 |
This task shows you how to retrieve models designed with V4 Covering
using the following method:
- Create a new V5 catalog.CATMaterial,
- Create a new V5 CATPart,
- In this new V5 CATPart, create the composites parameters and select
the new V5 catalog.CATMaterial,
- Save the CATPart,
- Load the V4 model in session,
- Copy/paste the V4 master in V5 CATPart.
|
 |
The quality of V4 surfaces and curves is an important issue if you retrieve
V4 Covering designs and modify them in V5. |
 |
-
Create a new empty V5 catalog of material.
All the V4
Composites materials will be transferred to this catalog, with the
exception of the warp and weft radius that are no longer part of the
material parameters (they will become parameters of the V5 producibility
feature).
You can also use a non-empty catalog. In that case, the material of the V4
model will be added to the materials already existing in the catalog.
-
Create a new CATPart.
-
Click Composites
Parameters .
The Composites Parameters dialog box is displayed. For more
information, see Defining the
Composites Parameters. Select the material catalog you have created in step 1.
For our scenario, we have used
CompositesCatalog_Mig_V4_V5_Start.CATMaterial. Save the CATPart as V4V5CPD.CATPart.
-
Load the V4 model you want to retrieve in session. For our
scenario, we have used V4-V5.model.
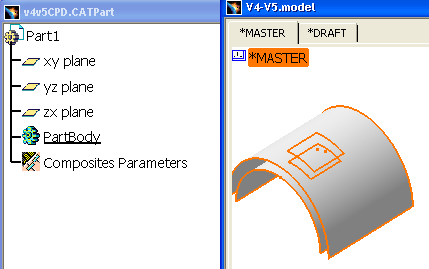
-
Copy/Paste the V4 model master to the newly created V5
CATPart.
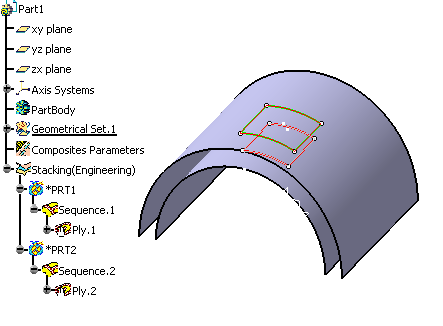 The model created in V4 Covering is now transferred to V5 Composites
Design workbench.
A stacking is created:
- For each part of the V4 model, 1 group of plies is
created. It references the engineering reference shell of the plies.
- In the group of plies, the sequences are created.
- For each ply (or insert):
- The attributes are created (material, direction,
rosette)
- Only the 3D engineering reference geometry is
transferred. (For the insert, the geometry is the solid that is
the result of the trimming of the insert skin with the reference
skin + close surface operation)
- The construction surfaces (GSD trim features) are
stored in a geometrical set named “construction geometries for
inserts”
- The solids (Part Design closed surface feature) are
stored in separate bodies named “ insertxxx solid “.
- A producibility feature is created, that contains
the warp and weft radius and the strategy point (The flatten
geometry can
then be recreated in the V5 Composites workbench).
|
|
 |
- If you want to transfer a V4 model made of several parts and obtain
one V5 CATPart for each V4 model part, you must first explode the V4 model
in several models, and then transfer each model separately.
- If you transfer a V4 model to a V5 CATPart with an existing stacking,
the new ply groups are added to this existing stacking. All the materials
of the V4 model are added to the material catalog referenced by the V5
CATPart.
- If you copy/paste a V4 model several times into the same V5 CATPart,
the ply groups and the material will be duplicated in the V5 CATPart.
- The V4 lay-up geometry (eng or man) is not transferred.
- The V4 flatten geometry (eng or man) is not transferred. You must
regenerate them in V5 (but all the necessary parameters, such as the ply
definition and producibility parameters are transferred.
- V4 models created with a reference skin with an offset superior to 0
are not supported. Such offset skins are not transferred to V5. Only
reference skins with no offset are transferred.
- Transferring V4 Covering models to V5 will reduce the CPU time,
improve the fiber propagation management and improve the workability of
the flatten geometry.
- Manufacturing data are not transferred. You must recreate them, thus
taking advantage of the V5 improvements (manufacturing data are created in
a separate CATPart, synchronization between the engineering and the
manufacturing CATParts, skin swapping/material excess ... features)
|
 |