Point to Point Operations
The information in this section will help you
create and edit Point to Point operations in your manufacturing program.
Select Point to Point
then set the strategy parameters
for defining:
- a sequence of elementary Goto Point, Goto Position and Go Delta
tool motions
Specify the tool
to be used,
NC macros
, and
feeds and speeds
as needed.
Point to Point Strategy Parameters
Point to Point Tool Motions
|
Goto Point
A tool motion defined by
the point the tool tip has to reach.
Geometry can be selected as follows:
- Direct selection on the part (points, vertices, and so on)
- Direct indication in a pre-selected surface.
Only selection done within the topological limits of the surface are
taken into account.
- Indication of points to be projected onto a user-defined indication
plane.
This indication plane is considered as infinite (it has no topological
limits). This allows point indication outside the part boundaries.
It is a temporary element used as an aid for selection. It is not
saved after operation edition.
|
|
Goto Position
A tool motion defined
by positioning the tool in contact with a part element, a drive element and
possibly a check element, while taking To / On / Past conditions into
account. |
|
Go Delta
A tool motion defined
by a displacement relative to a previous Point, Position or GoDelta motion
location. Types of Go Delta motion are as follows. |
|
- Components: relative motion defined by DX, DY, DZ
displacements from previous motion location.
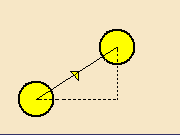
|
|
- Along Y axis: relative motion along Y axis (current axis
system) on a user specified Distance, from previous motion location.
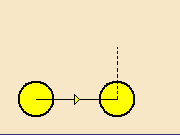
|
|
- Along X axis: relative motion along X axis (current axis
system) on a user specified Distance, from previous motion location.
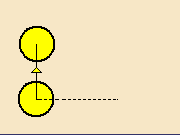
|
|
- Parallel to Line: relative motion on a user specified
Distance, parallel to a user selected Line, from previous motion
location.
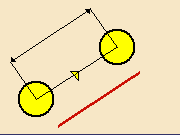
|
|
- Normal to Line: relative motion on a user specified Distance,
normal to a user selected Line, from previous motion location. The tool
motion is done in a plane perpendicular to the tool axis.
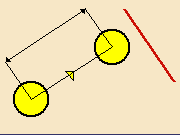
|
|
- Angle to Line: relative motion on a user specified Distance,
along a line computed from user defined Angle and Line. The tool motion
is done in a plane perpendicular to the tool axis.
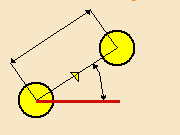
|
Point to Point Machining
Parameters
|
Machining
tolerance
Specifies the
maximum allowed distance between the theoretical and computed tool path.
|
|
Offset along
tool axis
Defines an
offset along the tool axis for all positions of the tool path (it is taken
into account for all the positions of the operation). |
|
First
compensation
Specifies
the tool corrector identifier to be used in the operation.
The corrector type (P1, P2, P3, for example), corrector identifier and
corrector number are defined on the tool. When the NC data source is
generated, the corrector number can be generated using specific parameters.
|
Point to Point
Tool
All Milling and Drilling tools can be used in this type of
operation.
Point to Point
Feeds and Speeds
In the Feeds and Speeds tab page, you can specify
feedrates for approach, retract and machining as well as a machining
spindle speed.
Feedrates and spindle speed can be defined in linear or angular units.
A Spindle output checkbox is available for managing output of the SPINDL
instruction in the generated NC data file. If the checkbox is selected,
the instruction is generated. Otherwise, it is not generated.
Feeds and speeds of the operation can be updated automatically according to
tooling data and the Rough or Finish quality of the
operation. This is described in
Update of Feeds and Speeds on Machining Operation.
In Point to Point operations, a local feedrate can be defined
for all tool motions (except the first motion, which must be either RAPID or a
specific feedrate). The local feedrate is applied instead of the machining
feedrate during the tool motion to reach the tool position. For the operation
start point, machining feedrate is taken into account.
Point to
Point NC Macros
You can define transition paths in your machining operations by means of NC
Macros. These transition paths are built from elementary motions and are useful
for providing approach and retract motion in the tool path.
- An Approach macro is used to approach the operation start point.
- A Retract macro is used to retract from the operation end point.
You can use the following commands to define the elementary motions of
macros in a Point to Point operation:
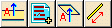 |
|
| |
| |
| |
| |
|
| |
| |
| |
| |
|
| |
| |
| |
-> |
distance along a given direction |
| |
| |
-> |
axial motion to a plane |
| |
-> |
PP word |
-> |
axial motion |
The general procedure is described in
Define Macros on a Milling Operation.