
 |
This task will show you how to create surfaces
automatically from a mesh.
- The Automatic Surface command is adapted to many types of shapes.
- It can create complex surfaces with a minimum set of Nurbs.
- It can take holes into account.
- It preserves fillet with small radius (but not very sharp
edges).
- Surfaces can be created with or without a full internal
tangency between faces.
The input required is a mesh (not a cloud of points):
- it may not have non-manifold vertices or triangles,
- it must be a mono-cell mesh, without non-connex zones,
|
 |
Sharp edges are not preserved. |
 |
Open the
AutomaticSurf.CATPart from the
samples directory. |
 |
-
Click Automatic Surface
.
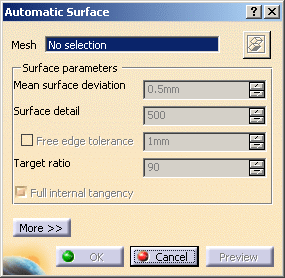
-
Select Sample as the
Mesh. The
is now available and enables you to hide or show the mesh.
-
Type the
Mean surface
deviation,
i.e. the average deviation between the surface that will be created and
the input mesh,
computed on all mesh vertices.
-
Click Preview to preview the surface.
-
Click More to have access to statistics and
some display check boxes:
The Statistics
are:
- output faces:
global count of faces contained in the output surface,
- Max surface deviation:
value of the maximum deviation between the surface and the mesh,
also displayed with the spikes,
- Max free edges deviation:
value of the maximum deviation between the free edges and the mesh,
also displayed with the spikes,
- Mean surface deviation:
value of the mean deviation between the surface and the mesh,
- xx% of yyy points Ok:
percentage of the measured points that are under the Mean
surface deviation.
-
Select the
Spikes check box to visualize the deviations between the mesh
and the surface:
- The points with the maximum deviation on the surface or
on free edges are displayed on a small yellow rectangle,
with the corresponding value of the deviation.
- Deviation enables you to display only the spikes on
points
with a deviation greater than this value.
- Negative and positive deviations are displayed in different
colors.
- Click
to visualize the deviations on the surface:
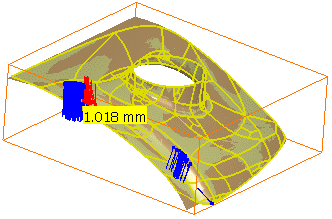
- Click
to visualize the deviations on the free edges
(only availbable when free edges exist):
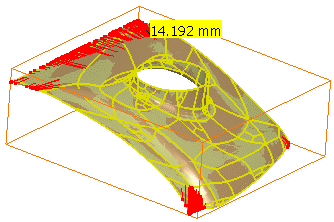
-
Click OK. Surface.2 is created.
|
|
Tuning parameters
Helps you increase or decrease the respect of mesh details on the
resulting surface:
the higher the value, the higher the respect of details.
The proposed range value is just an indication. It can be edited through
its contextual menu:
- The Surface detail is set to 500:
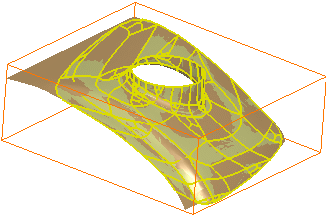
- The Surface detail is set to 1000:
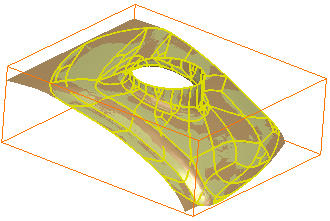
Chordal value used to sample the mesh boundaries.
Select this check box to improve the quality of the surface with respect
to the mesh boundaries.
- Free edge tolerance is not selected:
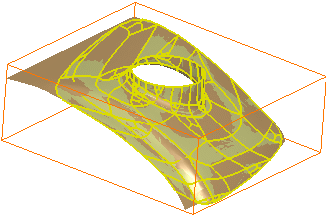
- Free edge tolerance is selected:
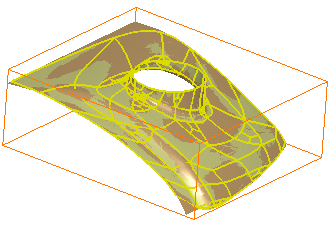
Ratio of measured points with a surface deviation under the Mean
surface deviation value.
- The actual ratio obtained may be different (greater or lower) than the
one you have requested.
- A ratio next to 100 is time consuming.
|
 |
If the Mean surface deviation or the Target
ratio requested cannot be reached,
the surface is created and a message is displayed. |
|
By default, this check box is selected and provides a full
internal tangency between the faces of the output surface.
If full internal tangency is not mandatory, you can clear this
check box. The output will be smaller in term of memory size and control
points. However, you will not be able to recover full internal tangency
later on, e.g. with healing or filleting commands. Nor will you be able to
perform thickness or offset operations on the output surface. |
 |