 |
-
Click Thread Representation Creation
in the
Geometry for 3D
Annotations toolbar.
The Thread Representation Creation dialog box is displayed. |
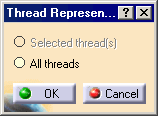 |
-
Select Thread.1 in the specification tree. You
can also select the threaded face in the geometry window.
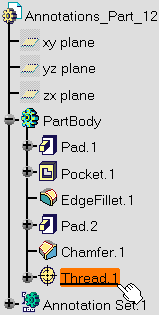 |
The Thread Representation Creation dialog box is updated
to indicate that the thread representation will be created for the
selected thread. |
 |
 |
In the case of numerous threads, selecting the
All threads option lets you create the thread representations of
all of them. |
|
-
Click OK to validate and exit the dialog box.
The geometrical representation of the thread is displayed in the geometry,
and an item is created in the specification tree. |
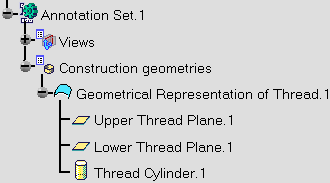 |
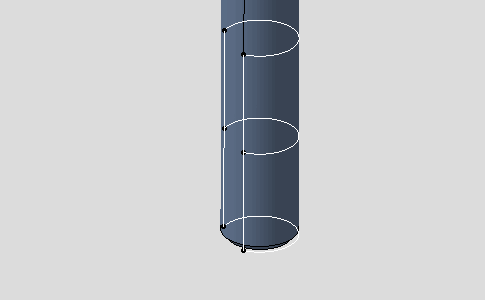 |
-
Click Tolerancing Advisor
in the
Annotations
toolbar.
The Semantic Tolerancing Advisor dialog box is displayed. |
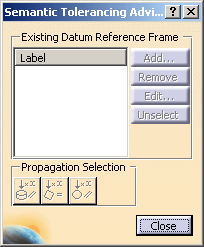 |
-
Select the median 3/4 circle arc which symbolizes the
thread helical surface.
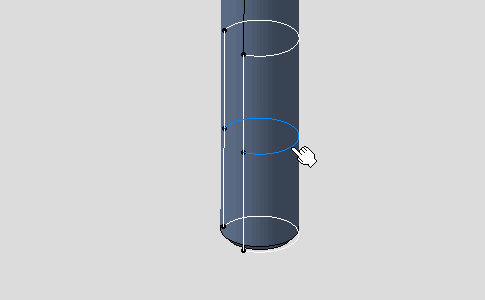 |
The Semantic Tolerancing Advisor dialog box is updated
according to the selected element. |
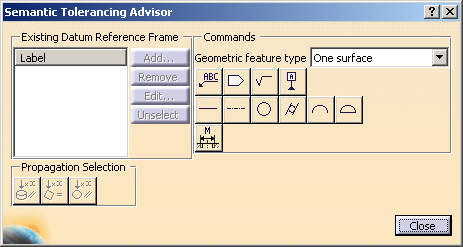 |
-
Click Thread Diameter (One surface):
The thread diameter dimension is previewed and the
Limit of Size Definition dialog box is displayed, offering
the following options:
|
-
Select the Tol class
option and in the Tol class drop-down list, select 6g
as the tolerance class value.
The pitch value is defined according to the selected standard when you
created the thread. |
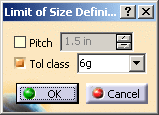 |
-
Click OK then anywhere in the geometry window
to unselect.
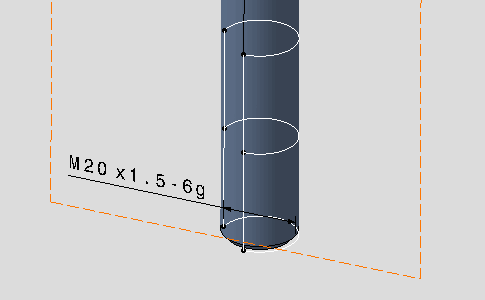 |
The thread diameter dimension is created.
The M symbol is displayed instead of the diameter symbol
according to the selected standard when you created the thread.
If no standard has been defined the diameter symbol is displayed. |
-
Back in the Semantic Tolerancing Advisor dialog
box, multi-select (using the Ctrl key, for example) the 3/4
circle arcs which symbolize the thread starting and ending planes.
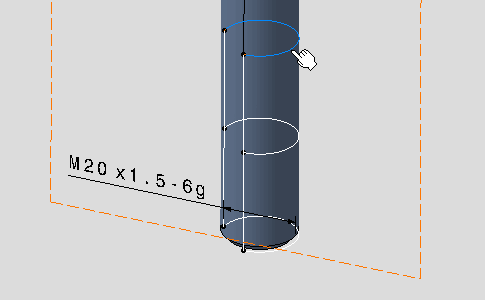 |
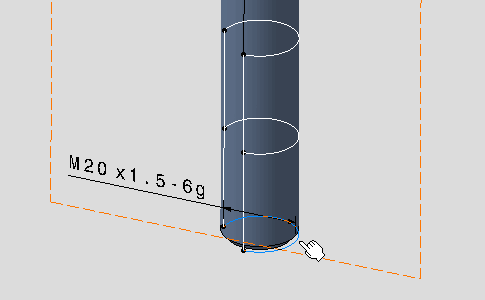 |
 |
Note that the 3/4 circle arcs which symbolize
the thread starting and ending planes are recognized as planar surfaces,
which means that you can tolerance them just like any other planar surface. |
|
-
Once again, the Semantic Tolerancing Advisor
dialog box is updated according to the selected elements.
-
Click Distance Creation (Tab/slot):
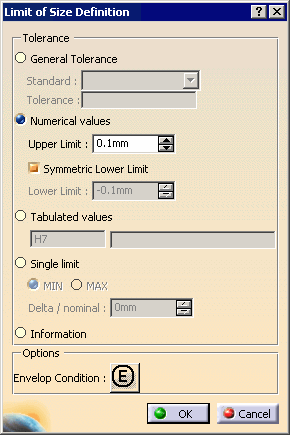 |
The thread length dimension is previewed and the Limit of
Size Definition dialog box is displayed, offering the following
options:
- General Tolerance: lets you define a pre-defined
class of tolerance, see
Tolerances for the default class setting.
- Numerical values: lets you define the Upper Limit and
optionally the Lower Limit (provided you uncheck the Symmetric Lower
Limit option).
- Tabulated values: lets you define fitting tolerances.
Refer to Normative References for more
information: ISO 286, ANSI B4.2.
- Single limit: lets you enter a minimum or maximum
tolerance value. Use the Delta / nominal field to enter a value in
relation to the nominal diameter value. For example, if the nominal
diameter value is 10 and if you enter 1, then the tolerance value
will be 11.
-
Information/Reference: lets you to set the
dimension as information (ISO-based standards)/ reference
(ASME-based standards). The information/reference dimension is
displayed enclosed by parentheses in geometry window.
|
-
Select the Tabulated values option.
-
Click OK then anywhere in the geometry window
to unselect.
-
Click Close in the Semantic Tolerancing
Advisor dialog box.
The thread dimensions and tolerances are displayed in the geometry as well
as in the specification tree. |
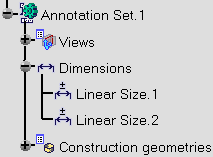 |
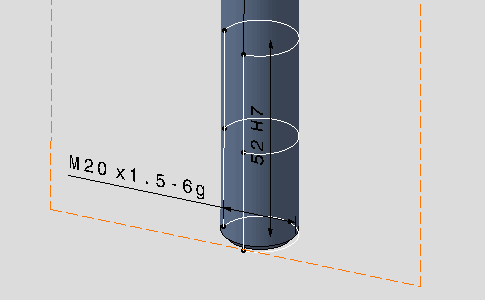 |
|