-
Select File > New
Select Part in the list.
-
Using the contextual menu, edit the part properties,
go to the Product tab and type MoldedPart as its
Part Number.
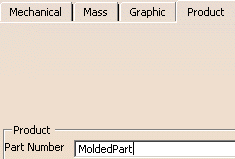
(You can also begin by creating a mold base
which automatically
contains
an empty MoldedPart where you can complete the steps given
below).
-
Open the
Tel.CATPart file in the Samples directory. This opens a new viewer.
-
Select the PartBody in the
specifications tree and copy it.
-
Select the Part in the
MoldedPart viewer and use the Paste special function in
the contextual menu.
-
Select AsResultWithLink in the
dialog box and click OK.
This ensures that if the original part to mold is modified that the
modifications will be applied to the MoldedPart.
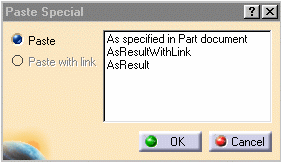
-
You can now
perform a scaling operation to take account of shrinkage:
- Select Start > Mechanical Design > Part Design.
- Right-click Body.2 in the specifications tree and
select Define In Work Object in the contextual menu.
- Click Scaling
.
- Type a ratio value of 1.03 (for example), select the xy plane in
the tree as reference and click OK.
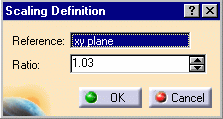
|
Repeat this action for the yz and zx planes with
different ratio values. |
-
Now
determine the pulling direction with Draft Analysis or the
Core and Cavity Design workbench:
the main pulling direction is defined when the CavitySurface and the
CoreSurface are separated.
From the Core and Cavity Design workbench, you obtain surface
joins for the CavitySurface and the CoreSurface.
An axis system is also created and used for the definition of the main
pulling direction.
-
Hide Core.1, Cavity.1, Other.1
and NoDraft_1deg.1.
-
Select Start > Shape > Generative Shape Design.
Insert an Geometrical set and name it PartingBody.
-
Click
Join
.
-
Select all of the bottom edges of the part. Click OK
in the dialog box to confirm the action.
-
Right-click the new join in the specifications tree to
open its properties and call it PartingLine.
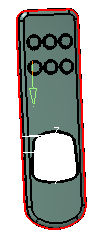
-
Now you are going to fill the hole on the part to enable
the split of the CavityPlate and of the CorePlate.
Join the curves around the hole and click OK in the dialog box.
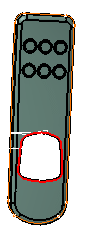
-
Click Fill
.
Select Join.2 in the specifications tree.
Click OK in the dialog box. The hole is filled.
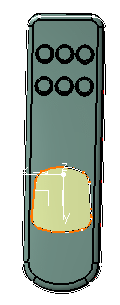
-
The next
thing you are going to do is to create the
parting surface.
- Click Sweep
.
- Click the Line Profile button in the dialog box.
- Select With reference surface for the Subtype.
- Select PartingLine in the specification tree for the
guide curve.
- Select xy plane in the specification for the Reference
surface.
- Type a value of 20 mm for Length 1.
- Click OK.
|
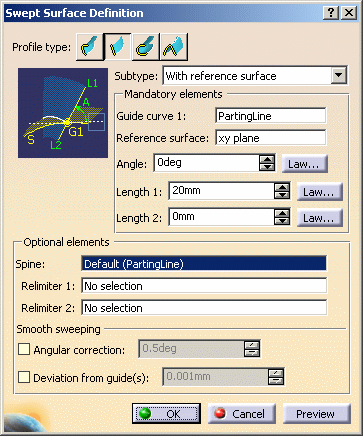 |
-
The parting surface is created
(if it is created in the wrong direction, i.e. in the inside of the part,
swap the values of Length 1 and Length 2).
Using the contextual menu, change the sweep name to PartingSurface.
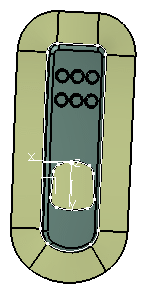
-
Click Extract
.
Since the PartingSurface is shared by both the
CavitySurface and the CoreSurface,
it is generated on
both.
Select Tangent continuity in the Propagation type
list and
pick any face on the upper surface in the viewer for the To
Extract box.
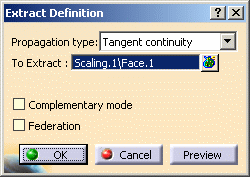
-
Turn the part over and repeat this step for the underside
surface.
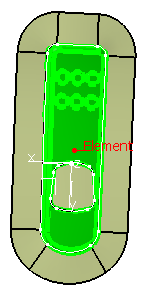
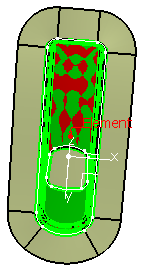
-
Click Join
.
Select PartingSurface, the fill and the first extract in the
specification tree.
Clear the Check connexity check box.
Click OK.
-
Right-click
the new join in the tree.
Select Properties in the contextual menu and change the name to
CavitySurface.
-
Repeat the action with the parting surface, fill and the
second extract.
Call the new join
CoreSurface.
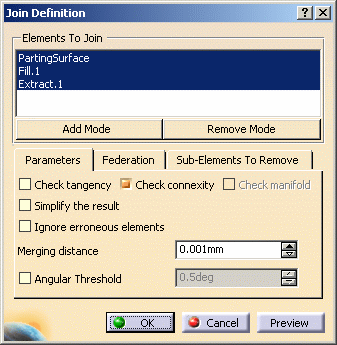
Your specification tree should look like this:
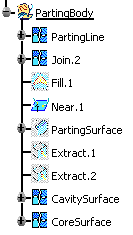