|
-
Click Fill
.
The Fill Surface Definition dialog box appears. |
-
Select curves or surface edges to form a closed boundary.
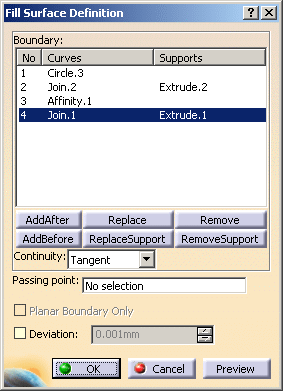 |
You can select a support surface for each curve or edge. In this
case continuity will be assured between the fill surface and selected
support surfaces. |
-
Use the combo to specify the desired continuity type
between any selected support surfaces and the fill surface:
|
The fill surface is displayed within the boundary. |
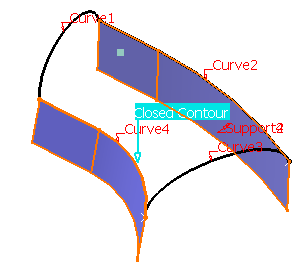 |
-
You can edit the boundary by first selecting an element
in the dialog box list then choosing a button to either:
-
Add a new
element after or before the selected one
-
Remove the
selected element
-
Replace the
selected element by another curve
-
Replace the
selected support element by another support surface
-
Remove the
selected support element.
|
-
Click in the
Passing point field, and select a point.
This point is a point through which the filling surface must
pass, thus adding a constraint to its creation. However, you may need
to alleviate the number of constraints by removing the supports. |
 |
This point should lie within the
area delimited by the selected curves. If not, the results may be
inconsistent. |
-
You can check Planar
Boundary Only to fill only planar boundaries, when the boundary is
defined by one curve on one surface.
-
 |
|
 |
|
-
Click OK to create the fill surface.
|