 |
This task shows you how to
automatically create axial machinable features and a machining pattern in a
single step. |
 |
Open the
HoleMakingOperations.CATPart
document, then select the desired Machining workbench from the
Start menu. |
 |
1. |
Select the Global Feature Recognition
icon
.
The Global Feature Recognition dialog box appears. |
|
2. |
In the Basic tab page, select the Hole checkbox to
create axial machinable features only. Select the top face of the part in
the 3D view. 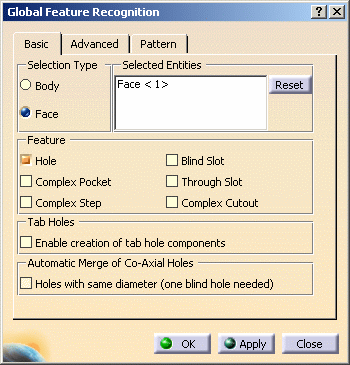
|
|
6. |
In the Pattern tab page, set the parameters for
pattern creation as follows.

With these parameters you will create a pattern on threaded holes whose
diameter is included in a specified range of diameters (that is, between 17
and 20mm). |
|
7. |
Select the Manufacturing View icon
and display the view sorted by patterns.The created machining pattern is
displayed. |
|
|
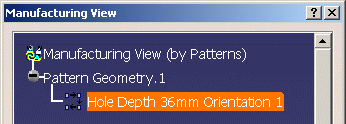 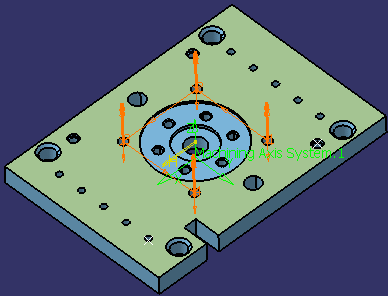
|
|
8. |
Double click the machining pattern node to display the
Machining pattern dialog box to obtain more information about the pattern. |
|
|
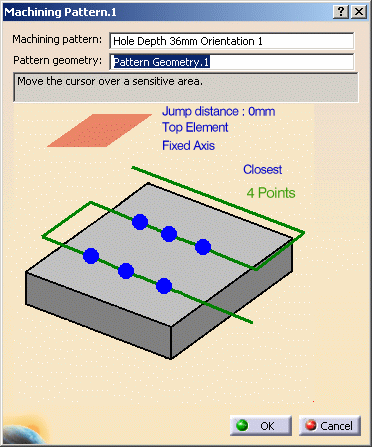
|
 |
|
Geometry Considerations for Pattern Creation
Pattern creation operates on a set of axial features selected from the
Manufacturing View, a set of faces, or an entire body.
- For a set of axial features, pattern creation applies the
matching criteria only to that set of features.
- For a set of planar faces, pattern creation applies the
matching criteria to all axial features from each face in the set. Note
that all features in a pattern will have identical axes.
If a reference direction is defined, the matching criteria only applies
to axial machinable features parallel to this axis.
- For a set of non-planar faces, pattern creation applies the
matching criteria to all axial features from each face in the set.
Features in the pattern can have different axes.
If a reference direction is defined, automatic pattern creation only
applies to axial machinable features parallel to this axis.
- For a body, pattern creation applies the matching criteria to
all axial features. Note that all features in a pattern will have
identical axes.
If a reference direction is defined, automatic pattern creation only
applies to axial machinable features parallel to this axis.
Using Tolerances in Pattern Creation
You can retrieve the fitting tolerances defined in design features when
machinable axial features are created. You can match these tolerance values
in the pattern creation functionality.
The Tolerance Value checkbox for matching the fitting
tolerance for pattern creation.
You can create patterns of holes having same tolerance values. Matching
is done for both tabulated (H7, and so on) as well as minimum/maximum
tolerance values.
Features having the same tolerance values are grouped in the same pattern.
Other holes, for which the tolerance value is not defined, will form a
separate pattern.
The fitting tolerance value is retrieved and information is displayed to
user:
- in the dialog box of the Machinable axial feature:
- in the Manufacturing View on the created pattern:
|
|
|
Pattern Creation with Color Criteria
When you select the Color checkbox for pattern creation,
colors of holes are matched for creating patterns. The color of the axial
machining feature faces is taken into account for pattern creation.
This color may be a basic color or a RGB color (Red, Green, Blue value).
Note that all holes have a color. When no specific color is defined on
the faces, the face color is the same than the body color.
- If only the Color checkbox is selected then all the holes
with same machining axis and having same color will form a pattern.
This behavior is similar to other pattern creation options. For all the
pattern creation options a created pattern will have holes with same
machining axes.
Exception to this is holes having non-planar top faces.
When there are some holes having non-planar top faces and if none of the
holes have the axis same as any of the planar holes, then these holes can
form a single pattern even if their axes do not match.
- If other criteria are also selected along with color then holes
matching all the other criteria and color will form one pattern.
- If only color is selected and machining direction is specified, then
all the holes having axis parallel to machining direction and having same
color will form one pattern. Holes, which do not have axis parallel to
machining direction, will not form any pattern.
- If the holes have more than one color, these holes will come under a
separate pattern for that specific orientation.
Example:
Part with counterbored holes (same hole and counterbored diameters):
10 counterbored without specific color
10 counterbored (all faces in red)
10 counterbored (first diameter face in blue, second diameter face in
red, other faces without specific color).
Hole with more than one color will be taken into account in a specific
pattern.
Three patterns will be created:
pattern for the undefined color (10 holes)
pattern for the red color (10 holes)
pattern for the holes with more than 1 color (10 holes).
Pattern Naming:
If user has selected the color option for pattern, RGB color definition
will be added at the end of pattern name as Color (R value, G value, B
value). |
 |