 |
This task shows you how to create a Mirror Part, from an
Engineering or a Manufacturing Part,
in a separate or existing .CATPart document,
keeping the link to the original .CATPart.This Mirror Part is created
copying and hiding the existing Composites features in a new CATPart,
and by
adding symmetry features to the existing Composites features (only the
symmetry features are visible).
This action is to be used at the end of the
Engineering process or at the end of the Manufacturing process
(not in the
course of a designing process, to create a new part by symmetry from an
existing part).
This Mirror Part keeps a link with the original part, so that it can be
synchronized with the original part, if it is modified. |
 |
- Do not regenerate a 3D Multisplice feature by editing the
feature and validating the edition with OK,
because this would
regenerate the cut-pieces and delete the Mirror features previously
created from the cut-pieces.
- Note that:
- Producibility parameters are transferred to the Mirror Part.
- the following elements are not generated in the Mirror Part:
- Core Samples,
- Numerical Analysis,
- Exploded surfaces
- Preliminary design entities (Composites PD): they are not
usable in the Mirror Part.
As in the manufacturing preparation document,
they are transferred if they are inputs of plies,
but in this case, the
Composites PD node cannot be extended.
However, Full plies
contour and ETBS features will be transferred (like
construction geometries).
|
|
Other elements are transferred as follows:
Input elements of the geometrical features describing the
Stacking:
- They are imported in the Mirror Part,
- They are put in the No Show via their father
Geometrical Set,
- Only the mirrored elements are visible.
Reference surfaces corresponding to plies groups, plies, cut-pieces, ...:
- They are imported in the Mirror Part and put in the No Show
as above,
- A GSD Symmetry feature is created in a new Geometrical Set
named Symmetry geometries,
- The name of the symmetry feature is Symmetry of "Name of the
original surface",
- Each symmetry feature is assigned to the corresponding stacking
element
(plies group, plies without cut-pieces, plies with no associative
cut-pieces, cut-pieces, ...)
 |
In the Mirror Part, symmetry is not applied to a ply with
associative cut-pieces,
but is applied to its cut-pieces. As a
consequence:
- symmetry will not be applied to the reference surface of the
ply,
but will be applied to the reference surface of the cut-pieces.
- if you want to create a core sampling on a ply with associative
cut-pieces,
select the check box Take cut-pieces into account
to generate a correct result.
|
Axis systems:
- They are imported in the Mirror Part and put in the No Show as above,
- A GSD symmetry feature is created in a new Geometrical Set
named Symmetry geometries,
- The name of the symmetry feature is Symmetry of Axis system.x,
- Each symmetry of Axis system is assigned to the corresponding stacking
element
(plies group, plies, cut-pieces, tape, core).
 |
- The symmetry of the axis is created, with no orientation
changes,
- If you want to use another rosette, you must create it and
change the orientations of the plies manually.
|
Composites Parameters:
- They are transferred as is so that the Mirror Part points to the same
material catalog
and uses the same directions.
Stacking:
- The mirrored Stacking elements keeps a link with the original
Stacking element,
- This link is visible using the Edit>Links... command,
- You cannot replace this link but you can deactivate it,
- It is visible through Enovia for Impacted by and
Impacts on.
- Each ply geometry receives a new symmetry feature, named Mirror,
placed after all the composites features (contour, limit contour, skin swapping,
material excess)
coming from the original part,
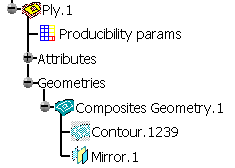
- This Mirror feature is similar to the symmetry features above,
with
the difference that it lays the result of the symmetry on the symmetry
of the reference surface.
- It can be edited.
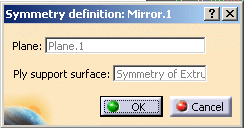
 |
The ply direction remains the same, as the direction is expressed
in the symmetry of the original rosette. |
- Associative cut-pieces (i.e. with Limit Contour features):
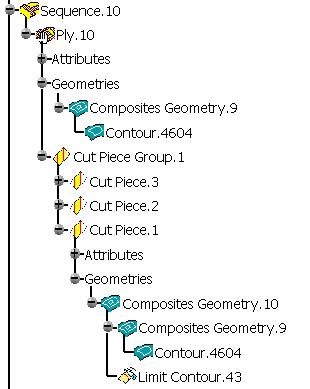
- No symmetry feature is added to the Composites Geometry of the
father ply (here Ply.10),
- A Mirror feature is added at the end of the Composites Geometry of
each cut-piece
(associativity is kept).
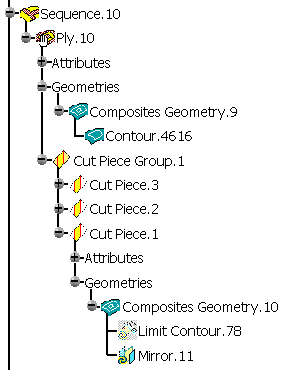
- Non associative cut-pieces (i.e. with datum curves as input to the
cut-piece contour):
- A symmetry feature is added to the Composites Geometry of the father
ply,
- A Mirror feature is added at the end of each cut-piece Composites
Geometry.
- Associative flatten geometry for plies and cut-pieces:
- Producibility paramaters are modified: a GSD symmetry feature is
created for the Seed point,
the seed curve and each curve of order of
drape.
If the Seed point was given by Point indication, a symmetry is
applied to the stored Point indication.
- The Flatten Rosette and the Flatten Contour are updated as they are
computed from the Ply Geometry,
hence from the new symmetry feature in
it.
 |
No symmetry is applied to the location point of the associative
flatten geometry. |
- Non associative (manually created) flatten geometry for plies and
cut-pieces:
- a GSD symmetry feature of the flatten geometry of the original part,
named Symmetry of "name of the feature or datum",
is created in the
Symmetry geometries Geometrical Set.
- This symmetry feature is assigned to the corresponding ply,
cut-piece or tape.
|