-
Click Flange
in the Swept Walls sub-toolbar.
The Flange Definition dialog box is displayed.
Note that the image in the right-hand pane of the dialog
box is updated as you choose your parameters and options, and provides a
graphical explanation about the current selection.
|
|
 |
By default, the icon which is pre-selected next to the Angle
field corresponds to an acute angle
for the Generative Sheetmetal Design workbench, and to an obtuse
angle for the
Aerospace SheetMetal Design workbench. |
-
Select the edge as shown in red.
The Spine field is updated with the selected
edge.
The drop-down list offers two choices:
-
Basic: the flange is created along the whole
support.
-
Relimited: the flange is created within
limits you define on the support (points, for example).
-
Select Basic.
 |
Selecting Relimited updates the dialog with two new
fields (Limit 1 and Limit 2) to let you specify
the flange limits. You can then select as the limits two points, two
planar faces, a point and a planar face, or a point and a vertex, as
shown below, for example. Note that right-clicking in the Limit
1 and Limit 2 fields lets you create the limits
(points, plane) or choose the X, Y or Z plane on-the-fly.
|
|
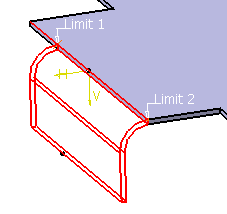 |
|
|
-
Choose the flange parameters:
-
Enter 15mm in the Length field. Use the
icons
next to the field
to specify the type of length. Note that the length is always computed
using the lowest external point of the flange.
-
Enter 45deg in the Angle field. Use the
icons next to the field to specify whether the angle is acute
or obtuse
.
-
Enter 2mm in the Radius field.
-
Check the Trim Support option to trim the
selected edge.
 |
The Trim Support option only works in the case of a planar
support. |
-
Click the Reverse Direction button to reverse
the direction of the flange.
-
Click the Invert Material Side button to
invert the material side. (This option is only available when the
Trim Support option is checked, otherwise it is deactivated.)
-
Click the More button to display the Bend
Allowance tab allowing you to locally redefine the bend allowance
settings.
Note that according to the DIN standard, if the radius
is modified, the K factor is adjusted accordingly.
You may need to deactivate the formula using the contextual menu on the
field and choosing Formula > Deactivate before editing the
value.
In this case, the new K Factor value overrides the value
set in the
Sheet Metal Parameters.
A preview of the flange to be created is displayed in the
geometry area.
-
When you are satisfied with the result, click OK
to create the flange. The flange is created and the feature is added to
the specification tree.