 |
This task shows you how to use Dynamic Smart Target
,
which creates a series of constraints on the fly, thereby reducing the
degrees of freedom of the components.
The objective is to snap the CHAINSAW_ENGINE_FLYWHEEL to the
CHAINSAW_ENGINE_CRANKSHAFT_LSIDE.1. |
 |
Depending on your configuration, you can use Dynamic Smart Target
in V5 workbenches that handle products (such as DMU Fitting) or processes
(such as DPM Assembly Process Simulation). In product workbenches,
you use Dynamic Smart Target
in conjunction with the Track ;
in DPM Assembly Simulation, you use Dynamic Smart Target
in conjunction with the Move Activity
. |
|
While creating or editing a track, a simulation or a shuttle, users
often wish to position an entity precisely. It can be useful to
cumulate several targets. Using a historical target (keeping track of
cumulative constraints) can help to put some elements in a specific
position.
The scenario below aims at showing you this capability:
- You are creating a track attached to Part2, you need this part to be
plugged into Part1
- Select Dynamic Smart Target
in the Manipulation toolbar
- Select the geometries you want to use as constraints for the snap,
such as L1, L2, L3 and L4, shown below (the selection order does not
matter).
- Manipulate Part2 so that it comes near to Part1. When the
selected constraint geometries (e.g., the axes L1 and L4) come near each
other, the parts will dynamically snap together with respect to the
constraints selected.
|
|
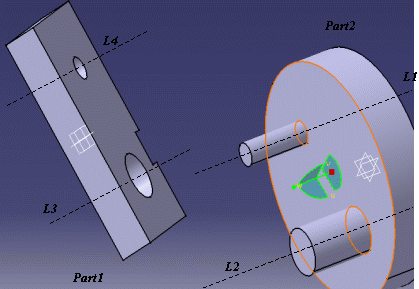 |
 |
Use the
SMART_SNAP.CATProduct document.
- For DMU Fitting, open the file in the product.
- For DPM Assembly Process Simulation, open the file in a workbench
such as DMU Fitting that creates .CATProducts. Then drag and drop
the geometry onto the ProductList node of the PPR tree.
|
 |
-
Select Tools > Options > DMU Fitting > DMU
Manipulation to verify the snapping settings.
Set (if necessary) values for:
- Position: 6mm (default value)
- Orientation: (default value)
|
-
Verify that you are familiar with the location and
appearance of the geometries with which you are working:
You want to snap the CHAINSAW_ENGINE_FLYWHEEL1 product to the
CHAINSAW_ENGINE_CRANKSHAFT_LSIDE product. |
-
Perform one of the following:
|
-
Select the shuttle.
-
Click Track
in the DMU Simulation toolbar.
|
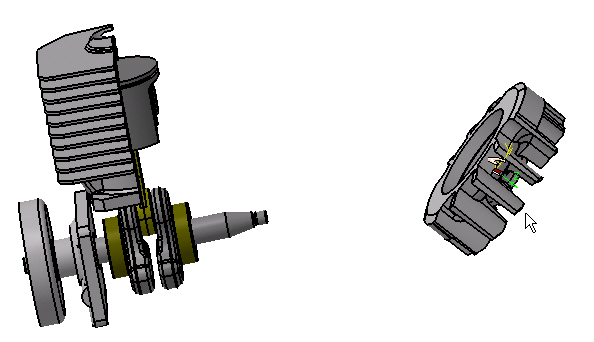 |
- In DPM Assembly Process Simulation:
|
-
Select the Process node.
-
Click Move Activity
in the Simulation Activity Creation toolbar.
-
Select the part to be snapped (in this example,
the engine flywheel).
-
Click OK in the Edit Shuttle
dialog box.
|
In DPM Assembly Process Simulation and DMU Fitting, the
Player, Recorder, and Manipulation
pop-up toolbars appear, as well as the Track dialog box. |
-
Click Dynamic Smart Target
in the Manipulation toolbar.
The Track dialog box and the
Recorder and Player pop-up
toolbars disappear. |
-
Select the desired constraint geometries (the selection
order is not relevant; see below for a key to the
tokens used to designate the geometries).
- For this example, first select the axis (cylinder) on the
CHAINSAW_ENGINE_CRANKSHAFT_LSIDE product and click to confirm the
operation.
|
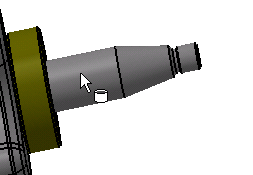 |
- Then, select a plane (inner one) on the
CHAINSAW_ENGINE_FLYWHEEL1 product and click to confirm the
operation.
|
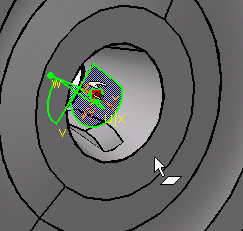 |
Back to the CHAINSAW_ENGINE_CRANKSHAFT_LSIDE product, select the
inner plane as shown below and click to confirm the
operation. |
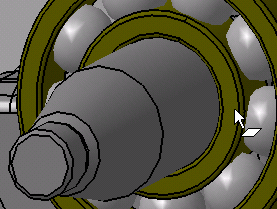 |
To finish, you need to select another axis on the
CHAINSAW_ENGINE_FLYWHEEL1. |
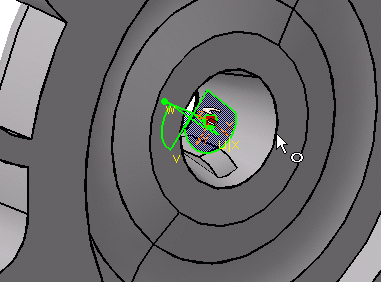 |
-
Click OK.
-
Move the shuttle so as to get it near the object.
` |
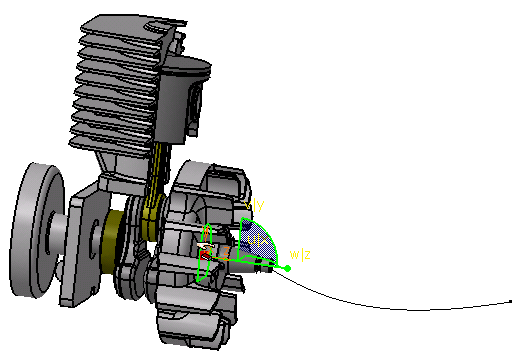 |
The planes are snapped together as well as the axes. |
-
Click Dynamic Smart Target
(highlighted in orange).
The Track dialog box and the
Recorder and Player pop-up
toolbars reappear. |
-
Click Record
to record the movement of the part as a track.
The track is created; you can replay it using the
Player commands. |
-
Click OK in the Track dialog box.
|
 |
Selectable
elements |
Design Mode |
Visualization mode |
Point |
 |
Yes |
Yes |
Line
 |
Yes |
Yes |
V4 Axis System |
 |
Yes |
Yes |
Plane |
 |
Yes |
Yes |
|