 |
This section explains how to change the different
sheet metal
parameters needed to create your first feature. |
 |
-
Click Sheet Metal Parameters
.
The Sheet Metal Parameters dialog box is displayed.
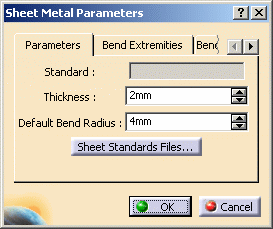
|
|
-
Change the Thickness if needed.
|
|
-
Change the Minimum Bend Radius
if needed.
The Minimum Bend radius defines the minimum internal radius allowing the
creation of a bend.
|
|
You can set the value to 0 to create bend with no radius. If
using the DIN standard, the KFactor automatically sets to 0 as well. |
 |
This option is only relevant with the Generative
Sheetmetal Design workbench. |
|
-
Change the Default Bend Radius if needed.
The Default Bend Radius corresponds to the internal radius and is linked
by default to the creation of the bends.
|
 |
Convention dictates that the inner
angle between the two elements is used to define the bend.
It can vary from 0deg to 180deg exclusive. This angle is constant and the
bend axis is rectilinear. |
 |
This option is only relevant with the Generative
Sheetmetal Design workbench. |
|
-
Click OK to validate the Sheet Metal
Parameters.
|
|
The Standard field
displays the Standard to use with the part, if implemented. The name of this
standard file is defined in a Design Table. |
 |
When the Check
all the bend radii button is checked, and you click OK in the Sheet
Metal Parameters dialog box, existing bend radii are checked and a list
displays flanges or bends that do not use the minimum Bend Radius value as
defined in step 3. Therefore, they will not be modified. |
 |
Parameters can be
defined in a Design Table. To do so, press the Sheet Standards Files...
button to access to the company-defined standards, if need be. For more
information, refer to the Customizing Standard Files section. |
|
All parameters hereafter, or only some of them,
can be defined in this Design Table: |
|
Sheet Metal Parameters |
Column associated in the Design Table |
Definition |
Standard in Sheet Metal Parameters |
SheetMetalStandard |
sheet reference name |
Thickness |
Thickness |
sheet thickness |
Minimum Bend Radius |
MinimumBendRadius |
minimum bend radius |
Default Bend Radius |
DefaultBendRadius |
default bend radius |
K Factor |
KFactor |
neutral fiber position |
Radius Table |
RadiusTable |
path to the file with all available radii |
|
 |
In all cases, the Thickness parameter must be
defined in the Design Table in order for the other parameters to be taken
into account. |
 |
Whenever both Radius Table and Default Bend Radius are
defined in the Design Table, only the Radius Table will be taken into
account for the bend creation. |
|
Standard Names For Holes |
Column associated in the Design Table |
Definition |
Clearance Hole |
ClearanceHoleStd |
path to the Clearance Hole Standard file |
Index Hole |
IndexHoleStd |
path to the Index Hole Standard file |
Manufacturing Hole |
ManufacturingHoleStd |
path to the Manufacturing Hole Standard file |
Fastener Hole |
FastenerHoleStd |
path to the Fastener Hole Standard file |
|
|
Standard Names For Stamps |
Column associated in the Design Table |
Definition |
Flanged Hole |
ExtrudedHoleStd |
path to the Flanged Hole Standard file |
Bead |
BeadStd |
path to the Bead Standard file |
Circular Stamp |
CircularStampStd |
path to the Circular Stamp Standard file |
Surface Stamp |
SurfaceStampStd |
path to the Surface Stamp Standard file |
Flanged CutOut |
FlangedCutoutStd |
path to the Flanged CutOut Standard file |
Curve Stamp |
CurveStampStd |
path to the Curve Stamp Standard file |
|
|
When a parameter refers to a path, another
sub-Design Table will be associated to the corresponding feature. |
|
1. Here is an example for the use of a bend
allowance table:
|
|
Main Sheet Metal Parameters Design Table |
|
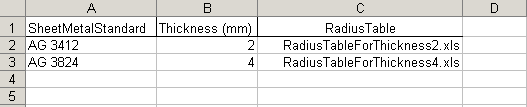 |
|
Radius Table For Thickness 2
This table defines available all bend radii for a thickness of 2 mm. A
design table will be created on the Default Bend Radius of the Sheet Metal
Parameters and on the Radius of each bend. |
|
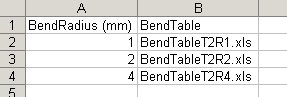
|
|
Bend Table for Thickness 2 and Bend Radius 1
Whenever a bend is created, a radius table will be associated. If the
configuration "Bend Radius = 1mm" is selected, a new design table (the
Bend Table) will be created from BendTableT2R1.xls in order to compute the
bend allowance.
According to the open angle, the bend deduction will be read in the
Allowance column or interpolated if necessary. |
|
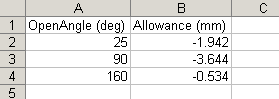
|
|
2. Here is an example for the use of a hole
standard file:
|
|
Main Sheet Metal Parameters Design Table |
|
 |
|
Hole Standard
Whenever a hole is created, a design table will associate its radius
with a standard name. |
|
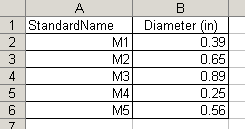
|
|
3. Here is an example for the use of a stamp
standard file:
|
|
Main Sheet Metal Parameters Design Table |
|
 |
|
Whenever a stamp is created, a design table
will associate its dimension with a standard name. |
|
|
|
|
|
 |
|
|
|
|
|
 |
|
|
|
|
|
 |
|
|
|
|
|
 |
|
|
|
|
|
 |
|
|
|
|
|
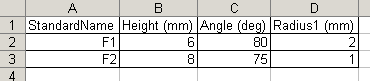 |
|
|
|
|
- Extruded Hole
(or Flanged Hole in the Generative Sheetmetal Design workbench)
|
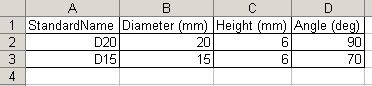 |
|
|
|
|
|
 |
 |