|
This task shows how to create a multi-sections
surface and includes the following functionalities:
You can generate a multi-sections surface by sweeping two or more
section curves along an automatically computed or user-defined spine. The
surface can be made to respect one or more guide curves. |
|
Open the
Loft1.CATPart document. |
 |
-
Click Multi-sections Surface
.
The Multi-sections Surface Definition dialog box appears. |
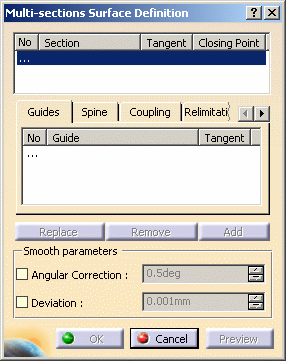 |
-
Select two or more planar section curves.
 |
- The curves must be continuous in point.
- You can select tangent surfaces for the start and end section
curves. These tangent surfaces must not be parallel to the
sections.
|
 |
A closing point can be selected
for a closed section curves. |
-
Click Preview.
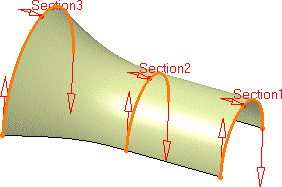 |
Multi-sections surface defined by three planar
sections |
|
 |
Sections can be 3D curves
providing that the intersection between one 3D profile and all guides
is coplanar (if three guides or more are defined). |
-
If needed, select one or more guide curves.
 |
Guide curves must intersect each
section curve and must be continuous in point. |
The first guide curve will be a boundary of the
multi-sections surface if it intersects the first extremity of each
sections curve. |
Similarly, the last guide curve will be a boundary of
the multi-sections surface if it intersects the last extremity of
each section curve. |
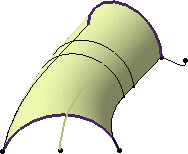 |
Multi-sections surface defined by 2 planar
sections and 2 guide curves |
|
You can make a multi-sections surface tangent to an
adjacent surface by selecting an end section that lies on the
adjacent surface. In this case, the guides must also be tangent to
the surface. |
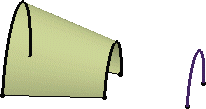 |
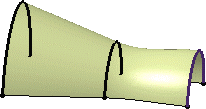 |
Multi-sections surface tangent to the existing
surface |
|
|
You can also impose tangency conditions by specifying
a direction for the tangent vector (selecting a plane to take its
normal, for example). This is useful for creating parts that are
symmetrical with respect to a plane. Tangency conditions can be
imposed on the two symmetrical halves. |
Similarly, you can impose a tangency onto each guide,
by selection of a surface or a plane (the direction is tangent
to the plane's normal). In this case, the sections must also be
tangent to the surface. |
-
Click OK to create the multi-sections surface.
The surface (identified as Multi-sections Surface.xxx) is added
to the specification tree. |
In case a section is defined by a closed curve,
extremum points are aggregated under
the parent command that created them and put in no show in the
specification tree. |
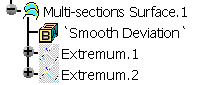 |
|
|
Editing a Multi-sections Surface
|
|
Double-click the multi-sections surface either in the 3D
area or in the specification tree. More possibilities are available with the contextual menu:
-
right-click the surface to access the following options:
-
right-click the multi-sections surface reference
elements, either a curve in the dialog box list or the red text on the figure
to access the following options:
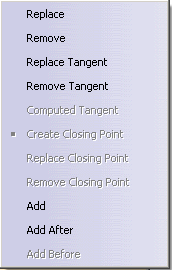 |
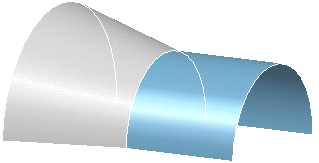 |
Above is the result when the tangency condition is removed
between the blue multi-sections surface and the adjacent surface |
|
|
Defining Smooth Parameters
|
|
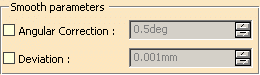
|
|
In the Smooth parameters
section, you can check:
- Angular Correction to smooth the lofting motion along the
reference guide curves. This may be necessary when small discontinuities
are detected with regards to the spine tangency or the reference guide
curves' normal. The smoothing is done for any discontinuity which angular
deviation is smaller than the input value, and therefore helps generating
better quality for the resulting multi-sections surface.
Over 0.01 degree, the smoothing is cancelled.
By default, the angular correction is set to 0.5 degree.
- Deviation to smooth the lofting motion by deviating from
the guide curve(s). A smoothing is performed using correction default
parameters in tangency and curvature.
By default, the deviation is set to 0.001mm, as defined in Tools >
Options. Refer to General Settings for more information.
 |
- If you are using a both Angular Correction and
Deviation options, it is not guaranteed that the spine plane
be kept within the given tolerance area. The spine may first be
approximated with the deviation tolerance, then each moving plane
may rotate within the angular correction tolerance.
- Do not specify a deviation on a
multi-sections surface, solid or volume that should be in contact
with guide curves.
|
|
|
Selecting a Spine
|
|
In the Spine
tab page, select the Computed Spine check box to use a spine
that is automatically computed or select a curve to impose that curve as
the spine. |
|
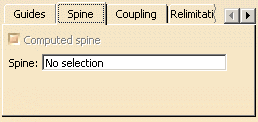
|
|
- It is strongly recommended that the spine curve be normal to each
section plane and must be continuous in tangency.
Otherwise, it may lead to an unpredictable shape.
- If the plane normal to the spine intersects one of the guiding curves
at different points, it is advised to use the closest point to the spine
point for coupling.
- You can create multi-sections surfaces between closed section curves.
These curves have point continuity at their closing point.
This closing point is either a vertex or an extremum point automatically
detected and highlighted by the system.
By default, the closing points of each section are linked to each other.
The red arrows in the figures below represent the
closing points of the closed section curves. You can change the
closing point by selecting any point on the curve. |
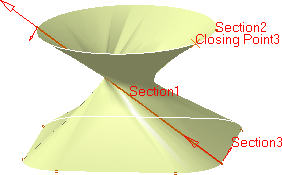 |
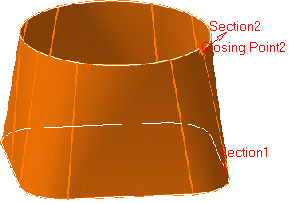 |
The surface is twisted: |
A new closing point has been imposed to get a non-twisted
surface: |
|
|
Relimitating the Multi-sections Surface
|
|
The Relimitation tab lets you specify the
relimitation type.
You can choose to limit the
multi-sections surface only on the Start section, only on the End section,
on both, or on none. |
 |
Open the
Loft3.CATPart document. |
|
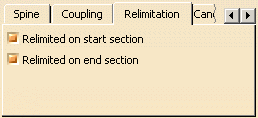
|
|
- when none of the options are checked: the swept surface is
extrapolated up to the spine limits.
- when both options are checked: the multi-sections surface is limited
to corresponding sections
- when one or both options are unchecked: the multi-sections surface is
swept along the spine:
- if the spine is a user spine, the multi-sections surface is limited
by the spine extremities or by the first guide extremity met along the
spine.
- if the spine is an automatically computed spine, and no guide is
selected: the multi-sections surface is limited by the start and end
sections
- if the spine is an automatically computed spine, and one or two
guides are selected: the multi-sections surface is limited by the
guides extremities.
- if the spine is an automatically computed spine, and more than two
guides are selected: the spine stops at a point corresponding to the
barycenter of the guide extremities. In any case, the tangent to the
spine extremity is the mean tangent to the guide extremities.
Both options checked: |
End section option unchecked: |
|
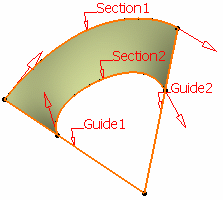 |
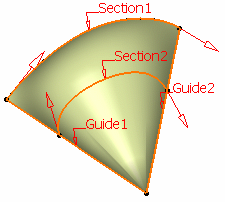 |
 |
After the multi-sections surface is relimited, the following
constraint needs to be fulfilled: the plane normal to the spine
defined at the relimitation point must intersect the guide(s) and
the point(s) resulting from this intersection must belong to the
section. |
|
|
Using a Canonical
Element
|
|
Use the Canonical portion detection
check button in the Canonical Element tab to automatically detect planar
surfaces to be used as planes for features needing one in their definition. |
|
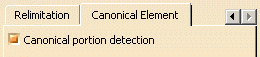 |
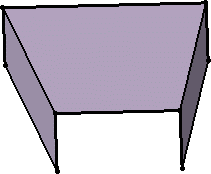 |
Initial multi-sections surface with planar faces |
|
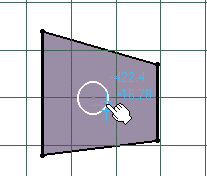 |
Using a planar face as reference for a sketch |
|
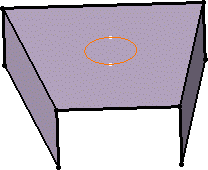 |
Resulting sketch |
|
Coupling
|
|
This task presents the three kinds of coupling
during the creation of the multi-sections surface surface:
These couplings compute the distribution of isoparameters on the
surface. |
|
Open the
Loft2.CATPart document. |
|
Coupling between two consecutive sections
|
|
This coupling is based on the curvilinear
abscissa. |
 |
-
Click Multi-sections Surface
.
The Multi-sections Surface Definition dialog box appears. |
-
Select the two consecutive sections.
-
Click OK to create the multi-sections surface.
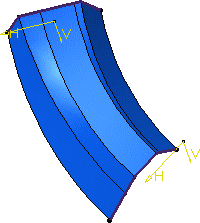 |
If you want to create a coupling between particular
points, you can add guides or define the
coupling type. |
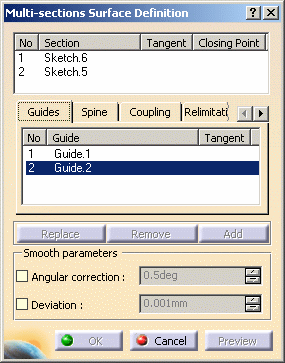 |
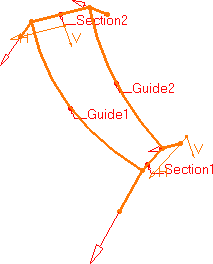 |
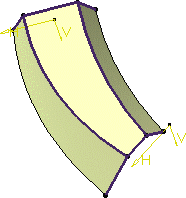 |
|
|
Coupling between guides
|
|
This coupling is performed by the spine. |
|
If a guide is the concatenation of several
curves, the resulting multi-sections surface will contain as many surfaces
as curves within the guide. |
|
|
|
|
Several coupling types are
available, depending on the section configuration:
- Ratio: the curves are coupled according to the curvilinear
abscissa ratio.
- Tangency: the curves are coupled according to their
tangency discontinuity points. If they do not have the same number of
points, they cannot be coupled using this option.
- Tangency then curvature: the curves are coupled according
to their tangency continuity first then curvature discontinuity points.
If they do not have the same number of points, they cannot be coupled
using this option.
- Vertices: the curves are coupled according to their
vertices. If they do not have the same number of vertices, they cannot be
coupled using this option.
|
|
Manual Coupling
|
|
If the number of vertices differ from one
section to another, you need to perform a manual coupling. |
 |
-
Select the sections for the multi-sections surface, and
check their orientations.
-
In the Coupling tab, choose the Tangency
option and click Preview.
An error message is displayed as the number of discontinuity
points on the first section is greater than on the other two
sections. |
The points that could not be
coupled, are displayed in the geometry with specific symbol depending
on the selected mode, along with coupling lines: |
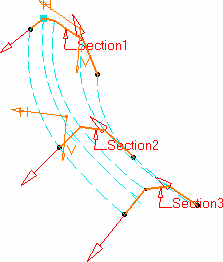 |
- In Tangency mode: uncoupled tangency discontinuity
points are represented by a square.
|
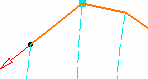 |
- In Tangency then curvature mode:
- uncoupled tangency discontinuity points are represented by a
square
- uncoupled curvatures discontinuity points are represented by
a empty circle
|
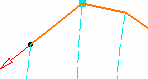 |
- In Vertices mode: uncoupled vertices are represented
by a full circle
|
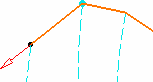 |
-
Click in the coupling list, or choose Add in
the contextual menu, or using the Add button, and manually
select a point on the first section.
The Coupling dialog box is displayed. |
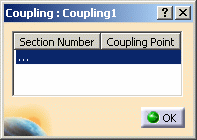 |
-
Select a corresponding coupling point on each section of
the multi-sections surface.
The Coupling dialog box is updated consequently, and the coupling
curve is previewed, provided Display coupling curves is
selected. |
When a coupling point has been defined on each section, this
dialog box automatically disappears. |
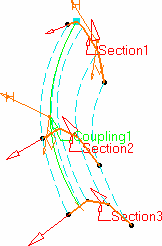 |
-
Click OK.
The multi-sections surface is created as defined with the
coupling specifications. |
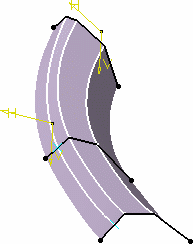 |
The same multi-sections surface without coupling and with Ratio
option would have looked like this: |
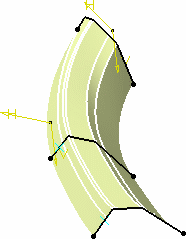 |
Note the increased number of generated surfaces. |
|
|
 |
- You can create coupling point on the fly, using the
Create coupling point contextual menu item (click in the 3D
area to display the contextual menu) instead of selecting an
existing point.
- To edit the coupling, simply double-click the coupling name
in the list (Coupling tab) to display the Coupling dialog box.
Then you select the point to be edited from the list and
create/select a replacing coupling point, then click OK.
- Use the contextual menu on the coupling list to edit defined
couplings.
|
|
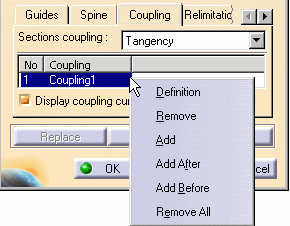 |
|
 |