In this particular example, select the General
Analysis Connection.1 in the specification tree (under the
Analysis Connection Manager.1 set).
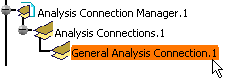
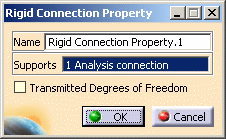
A symbol representing the Rigid Connection Property
is visualized on the corresponding faces.
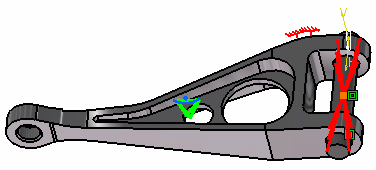
By default, if you deactivate the Transmitted
degrees of freedom option, all the degrees of freedom are
transmitted.
You can also release some degree of freedom to the
distant connection, if needed.
The degrees of freedom are released at the null-length element.
Translation 1 = Translation in x
Translation 2 = Translation in y
Translation 3 = Translation in z
Rotation 1 = Rotation in x
Rotation 2 = Rotation in y
Rotation 3 = Rotation in z
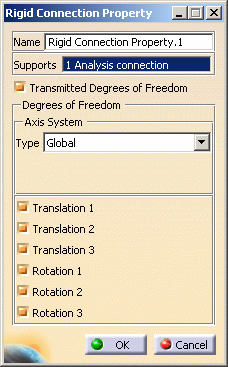
The Axis System Type combo box allows you to choose
between Global or User-defined Axis systems for
defining the degrees of freedom directions.
-
Global: if you select the Global Axis
system, the degree of freedom directions will be interpreted as
relative to the fixed global rectangular coordinate system.
-
User: if you select a User Axis
system, the degree of freedom directions will be relative to the
specified Axis system. Their interpretation will further depend on
your Axis System Type choice.
 |
The degrees of freedom are released only for
the null-length element, so the User Axis System is
defined only for the null-length element. |
To select a User-defined Axis system, you must
activate an existing Axis by clicking it in the features tree.
Its name will then be automatically displayed in the
Current Axis field.
If you select the User-defined Axis system, the
Local orientation list further allows you to choose
between Cartesian and Cylindrical Local
Axis Orientations.
-
Cartesian: the degrees of freedom
directions are relative to a fixed rectangular coordinate
system aligned with the cartesian coordinate directions of
the User-defined Axis.
-
Cylindrical: the degrees of
freedom directions are relative to a local variable
rectangular coordinate system aligned with the
cylindrical coordinate directions of each point relative to
the User-defined Axis.
|
|