 |
This section lists the rules
and recommendations to remember when creating catalog slots, endcuts and
small assemblies. |
|
General
- Always explicitly define points and never use implicit points, for
example those at the ends of lines.
- Wherever possible, make selections in the specification tree.
Oriented Planes and Lines
- Never invert the orientation of a plane without first checking
whether or not the plane has children.
In general, plane orientation must be known. This applies in particular
to planes tangent to surfaces, planes offset or parallel to oriented
planes, planes at an angle or normal to an oriented plane if the axis
of rotation is a line of known direction.
- Instantiate user feature SurfaceOrientation.CATPart to
force plane orientation.
- Always work with oriented lines, especially when used as axes of
rotation. When creating lines via the Intersection command, instantiate
user feature CurveOrientation.CATPart to force line
orientation.
User features are to be found in folder
..\OS\startup\EquipmentAndSystems\StructureDetailDesign\SampleData .
Input Geometry
- Do not use input geometry in knowledgeware rules or formula [F(x)].
If you need to do so, duplicate the surfaces using Offset
(0 offset) or Extract
commands and reference duplicated geometry in the rule or formula.
|
|
Taking Advantage of Shape Section Parameters
Using main geometric characteristics of
shape sections rather than creating appropriate input geometry is
recommended. This simplifies the definition of the catalog template and
reduces data size of both the template definition and the features you
place.
The following shape section parameters can be
employed:
- D: shape height
- Bf: Flange width
- Tf: flange thickness
- Tw: web thickness
- Radius1
- Radius2
- Slope
To include section parameters in your template definition, you must:
- Create a knowledgeware parameter of the desired type and named as
below
Shapen_(name of section parameter)
where n is a number identifying the numbre of parts to be
selected by the user when instantiating the feature.
For example, Shape1_Bf
- Create a knowledgeware formula [F(x)] that uses the parameter you
defined.
Shape section parameters are then accessed directly when the user
instantiates the feature. |
|
Sketching
- Always sketch using the Sketch with Absolute Axis definition
command:
- Set the sketch support type to Positioned and select a plane of
known orientation as Reference.
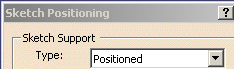
- Set the origin type to Projection point and select a stable
geometric point. Do not select a vertex.

- Set the orientation type to Parallel to line and select an
oriented line.

- Never set distance constraints in the Sketcher. To dimension
distances, create offset planes in the Wireframe and Surface Design
workbench, then set coincidence constraints based on these planes in
the Sketcher.
- Avoid creating circles constrained in tangency. Defining as much as
possible using the Wireframe and Surface Design workbench is
recommended.
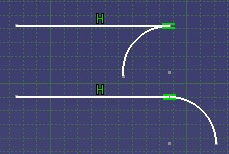
Creating Slots, Endcuts and Small Assemblies
- Always reference input geometry and never part document planes.
- Aways select input surfaces and not surfaces of starter model
plates and shapes.
- Always ensure that the geometric entities are properly ordered, for
example an intersection of two lines must be placed after the two
lines. Use the Reorder command if necessary.
- For slots and endcuts, always reference at least one entity of the
plate or shape that will contain the feature.
- For endcuts, ensure that Split cutting planes are oriented with
respect to geometric elements.
- For endcuts, ensure that the first Part Design feature (pocket,
split, etc.) describing the endcut is the active feature. Select this
component first when creating the template.
|
 |