 |
-
Click Line
in the Geometry Creation toolbar.
-
Use the vertical axis to define the cutting profile as
shown below, and double-click to end the line creation.
 |
You could also draw a profile consisting in multiple segments to
create an aligned section view/cut or an offset section view/cut.
|
-
Click New Section/Auxiliary View
in the Layout toolbar (Views sub-toolbar).
-
Select the line you have just created as the cutting
profile.
 |
You cannot select geometry which does not belong to the active
view. |
The Tools Palette toolbar is automatically displayed with the following options:
-
Auxiliary View: creates an auxiliary view.
-
Section View: creates a section view.
-
Section Cut: creates a section cut.
Create Datum: activate this option to create
a non-associative view. By default this option is not activated.
 |
This option is available only when selecting the New View From command. |
 |
These options are also available from the contextual menu.
Furthermore, the contextual menu display the Invert Normal option, that is also available directly in the view, via green manipulators. |
-
Select the Section View icon
.
-
Click on the sheet at the location where you want the
section view to be positioned.
 |
- Positioning the view defines the section view direction, in
accordance with the projection method.
The projection method (First angle standard or Third angle
standard) is defined by the sheet style, as specified in the
standard used by the layout. For more information, refer to
Sheet Styles in the Administration Tasks chapter. You can
change the projection method by editing the layout sheet properties
(using Edit > Properties).
- Section/auxiliary views are always created using the sheet
scale. The primary view scale, when it is different from the sheet
scale, is not propagated to other section/auxiliary views.
- If you change the sheet scale (defined in the sheet
properties), the scale of all existing views (defined in the view
properties) is multiplied by that of the sheet (for example, if
existing views already have a scale of 1/10, and if you change the
sheet scale to 1/10, then existing views will now have a scale of
1/100).
|
 |
Note how the view is previewed in the part window.
You need to zoom out, as the view box defined in the ISO_3D standard
used by the current layout has sides of 1000mm. For more information
on the standards, see Administration Tasks.
|
An empty section view is created, with its plane
perpendicular to the active view. Additionally, the Section view item is
added to the specification tree.
-
Double-click the section view to activate it. You can now
create 2D geometry in this view.
|
 |
About Section/Auxiliary Views
-
Section views, section cuts or auxiliary views are
created using an existing 2D profile (a single line or a multi-segment
profile) in the active view. Such views are based on a plane
perpendicular to the active view which contains the directional element
(the selected line). The projection direction depends on two factors:
-
the cursor location
-
the projection method
Once created, the new view is not associative to
the directional element, and this element is not transformed into a
callout. Therefore, it is impossible to edit section profiles after the
view has been created.
- Section views, section cuts or auxiliary views are positioned
according to their reference view. Therefore, moving a reference view
also moves its linked views.
The case of multi-segment profiles
Selecting a profile made of multiple segments lets you create several
section views/cuts in one shot. There are two possible scenarios:
- Aligned profile:
When selecting such a profile, a view is created for each segment.
- Offset profile:
When selecting such a profile, a view is created for each segment
parallel to the first one (for example, 1; 3; 5).
When creating views from a multi-segment profile, remember the following
points:
- Make sure you select the first segment in the profile (the
first-created one) if you want to create section views/cuts. If you do
not select the first segment, then only the selected segment is taken
into account (and not the whole profile), and an auxiliary is created.
- The views share the same origin in the layout sheet, and their local
axes (H and V) overlap.
- The first view of a multi-segment profile has folding lines
corresponding to each segment, and the other views only have folding
lines corresponding to the current segment.
- The name of each view is suffixed to indicate the view's rank.
- Only section views and section cuts can be created from a
multi-segment profile.
- The first segment of a multi-segment profile defines the section
orientation.
Section/auxiliary view origin point
The section/auxiliary view origin point is a 3D projection of the active view origin point to the geometry used as a cutting
profile.
See the illustration below:
The Front view origin point (represented in red) is a projection of the 3D axis origin (in blue).
For more information, you can refer to Before you begin creating views and
layout views customization.
Front View |
3D View |
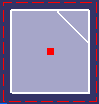 |
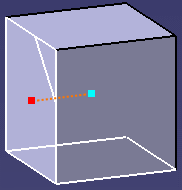 |
- The slanting line is used as a cutting profile
to create a Section view.
The Front view origin point is projected to the cutting profile to create the Section view origin point (in green).
Front View | Section View |
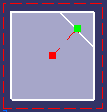 |
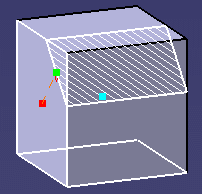 | You can see that the section view origin point (in green) is not a
projection of the 3D axis origin (in blue), but a projection of the active view origin point (red).
Section/auxiliary view axis orientation
The section/auxiliary view axis orientation is based on the cutting profile
angle defined in the primary view. In this way, the section/auxiliary view axis
follows the projected element plane, in order to simplify the design work.
See illustrations below:
Front view axis orientation |
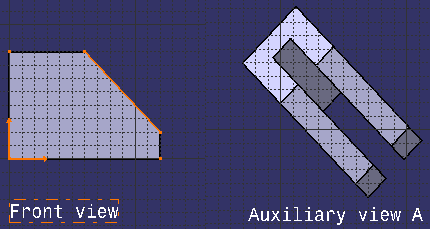 |
Auxiliary view axis orientation (angle = 45deg) |
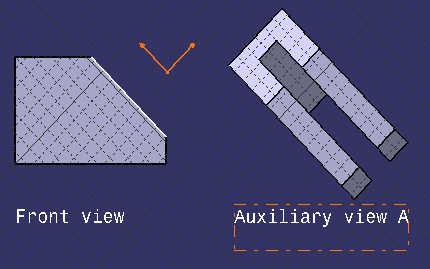 |
More precisely, here are the rules used to position the H /
V / N axis orientation in an auxiliary/section view:
H = has the same axis and the inverse direction of the active view
N axis. (As the reference view
N axis is
always going out of the geometry, so the auxiliary/section view H axis is going inside the geometry).
V = has the same axis as the cutting profile. Its direction depends on N and H: these three
directions must form a direct trihedron (right-handed cartesian system).
N = the axis is the chosen point of view (the user's look), the direction is toward the user.
As N is fixed and H is known,
V is deduced.
See illustrations below:
Active view
axis orientation |
Section/Auxiliary view
axis orientation |
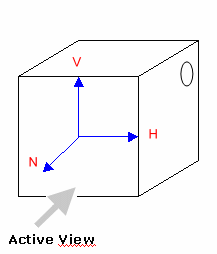 |
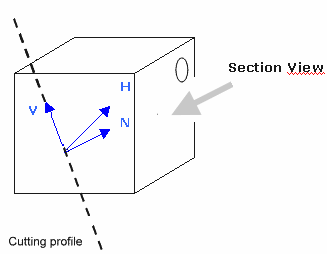 |
|