 |
This task shows how to define a multi-base
retainer, then to route bundle segments using it. |
 |
Open the
multibaseretainer part document.
|
 |
-
Switch to Electrical Part Design
workbench.
-
Define the support as a
retainer on both side of the part.
-
Save the part.
-
Switch to Electrical Harness
Assembly
workbench.
-
Click Geometrical Bundle
and select Product1.
-
Insert your part to this
product, using the contextual menu: Components >
Existing Component...
The File Selection dialog box opens.
Select the part you saved in step 3. |
-
Create a multi-branchable
document using Multi-Branchable Document
.
CATIA switch to Electrical Harness Installation workbench.
-
Create few points to route the
bundle segments, using Point
:
-
Click Multi-Branchable Document
again.
The dialog box opens: |
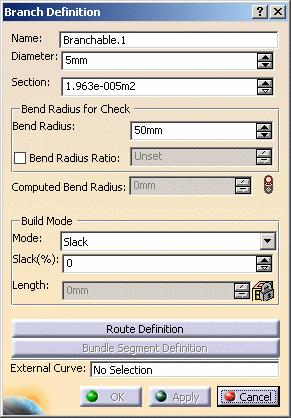 |
Change the parameters according to your needs. |
-
Click Route Definition.
The dialog box opens:
- Click successively the points, as shown below:
|
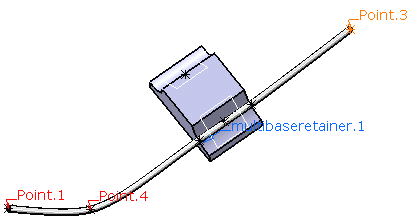
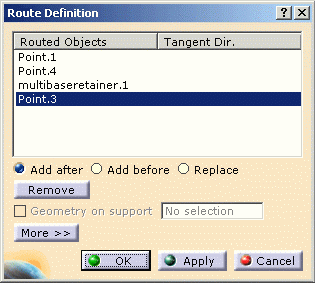 |
|
 |
When you select the retainer, CATIA finds the closest entry point
for the branch, according to the selection point. |
-
Repeat these steps for the second side.
-
Click OK to validate the entries made in the
dialog boxes.
The result looks like this: |
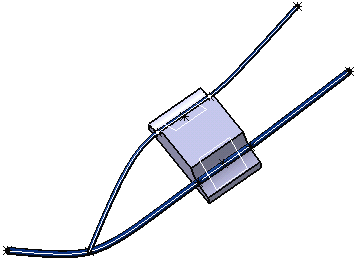 |
|
 |
When you route a bundle segment over a
retainer:
- The bundle segment curve is built as follows:
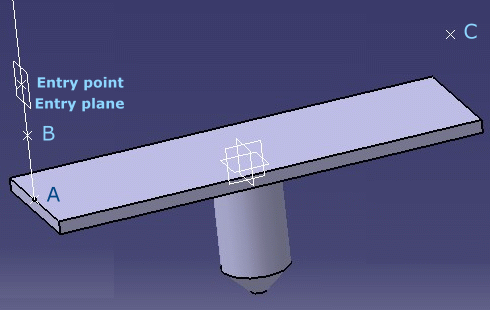 |
- The entry point is published as RefPoint1.
- It is projected to the base plane (RefBasePlane)
as A.
- A line is created between A and the entry
point (RefPoint1).
- A point (B) is created on this line, knowing
that the distance between A and B is
equal to the bundle segment radius.
- The point B is projected to RefPlane2
as C.
- The points B and C are added to the
bundle segment center curve definition. The slack between
these points is ignored.
All the construction objects are sent in
No Show space. |
|
|
- Using retainer and protective covering:
If the bundle segment is protected by a protective covering, the
formula that computes the distance between A and B takes into
account the thickness of the covering.
AB = bundle segment radius + protective
covering thickness |
It is the case when:
- A retainer is added to a protected bundle segment
- A protective covering is added to a bundle segment already
linked to a retainer
- The limit points of the protective covering are modified so
that it is added to or removed from the retainer.
|
|
 |
Note that:
-
Only one section of bundle segment can be taken into
account to be kept in contact with the retainer base plane, whatever the
diameter is. This means that a branch point created in the middle of the
retainer only allows one side of the bundle segment to be updated with
the correct diameter.
-
It is not possible to hold concurrently the properties of
a retainer and a standard support: either the base plane is taken into
account to route the bundle segment or it is the entry point and planes
only. The part below cannot be used as a retainer and a standard support.
|
 |
The retainer component is fully integrated in the Electrical Harness
Flattening workbench. |