 |
In the
previous versions of Product Structure, you could only move rigid components in the parent assembly. Now,
in addition to this behavior, you can dissociate the mechanical
structure of an assembly from the product structure, and this within
the same CATProduct document. As a consequence, you can move the components
of a sub-assembly in the parent assembly. |
|
IFor
the first time, this task recalls the behavior of rigid assemblies, and
then illustrates how to make sub-assemblies
flexible and how constraints defined in the reference document affect them.
Eventually you learn how to analyze the mechanical definition of an
assembly whenever this assembly includes flexible sub-assemblies (and
components attached together, see Fixing
Components Together). |
 |
- When a sub-assembly is flexible, you can apply updates to it, move it
when constrained and set constraints to it.
- When a sub-assembly containing an Assembly Feature, an Assembly
Symmetry or a Reuse Part Design Pattern is flexible, these features
cannot be updated because the flexible mechanism is not compatible with
them.
- What you need to keep in mind is that rigid sub-assemblies are always
synchronous with the original product, whatever mechanical modification
you perform.
Flexible sub-assemblies' components can be moved
individually in the parent assembly, without considering the position in
the original product. Flexible sub-assemblies are not meant to be moved.
Only their components can be moved in the parent assembly. Assembly Move
commands, therefore, do not apply to flexible sub-assemblies. They
either refuse flexible sub-assemblies selection (for example, Manipulate
command) or move flexible sub-assemblies' components instead (for
example, Move by Compass).
Since Release 7, you can edit the constraints defined for flexible
sub-assemblies. The changes made to these constraints do not affect the
constraints defined for the original product contained in the reference
document.
- You can edit the following attributes:
- values
- orientation
- driving/driven properties
- Set of constraints in a rigid sub-assembly can be removed when you
make it flexible.
|
 |
Open the
Articulation.CATProduct and
chain.CATProduct documents.
The product Articulation includes one CATProduct and two CATPart
documents as follows: |
|
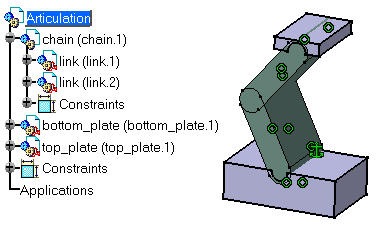 |
 |
-
Drag and drop the compass onto link (link.1), then select
link (link.1) and drag it. The whole chain -and not link.1 only- is
moved.
|
|
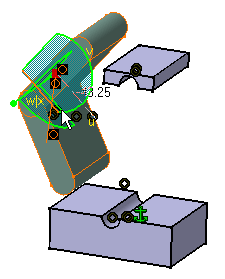 |
|
-
Undo this action to return to the initial state.
|
|
-
To make chain (chain.1) flexible, right-click it and
select the chain.1 object > Flexible/Rigid Sub-Assembly
contextual command.
Alternatively, click the Flexible Sub-Assembly icon
.
|
|
You can notice that the little wheel to the left
corner of the chain icon has turned purple. This identifies a flexible
sub-assembly. |
|
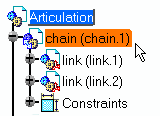 |
|
-
You can now move link (link.1) independently from link
(link.2). For example drag and drop the compass onto link (link.1)
and move it in the direction of your choice.
|
|
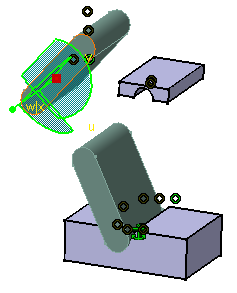 |
|
-
Copy and paste chain (chain.1) within
Articulation.CATProduct. You can notice that the property "flexible" is
copied too.
|
|
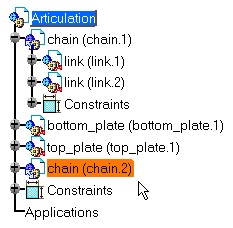 |
|
-
To make chain (chain.2) rigid,
right-click it and select the chain.2 object > Flexible/Rigid
Sub-Assembly contextual command. A message window appears.
|
|
-
Drag and drop chain (chain.2) to clearly see both
instances of chain.CATProduct.
|
|
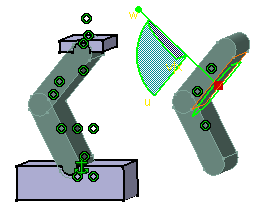 |
|
-
In chain.CATProduct, move link (link.1) using the
compass.
|
|
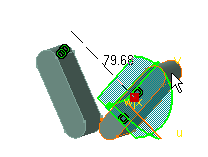 |
|
You can notice that because chain (chain.2) is
rigid, it inherits the new position of the original chain.CATProduct.
Conversely, chain (chain.1) remains unchanged. |
|
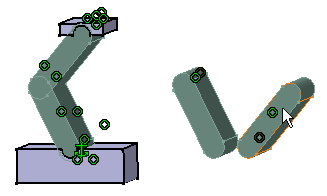 |
|
What you need to keep in mind is that rigid
sub-assemblies are always synchronous with the original product, whatever
mechanical modification you perform.
Flexible sub-assemblies can be moved individually, without considering the
position in the original product.
Since Release 7, you can edit the constraints defined for flexible
sub-assemblies. The changes made to these constraints do not affect the
constraints defined for the original product contained in the reference
document. |
|
You can edit the following attributes:
|
|
-
Set an angular constraint between Link 1 and Link 2 in
chain.CATProduct. For example, set 80 as the angle value.
|
|
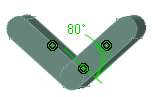 |
|
You can notice that both instances, chain
(chain.2) and chain (chain.1) inherit this constraint. |
|
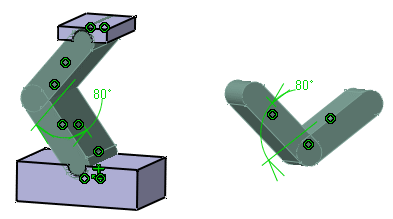 |
|
-
Edit the value of the angle constraint for chain
(chain.1). Enter 100 for example. This new value is specific to chain
(chain.1). Because chain (chain.1) is a flexible sub-assembly, this value
can no longer be affected by changes to the value set in the reference
document.
|
|
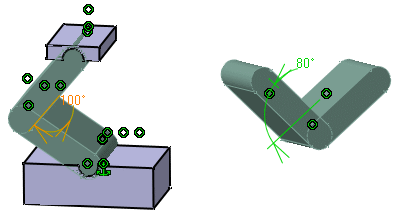 |
|
-
Edit the value of the angle constraint set in
chain.CATProduct. For example, enter 50 as the new value: because chain
(chain.2) is a rigid sub-assembly, and as the constraint value for chain
(chain.1) has been already redefined, chain (chain.2) is the only
sub-assembly to inherit this new value.
|
|
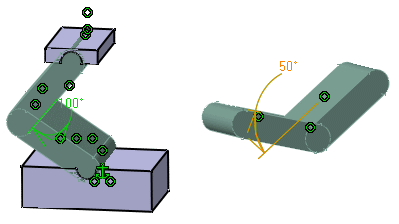 |
|
Mechanical Structure
|
|
-
Select the Analyze > Mechanical Structure...
command to display the
mechanical structure of Articulation.CATProduct. This mechanical
structure looks different from the product structure.
|
|
In Mechanical Structure Tree dialog box, chain.2
is displayed because it is a rigid sub-assembly. Conversely, chain.1 is not
displayed since it is a flexible sub-assembly. |
|
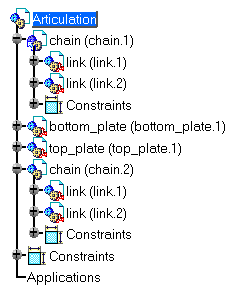 |
|
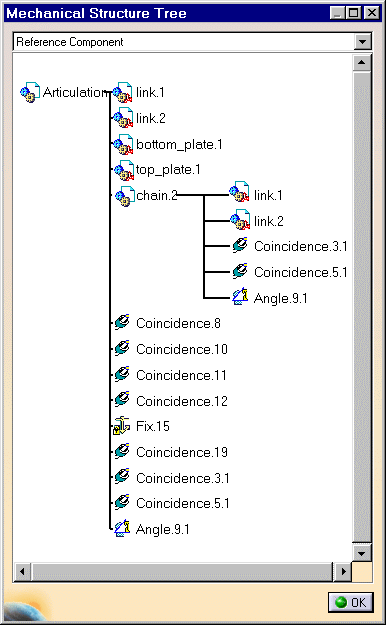 |
|
This display is merely informative. Note that
you can use the Reframe graph contextual command and the zoom capability to
improve the visualization, but also the Print whole contextual command to
obtain a paper document. For information on printing, please refer to
Printing Documents. |