-
Open the
MoldProduct.CATProduct from the samples/Rule/MoldBase directory. In
the specification tree, you see the Mold (Mold.1) and the
MoldedPart (MoldedPart). In MoldedPart, under
Publications you find the
published CoreSurface, i.e. the parting surface between
core and cavity. If you expand CorePlate, you will see
ExternalReferences that enables the synchronization with the molded
part.
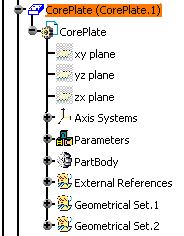
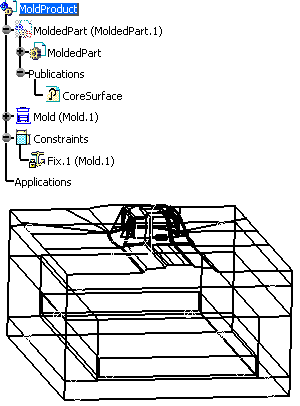
-
We are going to insert an ejector and
activate a rule that will manage the guiding height of the ejector in
respect of its position and of the CoreSurface shape.
Click the Add Ejector icon
. Click the File Open
icon in the dialog box. In the File Open box, browse the
samples directories and select Ejector_A_1.CATPart in the
samples/Rule/Component directory.
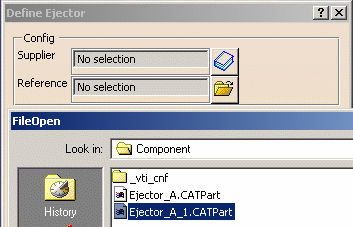
-
Select the top face of EjectorPlateB.
-
The sketcher is displayed, with a manipulator
to position the ejector:
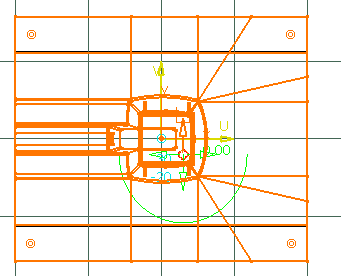
-
The Drill from field is updated with
EjectorPlateB. Still in the sketcher, select CorePlate as
To.
-
Go to the Parameters tab. Click
the rule catalog icon and select the MTDRule.catalog in the
samples/Rule/Component directory.
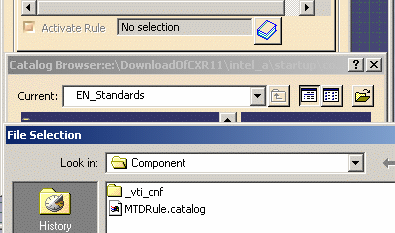
-
In the following dialog boxes, double-click
OffsetParting then RuleForOffsetParting. Click OK.
-
Make sure the Activate Rule check
box is selected. Click OK. The ejector is created. Whatever its
location, the height of of the guiding hole has always the same value,
defined by the parameter named Offset_Parting.
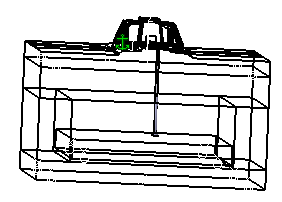
-
Select Edit Ejector component in
the contextual menu of Ejector_A_1_1.1
-
Change the position of the ejector and click OK. Update your model if necessary. You see that the height of
the guiding hole is split according to its position and the
CoreSurface shape, and has always the same value.
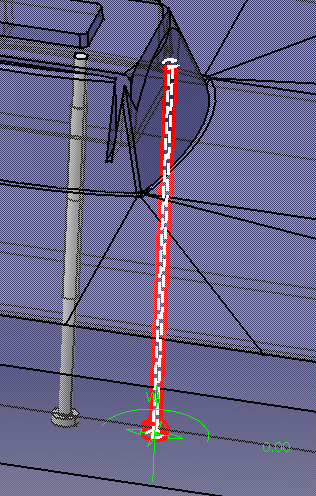
You see the preview of the new
split
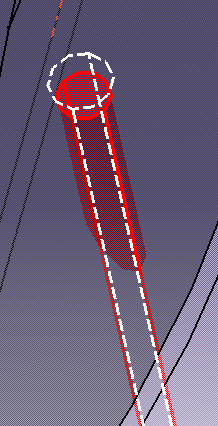
Result
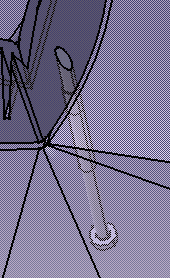