 |
This task explains how to manage components
given the component constraint type. |
 |
This feature is available on both the board and the manufacturing
panel. |
 |
Open the Scenario3.idf file and the corresponding
Scenario3.lib file from the samples folder.
An Assembly Product document is generated.
|
 |
If the configuration you are using provides access to the
Assembly Design workbench, geometrical
constraints are created between the board and the components, and are
displayed.
Within the assembly, the board needs to be anchored. |
 |
-
Double-click the power-jack constraint shown here in red.
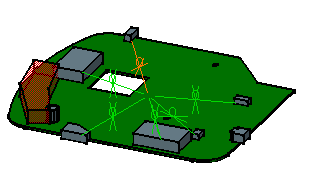 |
The Constraint Definition dialog box
opens. |
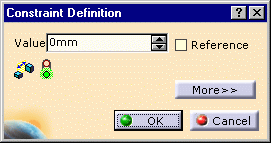 |
 |
The Assembly constraints (geometrical constraints)
linking the components to the board depend on the
component status. |
Component
Status |
Assembly
Constraint |
Unplaced |
No Constraint |
Placed |
Plane to Plane Constraint |
Fixed |
Fixity Constraint |
|
This information is transmitted through
the import file (.idf), the component capability to change location
is then driven by the constraint. Under certain
circumstances, a component status can be modified:
- from unplaced to placed or fixed
- from placed to fixed
but never from fixed to placed or unplaced, nor from placed to
unplaced (in order to keep the information defined in the ECAD
world). |
-
Editing the constraint, using
the More >> button, lets you modify the offset between the
component and the board (IDF 3.0):
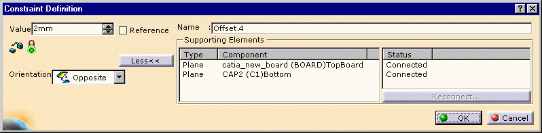 |
The IDF 3.0 takes into account the offset
which represents a mounting constraint of the component onto
the board. The offset is also managed between the board and the
panel. |
|