-
Still in the same CATProduct, hide all elements in the
MoldedPart apart from the PartBody.
-
Make MoldedPart the Define in Work Object
with its contextual menu
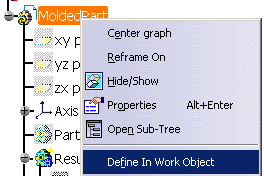
and insert a new Geometrical set.
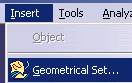
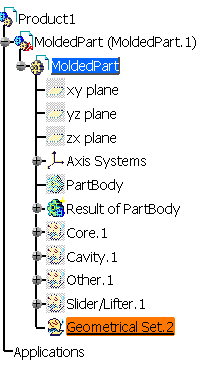
-
You are now going to create two lines that will define the
edge of the face split.
Click Create a Line
.
Choose tangent to curve as line type. For the first line:
Pick this curve,
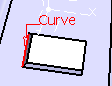
this point (element 2),
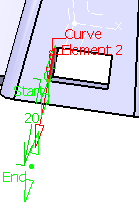
and this support
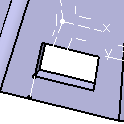
If necessary, click Reverse Direction.
Click OK to create the line.
-
Create the second line with the same support but with this
point and this curve:
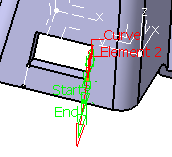
-
Now we are going to join the lines. Click Join
.
Make sure that the Check connexity check box is not
selected and select the two lines that you have just created.
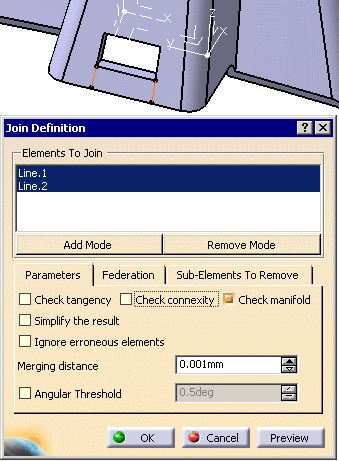
-
Click OK.
-
In the tree, hide the PartBody and show all of the other
elements in the MoldedPart.
-
You are now going to split the face with the hole with the
join that you just created.
Click Split Mold Area
in the Pulling Direction toolbar.
-
Select the face with the hole as the
Element to
Cut and the join you just created as the
Cutting
Element.
-
Click Apply.
-
Select Surface.16 in the dialog box, give
Slider/Lifter.1 as the destination and click
Change
Destination button.
Repeat this for Surface.17 that you will send to Cavity.1.
-
Click OK.