 |
This task explains two ways to create bends
between walls in the Sheet Metal part.
These bends can be created on non-connex walls, and with a constant radius
value. |
 |
Open the
NEWBendExtremities01.CATPart document. |
 |
-
Click Bend
.
The Bend Definition dialog box is displayed.
-
Select Support 1 and Support 2 in
the specification tree or in the geometry area. The two supports must be
connected by the edge of their internal faces.
The Bend Definition dialog box is updated, and arrows are
displayed, indicating the walls orientation. When relevant (which is
not the case in our example), you can click the arrows to invert the
orientation. |
The left and right endpoints for the bend are identified using
text. |
-
Right-click the Radius field and select
Formula -> Deactivate from the contextual menu to change the value.
|
You can set the Radius value to 0. |
-
Enter 4mm for the radius and click Preview.
The bend is previewed, along with its orientation symbolized by arrows.
-
Click the More>> button to display additional
options:
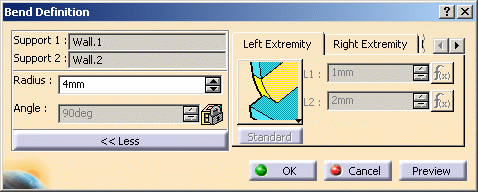 |
|
You can define:
|
|
-
Click the Left Extremity tab, and choose the
Mini with round relief bend extremity type.
-
Then, deactivate the L1 and L2 length formulas (as
previously explained in step 3), and set them to 6mm and 3mm
respectively.
-
Click the Right Extremity tab, and choose the
Curved shape type.
-
Click Preview to visualize the left and right
extremities.
-
Click OK in the Bend Definition dialog box.
The bend (identified as Cylindrical Bend) is created
with the specified extremity types and is added to the specification
tree. |
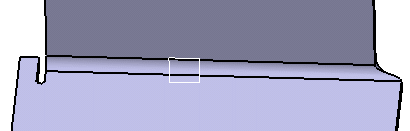 |
 |
- The extremities and the corner relief defined with the current
dialog box will apply locally and prevail over any other global
definition.
- Be careful when creating bends with square or
round relief. Depending on the geometry configuration, this
can lead to removing more matter than you would expect. Indeed, a
corner relief being computed on the whole intersection of the
elements involved (bends or bend/wall), in the following
configuration, the matter is removed till the end of the wall.
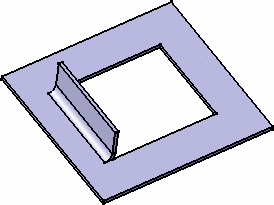 |
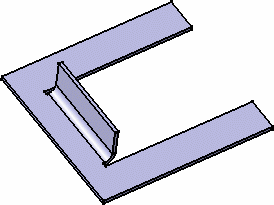 |
Bend with no relief |
Bend with square relief |
|
|
In this case, it is best to replace the bend corner relieves with
cutouts (identified in red in the
figure below) that will act as corner relieves removing matter to the
part.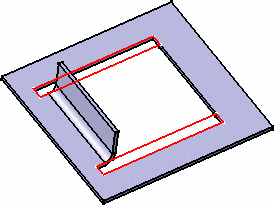 |
|
You can create bends with closed extremities on walls.
|
|
If you want to create a close bend, be aware that:
- a closed bend cannot be built with a null radius. If you try
to, a warning is issued and the bend creation fails;
- a closed bend cannot be built if there is no intersection with
another bend, for instance if a bend is created on an inverted
wall. A warning is issued and a maximum extremity is built instead;
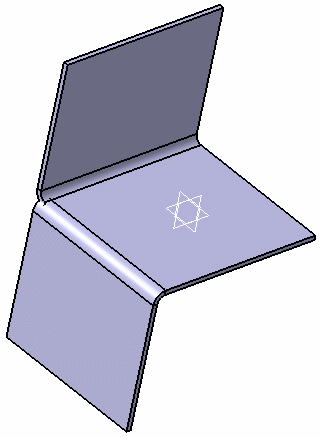
|
|
- the bends' supporting walls are not trimmed.
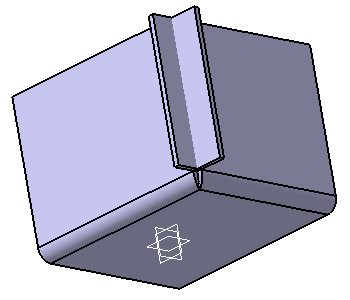
|
|
- In case the intersection between the bends of the supporting
walls is too short, a tangency extrapolation is computed.
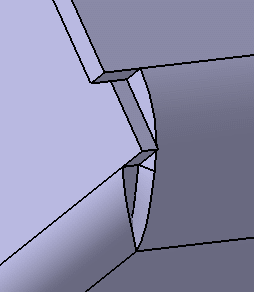
|
|
|
|
|
Creating a Bend on a Flange or a Stamp
Let's take an example with a surface stamp. |
 |
Open the
NEWBendExtremities02.CATPart document. |
 |
-
Click Bend
.
The Bend Definition dialog box is displayed.
-
Select the surface stamp's face as Support 1.
-
Select Wall.3 in the specification tree as Support 2.
-
Click OK in the Bend Definition dialog box to
create the bend on the surface stamp.
|
 |
To deselect a wall, simply click on another wall available in the
part. |
 |
- The stamp must be open, contain a planar face, and have a
radius higher than 0.
|
|
- You can intersect a closed bend with a flange.
|
|
|
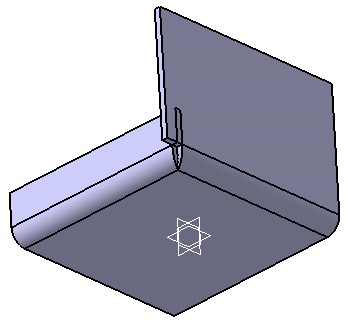 |
|
You will note that, unlike bends on walls, the filleted
part of the flange is relimited by the supporting wall. |
 |