 |
This task explains how to search fillets and
analyze their radii. Once this step is done, you can reconstruct them using
the Fillet Radius Reduction
command, or in some cases, other commands such as fills. However, not
all cases are detected nor can be reconstructed. It is not possible to have an overview of the size of the fillets
of a model: you must be familiar with the model, or work by trial and error.
We recommend that you handle first the fillets that are easy to recognize,
and then that you handle more complex areas. |
 |
- This command is available on a part level only.
If you are working in
an assembly, make current the part containing the surfaces to analyze.
- This command aims at detecting four-sided fillets, with a constant
radius:
- Three-sided junctions of fillets are not detected.
Fillets finishing in a triangle are not detected, at least whenever they
have only three sides.
We recommend that you recreate those fillets as fills.
- The notion of number of sides is based on geometric considerations:
two adjacent edges of the boundary are not in the same side if thy form a
sharp angle. Sometimes, a face may be seen as having three sides, whereas
it has more than three sides, geometrically speaking.
- Fillets with variable radius are not dealt with.
- This command can detect concave or convex fillets with respect to a
stamping or pulling direction:
- You must ensure that the surface to analyze
does not present undercut areas with respect to this direction
(stamping
or pulling direction) otherwise the criterion concave or convex will have
no meaning in the current context.
- You have to choose the best direction for the search.
In most cases,
the direction to use is the pulling direction (plastic injection) or the
stamping direction.
- We strongly recommend that you join the fillets which are adjacent
prior to analyzing the search result, in order to improve productivity.
This can be done by requiring a join of all the candidate fillets, with a
loose tolerance (e.g. 0.1).
This
way all the connected parts of the global join are produced as a single
surface and processing time is reduced.
- We recommend that you use one single interval with the smallest
possible interval values or the detection of fillets. Regrouping fillets of different sizes in a single geometrical set can
make the analysis of the result difficult.
- You can search fillets in Datum mode or in Feature mode. As the
feature mode generates an history, it makes the follow up of possible
errors easier.
- The command may detect faces as candidate fillets, although they are
not fillets:
- This occurs because the geometry analyzed is not precise enough,
- The analysis is done face by face.
Often a visual inspection of the
neighboring faces will tell you whether a face was intended to be a fillet
or not. Therefore, you should remove faces that you know are not fillets
from the selection to analyze.
- Simply click a face to remove it from the result selection.
|
 |
Open
Fillet01.CATPart from the samples directory.
|
 |
-
Click Search Fillets
in the Modify Fillet Radius toolbar. The Search Fillets
dialog box is displayed:

-
Select Surface.1 as the
Surface to analyze.
If needed, multi-Selection is available:
- Click
to display the list of elements selected:
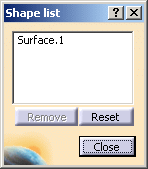
- Click an element in the graphic area or in the
specification tree to add it to the selection list,
- Select an element in the list, and click Remove
to modify the selection list.
- Click Reset to clear the selection list.
- Click Close to end the selection and
revert to the main dialog box.
|
-
You can select as many
Interval lines as you need, and key in the
Minimum and Maximum radius values for those
intervals, but we recommend that you select only one interval.
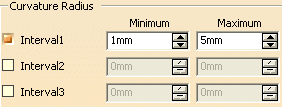
-
If required, set the
search direction, and define the
type
of fillets to search (Concave, Convex or All)
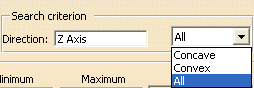
A contextual menu is available to help you define the search direction:
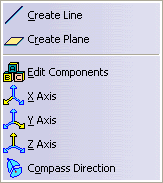
-
Click Apply.
The number of fillets found for each interval is displayed in the dialog
box.
The fillets are highlighted in the corresponding color:
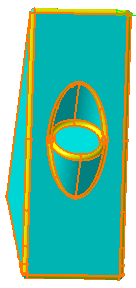
 |
- Double-click a color spot to edit the color.
- Take advantage of the color to analyze the result of the search:
In the image below, it is easy to see that some faces have been
missed by the search,
and that you need to extract them to complete
the fillet.
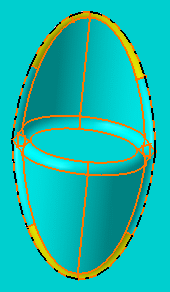
|
-
Click OK.
A geometrical set is created for each interval.
Its name is made of Radius followed by
the radius values of the interval.
The fillets found in a given interval are extracted as RadiusExtract.x
in feature mode
or RadiusSurface.x in datum mode and placed in the geometrical set created for this
given interval.
The fillets are created with the color
corresponding to the interval in the dialog box.
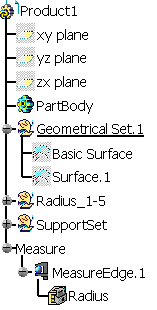
The input surface is sent to the NoShow
A geometrical set named SupportSet is created with the faces of the input
surface that are note candidate fillets, gathered in connected surfaces.
The collection of SupportSet and of all the Radiusxx geometrical sets
represents precisely the entire input model.
|
 |