediate
tool path with an approach and a retract.
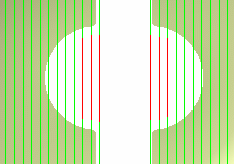
|
|
Sweeping:High Speed Milling tab
All parameters remain displayed in the <<Less mode.
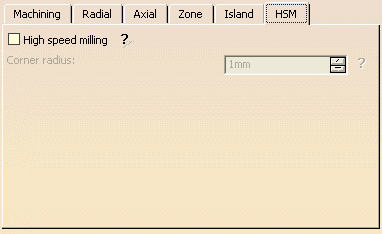
Select the check box High speed milling
to activate and define the parameters for High speed milling. Corner
radius
Defines the radius of the rounded ends of passes.
The ends are rounded to give a smoother path that is machined much faster. Sweeping: Geometry
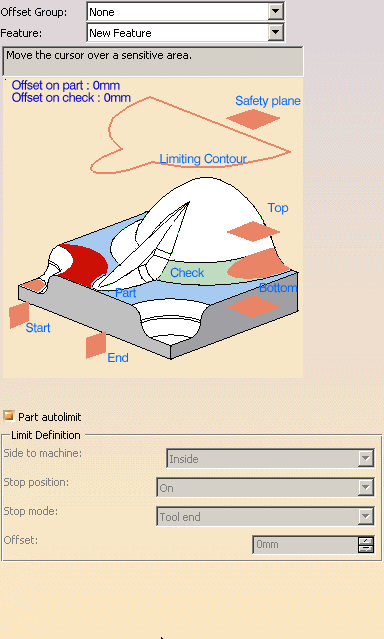
You can specify the following geometry:
- Part with possible Offset on Part (double-click the
label).
- Check elements with possible Offset on Check (double-click
the label).
The check is often a clamp that holds the part and therefore is not an
area to be machined.
 |
The tool path quality is improved along "between paths" if check
surfaces are selected. |
- Area to avoid if you do not wish to machine it (the small
light brown corner near the part selection area).
Subset
If you are editing a rework or a slope area, an additional
information is displayed,
indicating which type of subset you are working on.
This field is not editable (you can not go from one subset to another). Info
When pressed, gives the details on the parameters that were defined with
the rework area. Please refer to the
Basic
Task - Selecting Geometric Components to learn how to select the
geometry.
 Appears when
invalid faces have been detected.
This message disappears when you close the dialog box or when the next
computation is successful.

Appears when invalid faces have been detected and when you have decided
to ignore them.
This message remains displayed as a warning.
Click the text to switch from one status to the other. |