 |
-
Click Surfaces
Network
.
The dialog box is displayed.
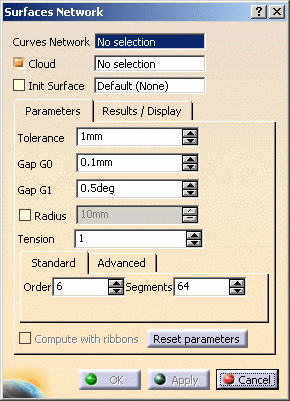
-
Select the curves network you have created (mandatory),
as well as the mesh as the Cloud.
-
Select Init Surface check box if you want to
use one.
The init surface helps the computation by giving the shape of the result
surface.
You can either select it yourself or let the application compute it in the
direction of the largest curve.
If you select an init surface, its name is displayed in the field
Init Surface.
 |
- It is not necessary to use a support
Cloud or a
Init Surface,
but they may improve the output.
- The init surface must be larger than the domain to process.
|
-
The curves network is displayed, with a green V marker on
each wire, meaning the wire will be filled.
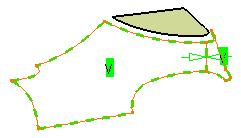
-
You can fill all the wires automatically (this is the
proposed default) or you can fill the wires one by one.
-
If you do not want to fill a wire:
- either click its marker, it will turn into a red X marker. The
wire will not be filled.
(Click marker again to reselect the wire, if necessary),
- or place the cursor on a marker and use the contextual menu:
|
|
-
Constraints
are set on edges shared by two wires.
 |
represents a point continuity |
 |
represents a tangency continuity |
To change the type of a constraint:
-
either click its marker. This will act as a
toggle,
-
or place the cursor on a marker and use the
contextual menu:
|
|
-
You can set the
Tolerance, which
is the mean maximum deviation between the surface created
and the cloud of points or mesh, i.e. the deviation may be higher at some
places. This field is editable.
-
You can set Gap:
G0, which is the distance between the surface and the boundary
curves.
Since there is more noise on points than on curves, the Tolerance
may be higher than the GO Gap.
The default value is 1.
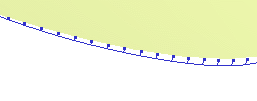
-
You can set Gap: G1, which is the tangency
tolerance between two contiguous surfaces (in blue below).
The default value is 0.5.
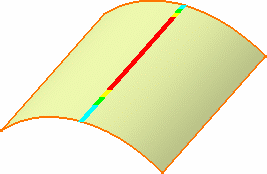
-
You can set the
Radius:
-
You can set the
Tension:
Possible values are between 0 and 4.
Use a higher value to have a tenser surface. |
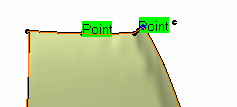 |
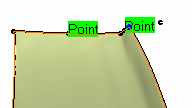 |
-
You can set
Standard: Order,
Segments:
These parameters apply globally to the surface computed. They are maximum
values.
The actual values are computed automatically by the action.
Surfaces Network creates a NURBS surface, controlled by
the tolerance (i.e. Tolerance),
the number of segments and their order.
Whenever possible, this surface consists of one single segment,
otherwise, it is made of several segments.
This surface may then be trimmed by the curves.
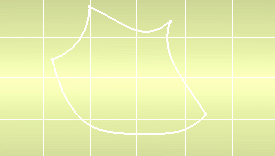 |
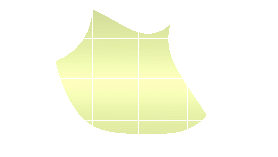 |
You can increase the order of the segments, thus reducing their
number, or vice-versa. |
- If the number of segments is x, this means that the surface
computed will consist of
a maximum of x segments, or less.
The default number of segments is 64, the maximum number is 2048.
|
- If the order of segments is y, this means that each segment will
have a maximum number
of y control points in each direction, or less.
The segment order may vary from 3 to 15.
|
-
You can set
Advanced: Order and Segments in U
and V. You may want to impose an order
and a number of segments in both U and V direction. To do so, go to the
Advanced tab.
You can edit the fields to:
- type the number of segments in each direction,
- type the order of segments in each direction.
Click Apply to restart the computation.
 |
- Increasing the order of the segments may result in an
oscillating surface,
even if this is not visible.
- Typeing a global number of Segments in the
Standard tab is different
from typeing the square roots of the global value for the
Segments in U and in V
in the Advanced tab:
if you type a global value of 64 segments in the Standard
tab, this is a maximum value,
that may be distributed in 14 segments in U and 4 in V,
whereas if you type 8 segments in U and 8 segments in V,
the maximum number of segments in U will be 8, the surfaces
computed will thus be different.
|
-
You can select the
Compute with ribbons
check box
This check box is only available if a mesh is selected and
is used when a tangent continuity is
required between the wires.
The wires curves are projected on the mesh and a tangency
ribbon is computed on the mesh
around the curve projection, and then taken into account for the
computation of the filling surface.
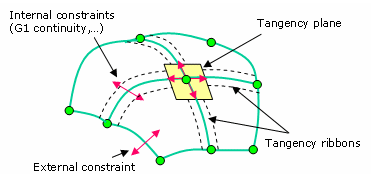
-
Click
Reset parameters to reset the parameters, if necessary.
-
Click Apply button. The filling surface is
computed. A progress bar is displayed.
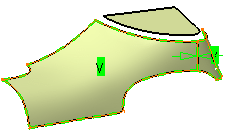
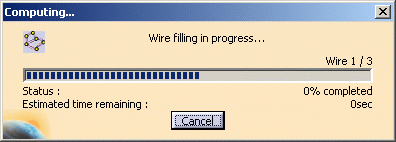
-
Go to the
Results/Display
tab.
Information on the points for the parameters taken into
account by the computation are available
in the box at the top of the tab (no dynamic display):
-
the maximum deviation found between the points of the
cloud and the surface,
-
the mean deviation found between the points of the cloud
and the surface.
This deviation should be as small as possible.
-
the percentage of points of the cloud that are below the
mean deviation.
-
Select the
Spikes check box to display the deviations.
-
Select the
Segmentation check
box to display
-
the segmentation on the surfaces computed,
-
the number of segments and order in U,
-
the number of segments and order in V.
|
-
Use the
Deviation field
to type the value
above which the deviation spikes will be displayed.
When you first enter the action, the Deviation value is the
same as the Tolerance.
Once a surface has been computed, the Deviation value is the
computed one.
-
By default, the check boxes
Display selection
and Display
constraints are selected.
You can unselect them according to your needs.
-
Once you are satisfied, click OK to create the
result:
the surfaces are assembled (Tolerance = 0.1 mm)
-
If the assembly does not respect the tolerance an error
message is issued.
-
If the assembly failed, an error message is issued and
the surfaces are created separately.
|
A Surface.xx element is created in the
specification tree.
|