 |
The Automotive BiW Fastening Application
natively supports the most common BiW joining process
categories: Welding, Adhesive, Sealant, and BiW Mechanical. An additional "Unspecified" Process Category is supplied in order to classify specific
technologies that do not belong to the application natively supported
process categories.
For each general process category, specific fastening process codes along
with their matching relevant parameters can be set-up in the Application
Parameters Start-Up standard file named GBF_STD. |
|
|
|
Here are the steps to customize the standard
file:
|
|
Locating the BiW Fastening Application
Standard File
|
|
The "GBF_STD" Standard file is located according to the reffiles/GbfStandards path from CATIA run time view root
directory (intel_a for Windows, aix_a for IBM UNIX, irix_a for SGI UNIX,
solaris_a for SUN Unix, hpux_a for HP UNIX). Two extensions are provided
for this file:
- .xls for Windows Operating System run time usage
- .txt for UNIX operating system run time usage
|
|
For example, you will
find in the directory: MyCompanyRootRuntimeview/intel_a/reffiles/GbfStandards,
the following files:
- GBF_STD.txt which is the master file
and can be generated from the GBF_STD.xls file on Windows using the Save
as *.txt command in Excel
- GBF_STD.xls which can be edited with
the Excel Windows Editor
|
|
|
|
|
Customizing the GBF_STD.xls file
|
|
|
|
The GBF_STD.xls standard file can be
customized by the company data administrator, according to his company or
industry specific standards requirements.
This file features two columns:
- the first column identifies the parameter name
- the second column specifies the list of possible values of the
identified parameter : value1, <value2>, value3. (brackets <>,
specify the default value: i.e. value2 is the default value of the
previous list)
|
|
Rows are divided into six chapters delimited
by excel row cells and filled in different colors.
- The first chapter (light green fill-in) specifies the list of CATIA
application parameters supported whatever the fastener process category
can be. This chapter is itself subdivided into three sections:
- A: CATIA V5 BiW Fastening Application parameters
- Number of digits for fixed-length
- B: CATIA V5 BiW Joint and Joint Body Parameters
- C: CATIA V5 BiW Fastener parameters
- 1. Life Cycle parameters
- 2. Fastener type parameters
- 3. Fastener Parameters
- The five additional chapters enable to set-up the list of the
fasteners parameters respectively for each specific process type and for
each supported process category:
- Welding (yellow fill-in)
- Adhesive (cyan fill-in)
- Sealant (magenta fill-in)
- BiW Mechanical (green fill-in)
- Unspecified (brown fill-in)
These chapters are themselves subdivided into sections C-1, C-2, C-3. |
|
What can be modified?
|
|
|
|
Pre-defined values of each BiW Fastening general parameter identified
in the sections C-2, C-3 of chapter 1
|
|
Modifying the list of values (column 2) for each row
parameter of Chapter 1, you can customize:
-
the applicable process categories (PCATS
parameter) value list: WLD (Welding), ADH (Adhesive), SEA
(Sealant), BWM (BiW Mechanical), U (Unspecified Process Category).
For example, you can narrow this list to: WLD, BWM if you plan to
use only Welding and BiW mechanical fastening technologies.
|
|
|
|
 |
Note that if you do not set up the
Fastener Types in the standard file, then the corresponding Fastener
commands will be appear grayish meaning that they cannot be
activated. |
|
|
- the assigned color for each process category (WLD_Color parameter,
ADH_Color parameter, transparent, etc.).
|
|
- the assigned symbol to thickness count if necessary:
- By default, the code 111 is assigned to 1T Thickness Count ->

- By default, the code 151 is assigned to 2T Thickness Count ->

- By default, the code 113 is assigned to 3T Thickness Count ->

- By default, the code 114 is assigned to 4T Thickness Count ->

Refer to the Symbols table for the
available list of symbols. |
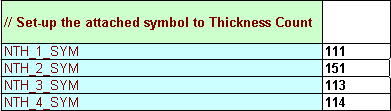 |
|
|
|
|
- the list of possible process types values for each process category
(PCAName_PTYPS parameter). For instance:
- the list of Welding process types (WLD_PTYPS parameter):
<21>;14;141;52;UNSW
- the list of possible values of each CATIA BiW Fastener attribute:
- robustness ( ROB parameter): A,B,C,D,U
- regulation (REG parameter): A,B,C,D,U
- finish (FIN parameter): A,B,C,D,U
- material (MAT parameter): MAT1, MAT2, etc.
For each fastener attribute, you can choose your own set of code values
(except for the discretization).
For example, you can choose to customize:
- the list of values of the robustness attributes to: A,B,C,D,E,U
- the list of values of the regulation attributes to : A,B
|
|
- the specific "relevant" value for each classification parameters:
Robustness, Finish, Regulation, etc. and assign to this value a
Symbol Mark Code:
- Example1: Assign Mark code "1" to Robustness parameter value C.
ROB_C_SYMO |
1 |
 |
- Example2: Assign Mark code "1" to Finish parameter value A.
FIN_A_SYMO |
1 |
 |
|
|
Each attribute value (A, B, etc) is the coded
value of the attribute as it will be stored in the Data Model. You can
provide a end user translation for each parameter coded value in the CATIA
NLS resource file CATBfmAttributesNLS.txt . In this file, each parameter
coded value is identified by a key built by concatenating the name of the
parameter and the coded value, separated by the "_" string separator. The
translation of the parameter is provided by setting the parameter value key
to its translation text.
For example the line: ROB_A = "Critical" provides the end-user with the
"Critical" translation of the coded value A of the Robustness parameter
(ROB).
The CATBfmAttributesNLS.txt file is located in your runtime environment
in MyCompanyRootRunTimeView/intel_a/resources/msgcatalog. |
|
 |
You must not remove any parameter
belonging to the Chapter 1 rows. |
|
|
The list of pre-defined fastener process type parameters belonging to
chapters 2 to 6
|
|
You can modify this list, either by: |
|
- modifying the list of values for each row containing the pre-defined
specific fastener process type parameters, or
- removing the pre-defined specific fastener process type parameters
you are not interested in, or
- adding your company specific fastener process type parameters
consistently with the list of process type values set up in Chapter 1
|
|
|
|
Let's take an example for a spotpoint of
Process Category = Welding and Process Type = Resistance. You can set:
-
the list of specific process
types code values (SpotPoint_WLD_PTY parameter): <21>;14;141;52;UNSW
In this list, the code value <21> matches the ISO code for Resistance
Welding.
-
the list of the applicable
standard attributes (SpotPoint_21_APAT parameter): you can specify the
list of attributes you consider as relevant for this process type. The
attributes strings must be chosen among the CATIA list:
ROB;REG;FIN;GFL;IFL;MID.
For a curve fastener, its discretization parameter
(DIS) is an added applicable attribute.
-
the applicability or the non
applicability of an add-on material (SpotPoint_21_AMAT parameter).
-
the list of possible Shape
Definition values (ASDF) of each parameter. The attribute strings must be
chosen among the values: PT3 (3DPoint);HSP (Hemisphere);SH
(Shank);SHH(Shank with Head);SHF(Shank with Head and Foot).
-
the list of possible string
code values of each parameter (SpotPoint_21_ROB, SpotPoint_21_REG, etc).
For a curve fastener, its discretization parameter (CurveBead_PTY_DIS
values) must be chosen among the SAG and STEP values.
-
the assignment of a graphic
symbol (SpotPoint_21_SYM parameter)
Refer to the Symbols table for the available
list of symbols.
|
|
Customizing the BIW
Functional Annotations
|
|
All fields can be customized, except for the F5 Field.
For each field (F1, F2, F3 and
F4), the allowed types of parameters that can be displayed are ABF
natively defined and cannot be extended: |
 |
- Field 1: (depending on the annotation type)
- Fastener Annotations: Fastener ID parameters
- Single ID (JEID)
- ID and Process Type (JEID-PTY)
- Diameter (DIA)
- User Value (USR)
- Series Annotations
- [Number of Fasteners] contained in Joint Body ((JB)FN)
- Joint Body ID -
[Number of Fasteners] (JBID-FN)
- Joint Body ID -
Process Type (JBID-PTY)
- [Number of Fasteners] contained in Joint ((J)FN)
- Joint ID -
[Number of Fasteners] (JID-FN)
- Joint ID -
Process Type (JID-PTY)
- Diameter
- User Value (USR)
- Field 2: Engineering Class Parameters
- Robustness or Finish or Regulation (ROB, REG, or FIN)
- User Value (USR)
- Field 3: Manufacturing Class Parameters
- Geometry Flag or Manufacturing Code or Inspection Flag (GFL,
MID or IFL)
- User Value (USR)
- Field 4: Shape Parameters
- Diameter or Length or Height or Material (DIA, LENGTH, HEIGHT
or MAT)
- User Value (USR)
|
Therefore an administrator can remove one or more parameters from the
list for each field but cannot add new parameters.
For instance, if an administrator adds the ROB value in the
parameters list of the F1 Field, it will not be displayed through the
F1 Field. |
 |
|
Saving the GBF_STD.xls file and keeping its name
|
|
- On Windows, the data administrator:
- edits and modifies the GBF_STD excel file,
- saves this file as .xls by keeping its original name (GBF_STD.xls)
- saves this file as tab delimiter by keeping its original name (GBF_STD.txt)
This standard text file will be used by default at import time.
|
|
- On Unix, the data administrator:
- edits and modifies the GBF_STD text file,
- saves this file as .txt.
|
|
|
|
Here is an
example of how to add a new process type named
"MyWldType" for a Welding SpotPoint. |
 |
Additional customized sample GBF_STD file
|
|
|
 |