Tooling for Thread Turning
The following tooling may be used:
- Internal and External threading insert-holders with thread inserts.
Geometry for Thread Turning
A Part profile is required. It can be specified as follows:
- select edges either directly or after selecting the By Curve
contextual command. In this case the
Edge Selection toolbar appears to help you specify the guiding
contour.
- select the Sectioning contextual command. Please refer to
Sectioning for details of how to use this capability.
Please note that the sectioning selection method is not associative.
End Limit: None / In / On / Out
This option allows you to specify a point, line, curve or face as the end
element of the profile to be machined. If a face is specified, the end
element is the intersection of the face and the working plane. The position
of the end of machining is also defined with respect to this element.
In / On / Out allows you to specify the Go-Go type positioning of the
tool with respect to the end element. The On option is always used for a
point type end element.
If needed, the profile may be extrapolated to the end element.
End Limit Offset: distance with respect to the end element (only
if end element is a line, curve or face, and when In or Out is set for end
element positioning).
Start Limit: None / In / On / Out
This option allows you to specify a point, line, curve or face as the start
element of the profile to be machined. If a face is specified, the start
element is the intersection of the face and the working plane. The position
of the start of machining is also defined with respect to this element.
In / On / Out allows you to specify the Go-Go type positioning of the tool
with respect to the start element. The On option is always used for a point
type end element.
If needed, the profile may be extrapolated to the start element.
Start Limit offset: distance with respect to the start element
(only if start element is a line, curve or face, and when In or Out
is set for start element positioning).
Relimiting the area to machine by means of limit elements
If you specify a point, it is projected onto the part profile.
A line through the projected point parallel to the radial axis delimits the
area to machine.
If you specify a line, its intersection with the part profile is calculated
(if necessary, the line is extrapolated).
A line through the intersection point parallel to the radial axis delimits
the area to machine.
If you specify a curve, its intersection with the part profile is
calculated (if necessary, the curve is extrapolated using the tangent at
the curve extremity).
A line through the intersection point parallel to the radial axis delimits
the area to machine.
Orientation and
Location for Thread Turning
- Orientation: Internal / External
This option allows you to specify the type of machining according to the
location of the area to machine on the part.
- Location: Front / Back
- Front, the profile is machined toward the head stock
- Back, the profile is machined from the head stock.
Threads
- Thread profile: ISO / Trapezoidal / UNC / Gas / Other
Other allows defining a specific thread profile.
- Thread unit: Pitch / Threads per Inch
You must specify the thread type when the Thread profile is Other. Thread
is automatically set to Pitch for the ISO and Trapezoidal types and set
to Threads per Inch for UNC and Gas.
- Nominal diameter
This value must be given when Thread type is internal and Thread profile
is Other.
- Thread length
This value must be given when the Start or End relimiting element is set
to Profile End.
- Thread pitch
This value must be given when the Thread type is set to Pitch or the
Thread profile is ISO or Trapezoidal.
- Threads/inch
This value must be given when the Thread type is set to Thread per inch
or when the Thread profile is UNC or Gas.
- Thread depth
This value must be given when the Thread profile is Other.
- Number of threads
When greater than 1, this value allows you to specify whether a
multi-start thread is to be machined.
Machining Strategy Parameters for Thread
Turning
Machining Options for
Thread Turning
- Threading type. You must choose the desired threading type:
- Constant depth of cut
- Constant section of cut
- Maximum Depth of cut when Threading type is set to Constant
depth of cut
- Number of passes when Threading type is set to Constant
section of cut.
When the number of passes is defined, the Section of cut value is
automatically set.
- Machining spindle speed in revolutions per minute
- Thread Penetration type:
- Straight
- Oblique (penetration angle must be specified)
- Alternate (penetration angle must be specified).
Path Computation
options for Thread Turning
- Clearance on crest diameter
- Lead-in Distance
Defined with respect to the cutting direction. The tool is in RAPID
mode before this distance.
- Lift-off Distance and Lift-off Angle.
These parameters define the lift-off vector at the end of each pass with
respect to the cutting direction. The figure below shows the effect of a
positive lift-off angle (external machining is assumed).
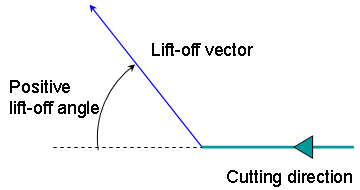
First and Last Passes options for Thread
Turning
- Manage penetration on first passes by means of the First passes
check box. This option is available when Threading type is set to
Constant section of cut. When activated, you must specify values for:
- Number of first passes
- First section rate.
When these two values are specified, the
Section of cut for first passes value is automatically set.
- Manage penetration on the last passes by means of the Last passes
check box. When activated, you must specify:
- Number of last passes
- Depth of cut for last passes.
- Manage the spring passes by means of the Spring passes check
box. When activated, you must specify a
Number of spring passes.
CYCLE or GOTO Output Syntaxes
If you want to generate CYCLE statements, you must select the
Output CYCLE syntax checkbox in the Options tab and set the
Syntax Used option to Yes in the NC Output generation dialog box.
Otherwise, GOTO statements will be generated.
The parameters available for PP word syntaxes for this type of operation
are described in the
NC_LATHE_THREADING section of the Manufacturing Infrastructure User's Guide.
Editing CYCLE Syntaxes
The Edit
Cycle command in the Thread Turning dialog box allows you to:
- display the unresolved syntax of the NC Instruction of the operation.
This is the syntax as specified in the PP table referenced by the current
Part Operation.
- display and, if needed, edit the syntax that is resolved either by
geometric selection and user entries.
The Cycle Syntax Edition dialog box is displayed when you click the
Edit Cycle command.
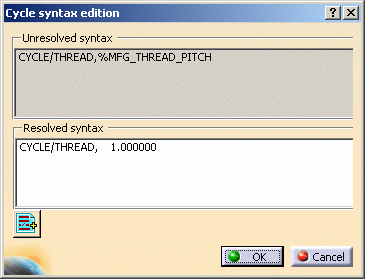
You can access all the CYCLE syntaxes contained in the current PP table
by means of the PP instruction
icon. You can then select the desired syntax to be used by means of the
procedure described in the
Insert PP Instruction section.
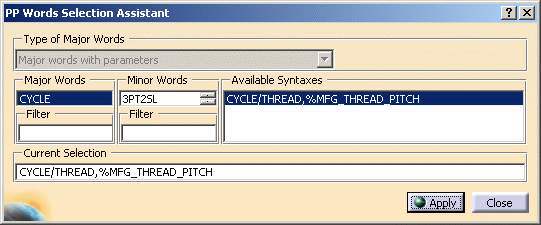
Tool Compensation for Thread Turning
You can select
a tool compensation number corresponding to the desired tool output
point. Note that the usable compensation numbers are defined on the tool
assembly linked to the machining operation. If
you do not select a tool compensation number, the output point
corresponding to type P9 will be used by default.
Note that the change of output point is
managed automatically if you set the
Change
Output Point option for Trapezoidal or Other Thread profile.
Approach and Retract Macros for Thread Turning
The following
Approach and Retract macros are proposed:
Direct, Axial-radial, Radial-axial, and Build by user.
The selected macro type (Approach or Retract)
defines the tool motion before or after machining. Various feedrates are
available for the approach and retract motions (RAPID, air-cutting, and so
on).
See
Define Macros on a Turning Operation for more information. |