The branch point or
branch end closest to the point of selection is selected as the
rotate point and is highlighted.
Make your selection in the specification tree, since the exact position of the
selected point has to be known.
Note: If a branch point is selected as the rotate point, a
message asks the user to confirm the split of the branch into two at
the selected branch point.
A green arrow and a dialog box appear at the same
time.
The green arrow indicates the direction of rotation appears
on the geometry area and the impacted bundle segment is highlighted
letting you check the impact of your action.
The user can modify the angle by selecting the green arrow directly.
The Rotate dialog box pops up.
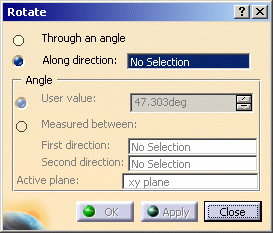 |
The default active plane is the one you have
defined in the Harness Flattening Parameters dialog box at the
beginning of your session. |
|