 |
This task illustrates how to recognize
an existing part as a sheet metal part, i.e. recognize as sheet metal
features the thin part shapes of a part created using the Part Design
workbench or of a CATIA Version 4 Solid, for example. You can also use this
functionality to recognize parts created using the SheetMetal Design
workbench as Generative Sheetmetal Design parts. Currently, walls and
bends can be recognized. Hems are recognized as walls. |
 |
Before recognizing your part, we advice you to copy-paste as result it
in a new part. |
 |
Walls and cylindrical bends only can be recognized. Hems are recognized as
walls.
|
 |
Open the
NEWRecognize01.CATPart document.
This document contains a part created in the Part
Design workbench: |
|
 |

|
-
Click Recognize
.
The Recognize Definition dialog box is displayed.
-
Select a reference face. It will be the reference face
for unfolding and for the definition of the
sheet metal parameters (i.e. all default parameters will be based on
this face).
 |
You can get a preview of
the recognized features by clicking the
Display recognized features
button: it allows you to highlight them with the selected color. |
-
Click OK to validate.
The walls are generated from the Part Design geometry. The
Recognize.1 feature is added to the tree view.
At the same time, the sheet metal
parameters are created, deduced from the Part geometry. |
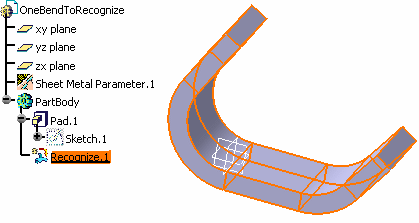 |
-
Click Sheet Metal Parameters
.
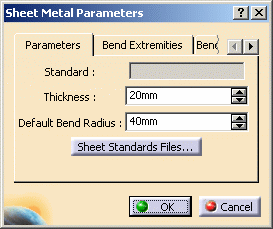 |
|
On the Parameters tab:
-
the Thickness is equal to 20mm,
-
the Default Bend Radius value amounts to
twice that of the thickness.
On the Bend Extremities tab:
You can modify a few of these parameters. The
Thickness parameter cannot be modified because it is based,
like the bend extremities and radius, on the initial solid geometry.
However, you can modify other parameters (default bend radius and
bend extremities) in order for them to be taken into account for
sheet metal features other than the "recognized" ones.
The bend allowance, being used to unfold the part,
and the bend corner relief affect all features, and therefore can be
edited even for "recognized" features. |
 |
You can also define the sheet metal parameters prior to
recognizing the part. In this case, you need to make sure that the
Thickness parameter value corresponds to the part
thickness. |
-
When all parameters have been redefined as needed, click
OK in the Sheet Metal Parameters dialog box.
The solid is now a Generative Sheetmetal Design part. You can now deal
with it as with any other Generative Sheetmetal Design part, adding
Generative Sheetmetal Design features to complete the design, or
unfolding it.
 |
In certain cases, there may be an ambiguity as regards the faces
from which the walls are to be generated.
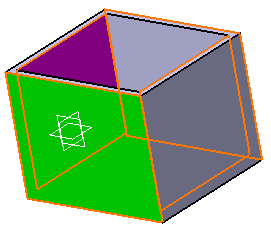 |
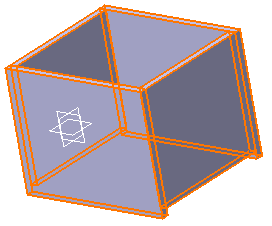 |
Faces to select |
Recognition result |
For example, if the initial part is a box such as shown below, you
need to select two opposite inner faces, and outer faces on the other
two sides of the box, in order to avoid overlapping when recognizing
the walls.
In case faces are overlapping, you need to select the sides of
each face. If you select only one face, the overlapping faces will be
recognized as a unique pad and not as two
independent walls.
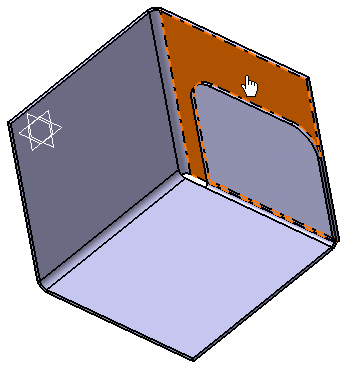 |
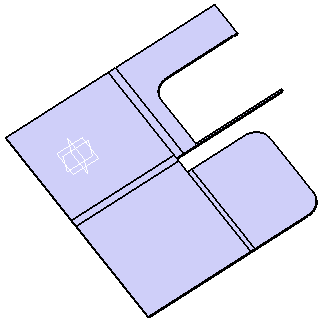 |
Face selected to be recognized as a wall |
Result of recognition when unfolding |
To avoid this, select first the inner side
of the overlapping faces.
Then select the outer side.
The overlapping faces will be recognized as
independent walls.
|
|
|
Recognizing Stamping Features
|
 |
This task illustrates how to recognize a stamp
geometry in order to create a Generative Sheetmetal Design stamping feature
provided it is on a planar and single support.
Consequently, the following types of stamps can be recognized:
- Circular stamp
- Curve stamp
- Surface stamp
- Bead
- Bridge
- Louver
The recognize feature enables to create a Generative Sheetmetal Design
stamping feature from a V4 model or parts created with Sheetmetal Design.
|
 |
The Part Feature Recognition license is required to
activate this feature in the Generative Sheetmetal Design Workbench. |
 |
Open the
NEWRecognize03.CATPart document. This document contains a part created
from a V4 model. |
 |
-
Click Recognize
.
The Recognize Definition dialog box is displayed.
-
Select a reference face. It will be the reference face
for unfolding and for the definition of the
sheet metal parameters (i.e. all default parameters will be based on
this face).
-
Click OK.
The stamps are generated from the geometry. |
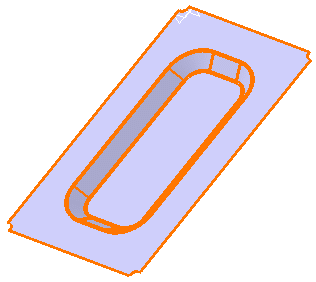 |
 |
Three
modes are available for the recognition :
|
 |
You can also force a face to be recognized as one feature by
selecting it in the
Face to keep
field.
For instance, in the following part pink faces are
usually recognized as walls and bends, and blue faces as a stamp.
But you can also choose the blue faces to be recognized as walls and
bends by selecting them in the
Face to keep
field of the Walls and Bends
tab.
|
|
- There is no stiffening rib recognition, since the support feature
for the stamp must be planar.
- Stamps containing inner contours such as flanged hole, flanged
cutout cannot be recognized.
- Sharp stamps are not recognized.
|
|
|
Managing the Bend Allowance
|
 |
This task illustrates how to specify the K-Factor in a recognition context. |
 |
Open the
NEWRecognize04.CATPart document. |
|
-
Click Recognize
.
The Recognize Definition dialog box is displayed.
-
Select a reference face. It will be the reference face
for unfolding and for the definition of the
sheet metal parameters (i.e. all default parameters will be based on
this face).
-
Click on the Bend Allowance tab.
-
Select the bend you want to recognize.
 |
Every bend
on which you specify a K-Factor is entered in the
Bending face box. |
-
Specify the value of the K-factor.
 |
- This K-Factor will only be applied on the bend
you selected.
- The bends you do not select will keep the default
K-Factor value.
|
 |
You can also edit the K-Factor value by clicking on the
K-Factor text symbol on the geometry. |
 |
You cannot specify 2 different K-Factor values
on the 2 faces of the same bend. |
-
Click OK.
|
 |